Snake-arm robot's cutting edge in radioactive environments
An innovative snake-like robot has been developed to cut up items in contaminated or difficult-to-access areas of nuclear facilities.
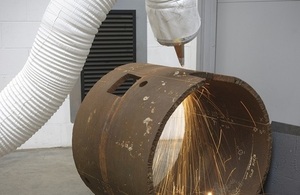
LaserSnake2 can cut through metal that is up to 100mm thick
Background
The NDA’s estate contains large quantities of contaminated metal vessels and pipework. Sellafield alone has thousands of items that must be cut up and removed before the buildings can be decommissioned.
Challenge
Accurate cutting up and removal of radioactive vessels and pipes from areas that are contaminated or difficult to access.
Solution
Remotely deployed and innovative snake-arm robot with purpose-designed lightweight cutting head, for laser powers up to 10kW: LaserSnake2
Benefits
Cheaper, faster and safer than conventional cutting techniques, producing less secondary waste.
Detail
Decommissioning often requires the development of bespoke tools for remote deployment, or for workers in protective air-fed suits to use hand-held tools. Such approaches can be hazardous for the operators (radiologically and conventionally), extremely time-consuming and hence costly.
Laser cutting is faster and far more efficient than conventional cutting techniques and is a well-established process used in aerospace, automotive and defence industries. It is also safer, cheaper and produces less secondary waste. One approach to laser cutting in a remote environment is LaserSnake2, an accurate snake-arm robot with a long reach arm, carrying a decommissioning-specific lightweight laser cutting head with the capability to cut metal up to 100mm thick.
The snake-arm robot is highly dexterous, able to access areas where other robotic technologies would have difficulties. LaserSnake2, now ready for commercial deployment, can be customised to suit a range of conditions, bringing benefits for decommissioning that is usually carried out both remotely and manually.
Sellafield Ltd, as part of its Active Demonstrator Programme, has now completed a cutting demonstration using LaserSnake2 in the radioactive environment of the First Generation Reprocessing Plant. The deployment was the first of its kind on a UK nuclear site, and a significant achievement.
A 5 tonne, double-walled stainless steel vessel, with a 32mm thick inner shell, was entirely and successfully size reduced. This trial has shown LaserSnake2’s capability to remotely cut some of the thickest materials on the Sellafield site, and its potential to access challenging radioactive areas. Other NDA sites could benefit from the LaserSnake2 approach.
A high level of collaboration between project partners, and end-users in particular, has accelerated the demonstration on site and provided valuable insight in how to introduce innovative technologies from other industries.
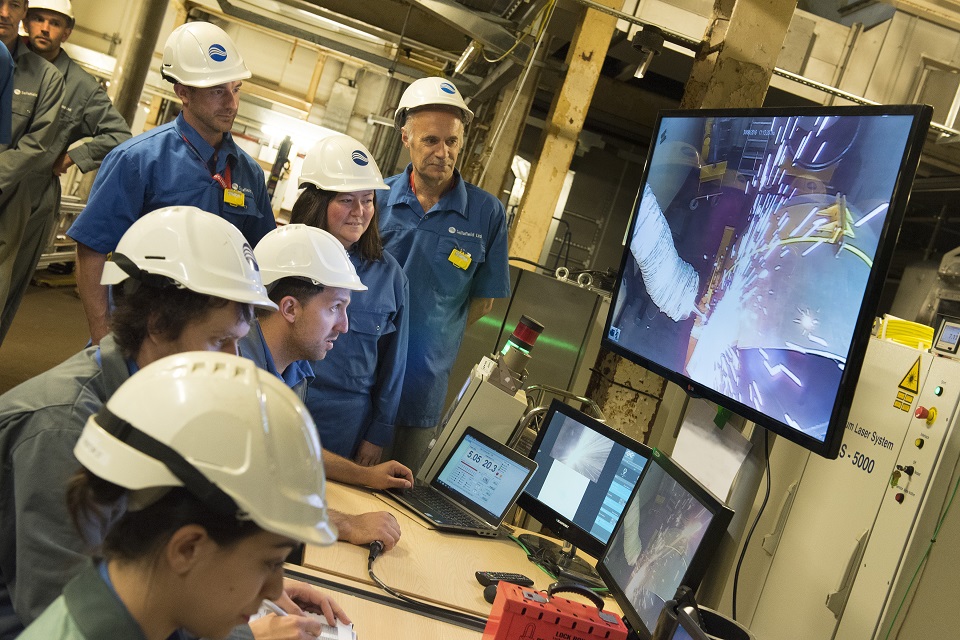
Viewing remotely, some of the development team watch LaserSnake2 in action
R&D approach
The development of LaserSnake2 and application of the associated technologies illustrates the routes for encouraging innovation and technology developments:
- early innovation funding from NDA’s R&D portfolio to demonstrate the effectiveness of lasers in cutting metal and removing contaminated concrete surfaces
- effective leveraging of funding from government-led initiatives to enable the combination of a cutting head with a snake-arm robot and demonstrate its potential as a decommissioning tool in a non-radioactive environment
- leveraging of NDA funding from a collaborative innovation competition with Innovate UK and BEIS to develop LaserSnake2, a new, larger, more accurate snake-arm robot, with an improved laser cutting head. This included demonstration in a radioactive environment
- end-user support to take the LaserSnake2 technology for demonstration at the Sellafield site
- Sellafield Ltd now looking for opportunities to accelerate risk and hazard reduction using LaserSnake2