Made in Cumbria: the nuclear storage solution set to ‘rack-up’ the savings
A Cumbrian collaboration has manufactured a world-first nuclear space saver.
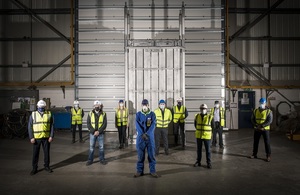
Bendalls Engineering Ltd is one of three companies which have delivered the first ‘Hybrid 1 63 Can Rack’ to Sellafield.
And the innovation could save the UK £2 billon in nuclear decommissioning costs.
Workington’s West Cumberland Engineering Ltd, Bendalls Engineering Ltd, of Carlisle, and TEAM Industrial Services, which has bases in Kendal and Carlisle, have delivered the first ‘Hybrid 1 63 Can Rack’ to Sellafield.
At a stroke, it triples the number of fuel cans that can be held in one underwater storage container.
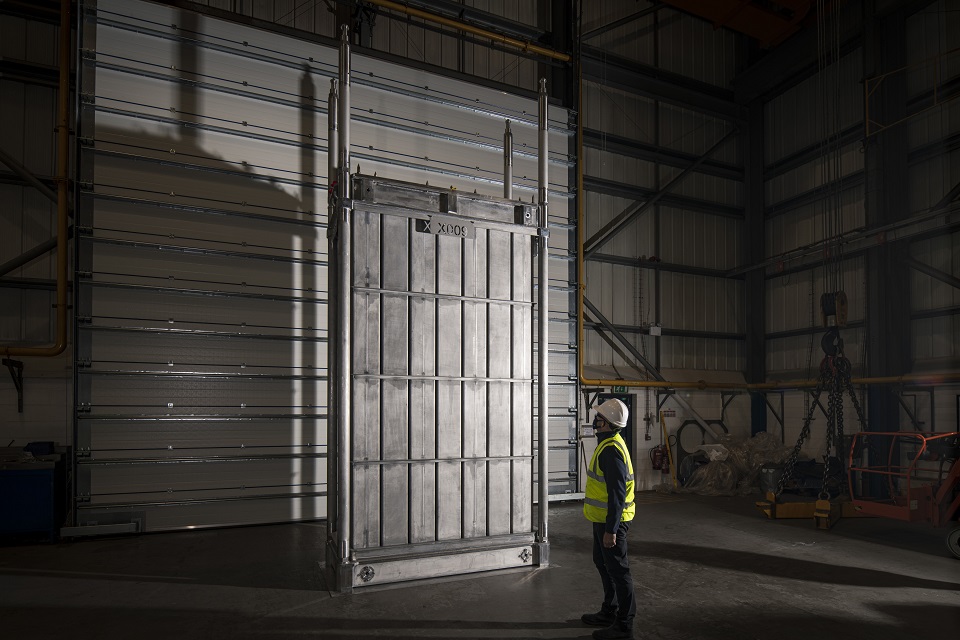
The 63 can rack, Hybrid 1 design can store 63 fuel cans in one rack.
It’s an important breakthrough because space is limited in the UK’s only storage pond for Advanced Gas-cooled Reactor (AGR) fuel, at Sellafield’s Thorp plant.
It will also help reduce the time it takes to remove fuel from AGR reactors, saving potentially £2 billon on decommissioning costs.
There are currently 7 AGR power stations in the UK, all operated by EDF Energy.
The project has also had input from Sellafield Ltd, EDF Energy, the Nuclear Decommissioning Authority, and Direct Rail Services.
Andrew Pringle, AGR operating Programme Manager for Sellafield Ltd, said:
It has been a great example of collaboration.
As the AGR stations are coming to the end of their operational lives, we have to look at how we store the fuel.
The current storage compartments can hold up to 20 fuel cans. We knew this wouldn’t be enough. So for a number of years, we’ve been working to design a solution.
The answer is the 63 can rack, Hybrid 1 design. As the name suggests, it can store 63 fuel cans in one rack.
The first rack has been placed in the Thorp Receipt and Storage Pond. We have a further 15 to follow and then the Hybrid 2 Rack, which is an enhanced design to optimise manufacturing, will be used to store fuel cans.
This will ensure we can support ongoing AGR receipts and enable accelerated bulk defueling of the AGR reactors from 8 years to 3.5 years. That’s good news for the tax payer as it will potentially save around £2 billon in decommissioning costs.
The Cumbrian collaboration will manufacture 8 of the Hybrid 1 design racks in total. A further 8 are being produced by Grahams Engineering Ltd, of Lancashire.
A contract opportunity to manufacture the Hybrid 2 design racks has been published on Sellafield Ltd’s CTM system (ref 12613.) Contract award is expected in August 2021.