Installed: the Sellafield space saver set to save billions
The first fuel has been placed into a space-saving storage rack at Sellafield set to save billions of pounds.
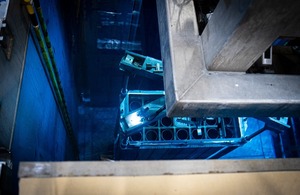
Known as the 63-can rack, the container allows the Thorp pond to store 50% more spent nuclear fuel.
That means Sellafield can safely store all the fuel expected from the UK’s currently operational nuclear power stations.
Without the rack, a new storage pond would have to be built, potentially costing billions of pounds.
The rethink was required because Thorp needs to store more fuel than previously thought.
That’s because the UK no longer reprocesses spent fuel, but instead stores it underwater prior to disposal.
Roddy Miller, Sellafield Ltd’s nuclear operations director, said:
From the birth of the nuclear industry in the 1940s, Sellafield has always proudly served the nation.
These days, our job is to create a clean and safe environment for future generations by safely managing our nuclear legacy.
This includes receiving and storing the UK’s spent nuclear fuel, helping EDF Energy to continue generating low carbon electricity for homes and businesses.
Since the change of approach to managing spent fuel, it was clear we would need to innovate to be able to safely store everything we need to in the Thorp pond.
These racks will increase fuel capacity from 4,000 tonnes to 6,000 tonnes, meaning we can accommodate all current and future arising, negating the need for a new storage facility.
It’s a great example of collaboration between ourselves, the Nuclear Decommissioning Authority Group, EDF Energy, and our supply chain. Everyone involved should be proud of their contribution.
The rack has been 16 years in the making and represents a success story for UK manufacturing.
Weighing 7 tonnes and standing 5.5 metres high, the stainless steel containers are being built by a consortium of Cumbrian manufacturers and Stoke-based Goodwin International.
Between them, they will manufacture 160 racks. Another 340 racks will be needed in the future.
It’s a key contract for Carlisle-based Bendalls Engineering and Workington’s West Cumberland Engineering, who head up the Cumbria Manufacturing Alliance making half the racks.
Transfers of fuel from the old containers into the new racks started during the summer.
Operators who previously fed fuel into the reprocessing system are now placing fuel into the new racks.
Because fuel will be stored for longer than was originally intended, the pond has required other alterations including raising the pH level to avoid corrosion and installing new cooling capacity.