£150 million investment will help transform UK construction sector
Construction industry in the UK is set for a boost of up to £150 million over the next five years
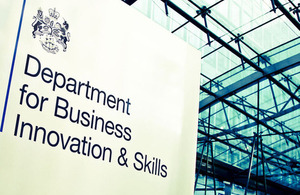
The construction industry in the UK is set for a boost of up to £150 million over the next five years to help reduce construction times, improve quality and make buildings more efficient.
£60 million is being invested through the Technology Strategy Board to support the UK construction industry in designing and developing more energy efficient buildings. The projects are expected to leverage in an additional £60 million of industry investment and £30 million extra funding from across government and other agencies.
Over the last five years £83 million has already been invested in low carbon buildings, saving money for home owners and businesses. Projects have ranged from small businesses like The Facility, developing new energy efficient designs and systems to refit Victorian homes, to multi-national companies like Skanska, developing semi-autonomous equipment such as lift motors and central heating pumps that can tell operators when they need maintenance.
Business Secretary Vince Cable said:
The UK’s new and existing buildings must adjust to a low carbon economy. Investing in energy efficient construction projects is important to help industry and government achieve our aims of reducing greenhouse gas emissions by 50 per cent by 2025. I therefore warmly welcome the Technology Strategy Board’s investment of £60 million in energy efficient technology alongside the private sector.
The construction industry contributes almost £90 billion to the UK economy and supports around 3 million jobs. We are well placed to take advantage of new and emerging energy efficient technologies, commercialise them and then export them across the world.
Over the last five years the Technology Strategy Board has invested £83 million of funding through the Low Impact Buildings Innovation Platform. This has been supported by industry investment of £34 million. The future direct economic benefits of this investment are expected to be more than £1.5 billion and three quarters of the organisations supported are SMEs with fewer than 250 staff.
Director of Innovation Programmes at the Technology Strategy Board David Bott said:
The government’s challenging target of an 80 per cent reduction in the UK’s greenhouse gas emissions by 2050 called for innovation on a grand scale. We’ve been astounded by the enthusiasm with which the projects we’ve funded, through our Low Impact Buildings Innovation Platform, have grasped that challenge.
The resulting new, innovative techniques for both building new, energy efficient homes and for refurbishing existing homes to similar standards have achieved often startling carbon footprint reductions and have the potential to help drive economic growth in this sector.
We’re already identifying the most commercially viable solutions from this programme for further trails at scale, through our ‘Scaling Up Retrofit of the Nations Homes’ initiative and groundbreaking collaborations such as the AIMC4 project.
The announcement comes ahead of the one year anniversary of the launch of the government’s Industrial Strategy. Eleven sector-specific strategies have been produced alongside industry with the objective of achieving strong and sustainable growth across the UK and between industries.
On Wednesday 11 September government and the CBI will host an Industrial Strategy Conference at Warwick Business School. The conference will consider what government and industry have achieved working together over the past year and where more will follow.
Notes to editors:
1.£60 million is being invested by the Technology Strategy Board into the Low Impact Building Innovation Platform. This funds projects that can reduce construction times, improve quality and make buildings more efficient.
2.The Technology Strategy Board is the UK’s innovation agency. Its goal is to accelerate economic growth by stimulating and supporting business-led innovation. Sponsored by the Department for Business, Innovation and Skills (BIS), the Technology Strategy Board brings together business, research and the public sector, supporting and accelerating the development of innovative products and services to meet market needs, tackle major societal challenges and help build the future economy.
3.For more information on Low Impact Building projects, contact Rod Alexander in the TSB press office. Tel: 07500 051 101. E-mail: rod.alexander@tsb.gov.uk.
4.The construction industrial strategy was published in July 2013.
5.The government’s economic policy objective is to achieve ‘strong, sustainable and balanced growth that is more evenly shared across the country and between industries’. It set four ambitions in the ‘Plan for Growth’, published at Budget 2011:
- to create the most competitive tax system in the G20
- to make the UK the best place in Europe to start, finance and grow a business
- to encourage investment and exports as a route to a more balanced economy
- to create a more educated workforce that is the most flexible in Europe.
Work is underway across government to achieve these ambitions, including progress on more than 250 measures as part of the Growth Review. Developing an Industrial Strategy gives new impetus to this work by providing businesses, investors and the public with more clarity about the long-term direction in which the government wants the economy to travel.
Case studies:
‘Retrofit for the Future’ project trials a range of carbon reduction technologies
The Technology Strategy Board funded a ‘retrofit’ pilot project, at Byron square, in Cambridge, to test various high-tech retrofit methods and technologies, transforming a 1940’s steel-framed house into one which achieves an Energy Performance ‘A Rating’.
The project, undertaken by architects PRP and Cambridge City Council, as part of the Technology Strategy Board’s ‘Retrofit for the Future’ programme, incorporated a range of innovative retrofit solutions, including:
- photovoltaics and solar thermal panels in matching frames
- aerogel insulated drylining
- triple glazed windows with thermal control layer
- full LED lighting
- flue gas heat recovery
- waste water heat recovery system
- low-energy decentralised whole house ventilation
- an energy display system – an interactive touch screen interface for education and awareness.
TSB-funded project develops ‘flying factories’ for off-site building construction
A project funded through the Technology Strategy Board’s Low Impact Buildings Innovation Platform has undertaken a fundamental rethink of building processes, developing ‘flying factories’, in order to deliver high-quality, low-carbon buildings at affordable levels.
The project, led by Skanska and involving partners from Modcell, the University of Reading, The South West Manufacturing Advisory Service and the Building Research Establishment, has developed a system of ‘near-site’ manufacture using modern ‘flying factories’.
These ‘flying factories’ allow the structures to be built in controlled conditions, removing the potential effects of bad weather and other on-site hazards, and speeding up the assembly of the building on site.
Combined with virtual-reality-enabled supply chain management and process improvement, the system provides a 28 per cent reduction in cost per square metre and 30 per cent shorter programmes, providing a higher-quality and a more predictable build cost.
The AIMC4 Consortium
AIMC4 is a unique partnership of companies, created in 2009 to research, develop and pioneer the volume production of the low carbon homes for the future. The ground breaking project is overall worth £6.4 million, of which half has been invested by the Technology Strategy Board and half by the consortium.
Challenged with designing and delivering homes to the Code for Sustainable Homes, Level 4 energy performance, through innovative fabric and building services solutions only, the project has deliberately trialled a wide range of technologies –to suit the built form and location – the lessons of AIMC4 can be transferred to deliver desirable low carbon homes in any location.
The consortium has now successfully delivered and sold 17 AIMC4 homes, at 5 very different locations across the UK – Aberdeen, Edinburgh, Preston, Corby and Epsom. These are desirable homes designed to perform and to meet consumer needs for homes that are low energy, affordable, low maintenance and offer a modern flexible lifestyle.
A model of collaboration, the partnership developed the idea of ‘Supplier Sandpits’, designed to give companies from SME’s to multinationals and start-ups an opportunity to showcase and further develop possible solutions to the new challenges through a series of highly interactive intensive workshops designed to stimulate collaboration and innovation.
The consortium members comprise developers Stewart Milne Group, Crest Nicholson PLC and Barratt Developments PLC, H+H UK Ltd an innovative supplier of Aircrete concrete products and the Building Research Establishment (BRE) advising on innovative solutions.
Achieving the AIMC4 goal will not only assist in meeting the government target of zero carbon homes by 2016, but will reduce costs, create a new UK supply chain, generate new build systems and processes and ensure homes are designed that meet consumer needs.