Pressure treatment for plutonium stockpile
New approach offers potential to convert plutonium into safe, stable forms.
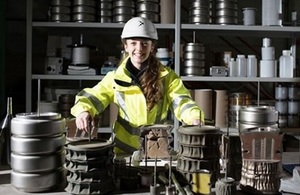
Stephanie Thornber, a materials science and engineering graduate, used both cerium (non-radioactive) and uranium (radioactive) as substitutes for plutonium, to develop glass-ceramic materials on a small-scale HIP machine.
Challenge
To identify and develop immobilisation technologies for UK plutonium stocks that are unsuitable for re-use as a component of new fuel.
Solution
Adapt and refine an existing thermal treatment process: hot isostatic pressing.
Benefits | Consolidation and stabilisation for long-term storage. |
Status | Small-scale demonstrator plant in the development stage. |
R&D driver | Inform strategy |
Research organisation | National Nuclear Laboratory (NNL) |
Timeframe | 2014 to 2018 for PhD, sponsored through the DRP, and from 2018 the DRP project delivered by NNL is ongoing |
Details
NDA holds a stockpile of packaged plutonium, arising from reprocessing spent nuclear fuel over many decades, which need to be managed safely and securely. Options currently being developed are focused on possible re-use in mixed oxide (MOX) fuel for nuclear reactors. However, some of the stockpile is unsuitable and will need to be immobilised for eventual disposal in a permanent facility. An NDA project is under way developing material matrices for immobilising plutonium.
Hot Isostatic Pressing (HIP) has been used in industrial processes for several decades and, if it can be modified successfully, has the potential to convert plutonium materials into safe, stable forms that will be resilient over the long term and be suitable for geological disposal. HIP uses heat and high pressures to consolidate and compress materials inside a pressure vessel, producing dense products ready for storage and disposal.
HIP is flexible, able to process different materials including ceramics and glass ceramics. Ceramics and glasses exist in the natural environment and have properties that would be suitable for nuclear wasteforms, such as long-term radionuclide retention and radiation tolerance.
One of the university PhD projects sponsored through the DRP built on existing Sheffield University investigations into the HIP process. The research by Stephanie Thornber, a materials science and engineering graduate, used both cerium (non-radioactive) and uranium (radioactive) as substitutes for plutonium, to develop glass-ceramic materials on a small-scale HIP machine. The process involved milling glass and ceramic-forming powders with the plutonium substitute, packing these inside stainless steel canisters, before subjecting them to heat and high pressure in the HIP machine to create a solid glass-ceramic product. Stephanie varied the ratio of glass and ceramic-forming materials as well as the glass composition, in order to identify the optimum formulation for the required properties of the final wasteform.
As the UK currently lacks facilities for testing HIP with plutonium, Stephanie spent part of her project overseas with Australia’s Nuclear Science and Technology Organisation (ANSTO), where she was able to substantiate her Sheffield work by making plutonium-containing HIP samples, representative of the target UK waste product.
Results from Stephanie’s research placement supported her inactive work at Sheffield and provided confidence in the materials being considered for immobilisation of the UK’s plutonium stockpile material.
Stephanie’s technical expertise acquired during her PhD studies led to further Direct Research Portfolio (DRP) funding, enabling her to continue the work in a full-time project with the thermal treatment team at the National Nuclear Laboratory (NNL), which has facilities on the Sellafield site. NNL is supporting NDA projects on developing Hot Isostatic Pressing for plutonium disposition, including construction of a small-scale experimental facility.
Stephanie summarised her past work and aspirations for the future of the HIP technology:
Nuclearisation of the process is very complicated.
A lot of work with non-active materials has been carried out on a small scale and we are now working towards constructing a small-scale facility able to produce plutonium-active samples. This will allow us to further substantiate the wasteform development and advance the technology’s maturity for processing radioactive materials. I hope that success of this project will lead to future large-scale demonstration facilities here in the UK.
The treatment process could potentially save billions of pounds from the cost of repackaging hundreds of plutonium canisters that are currently stored at Sellafield, pending transfer to a Geological Disposal Facility.