North businesses are powering Sellafield clean-up
A chain of northern companies has begun manufacturing containers to store radioactive waste from one of the UK’s most important nuclear decommissioning projects.
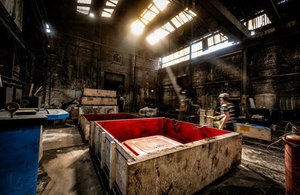
The first steps have now been taken on the production of the first of the 33-tonne metal containers
Businesses in West Yorkshire, Lancashire, and Cumbria are joining forces to produce self-shielded boxes which will store legacy waste from the First Generation Magnox Storage Pond at Sellafield.
The 66-year old open air pond was originally used to store nuclear fuel from the UK’s first generation of nuclear power stations. It has been prioritised for clean-up by the Nuclear Decommissioning Authority.
The clean-up work requires the manufacture of hundreds of boxes to store material taken out of the facility.
The final number needed is still to be decided but the work could ultimately be worth between £50m and £100m.
The first steps have now been taken on the production of the first of the 33-tonne metal containers
North businesses are powering Sellafield clean-up
They began life in Brighouse, near Huddersfield, where expert craftsmen at Arthur Jackson & Co made intricate wooden ‘patterns’ to create moulds into which molten iron can be poured to cast the boxes.
Next, the Shakespeare Foundry, in Preston, made the mould and poured the iron, which takes a month to cool. The mould was recently broken away to reveal the basic structure of the box inside.
The next destination will be Eaves, a Blackburn-based company, which will carry out precision machining to make holes for process ports, filters and bolts.
Later this year, the final step of the first boxes’ journey will be to Workington-based TIS, where seals, filters, process ports and bolts will be assembled before they are transported to Sellafield.
Once the boxes are on the site they will be filled with waste and stored in a newly-constructed interim waste store from early 2019.
Dorothy Gradden, Head of Legacy Ponds at Sellafield, said:
The arrival of the waste boxes on site will be another landmark in cleaning up the most hazardous facilities on the Sellafield site.
This is the Northern Powerhouse in action - a chain of manufacturing specialists, some of whom are delivering products for the nuclear industry for the first time, are stepping up and helping us achieve one of the most important projects in decommissioning the UK’s civil nuclear legacy.
All of this work has been managed by the primary contractor, Westinghouse (with its UK base in the North West of England) which won a multi-million pound contract to manufacture up to 750 of these self-shielded boxes.
Tremendous progress has been made to remove fuel and sludge from the pond since retrieval work began in April 2016.
The self-shielded boxes will also be used to store skips of zeolite, a filter mineral used to absorb radioactive particles from the pond water in order to make it safer for nuclear workers during the plant’s 30-year operational life