Sellafield robots leading an evolution in nuclear decommissioning
ROBOTS at Sellafield are delivering breakthroughs at the site with learnings shared with the wider nuclear industry.
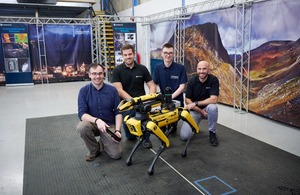
From left to right: Lawrence King, Calvin Smye, Callum Taylor and Deon Bulman from Sellafield Ltd
The use of robots is increasingly commonplace at Sellafield, helping to make work safer, faster, and cheaper, and delivering valuable lessons for other nuclear sites in the UK.
Adopting new and innovative ways of using these developing technologies continues to change the way we think about clean-up and decommissioning.
Sellafield’s remote operated vehicles (ROV) department based at the Engineering Centre of Excellence in Cleator Moor, West Cumbria are at the forefront of taking standard equipment and software and adapting it for a range of on-site needs.
They recently became the first in the world to use a light detection and ranging (LiDAR) laser scanning device on a ROV in a high radiation environment, allowing the robot to navigate and build a 3D image of the hazardous area and removing the need for humans to enter.
Calvin Smye, ROV equipment engineer, Sellafield Ltd said:
Everything we are using is off the shelf but by adding different payloads, like a LiDAR senor and a radiation monitor, we are adapting them to deliver for our business.
Since the introduction of this technology we’ve really been at the forefront of testing it and adjusting it to our needs and are now leaders in the nuclear industry for applying it.
We’ve seen supply chain colleagues deploying the same technology at other nuclear sites following our success.
The robot in question was Spot the robot dog, now a familiar sight on many jobs at Sellafield, from inspections of buildings and equipment to the sorting and segregation of wastes.
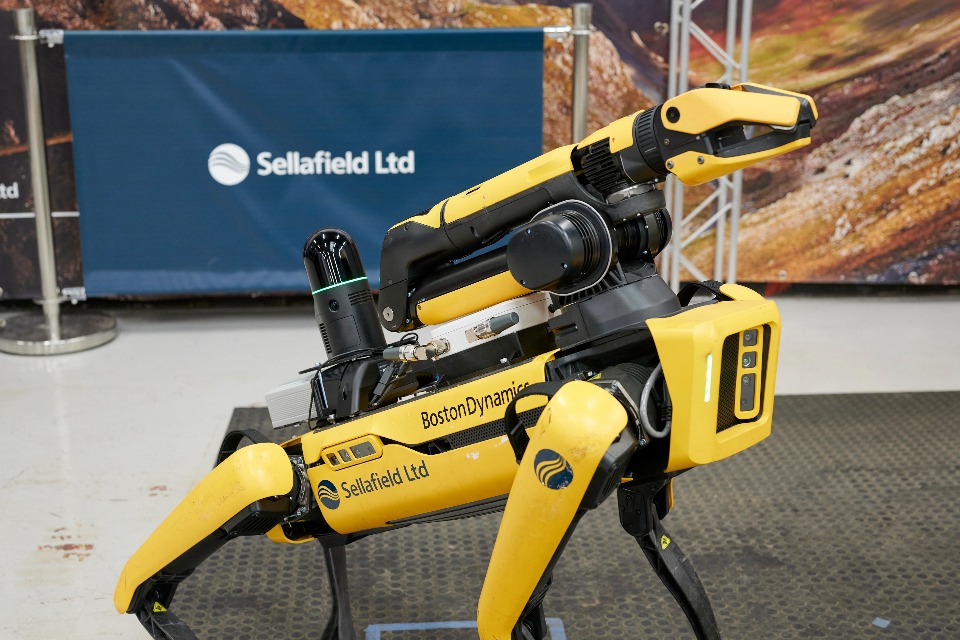
Spot the dog with the LiDAR scanner
Spot’s capabilities were shared with industry colleagues during a live demonstration at one of the site’s oldest buildings, Calder Hall.
Like many buildings built in the 1950s, Calder Hall has areas where asbestos is a known hazard, making them inaccessible for humans and difficult to decommission.
AtkinsRéalis, supported with some of the ROV teams equipment and documentation, recently utilised Spot to conduct a livestreamed inspection – via the robot’s on-board camera – and build an accurate understanding of the condition of the area and how best to clean it up.
The same robots are now being used across other Nuclear Decommissioning Authority sites in the UK, including at Dounreay in Scotland, demonstrating how learning is being shared to deliver better outcomes.
But it’s not all robot dogs, the team has also used an IPEK crawler robot – commonly used for sewer pipe inspections – to inspect the structural integrity of pipework from up to 250 meters away.
Sellafield is also exploring the use of ROVs to detect potentially dangerous gases in work areas before humans are sent in, much like the canaries used in coal mines over 200 years ago. They’ve recently conducted their first trial using a dosimeter designed by the Radiometrics Systems Group.
Deon Bulman, ROV equipment programme lead, Sellafield Ltd said:
The adoption of new technology is progressing at pace at Sellafield as people start to see the benefits.
The technology is here to support people, not replace them, and those that embrace it soon see the advantages.
If we can do one task that removes the need for a person to enter a hazardous area, that’s a win.
As well as improving safety, ROVs also bring advantages in delivering significant cost savings while improving operational efficiency.
Rav Chunilal, head of robotics and artificial intelligence, Sellafield Ltd said:
The use of ROVs at Sellafield marks a significant milestone in our commitment to safety and efficiency.
These cutting-edge robots allow us to access dangerous and challenging areas remotely, removing humans from harm’s way and saving time and costs for maintenance and inspections.
By embracing remote technologies, Sellafield is pioneering a new era in the nuclear industry and setting a standard for excellence in decommissioning operations worldwide.