Annual Research and Development Review
Published 28 September 2020
Annual Research and Development Review
This report presents:
- R&D managed by Sellafield Ltd value streams driven by the needs of the business
- Longer term R&D focussed on opportunities for innovative technologies, tools and techniques to reduce costs, improve safety and reduce timescales
- Collaborative R&D with a wide range of supply chain companies, organisations and universities
- Some of the specialist staff from the research community working in and with Sellafield Ltd’s technical teams
Foreward
We are seeing radical change at Sellafield, across the site – from the way we work, physically and virtually, to the new ideas, infrastructure and facilities being introduced to deal with the challenges of our decommissioning mission.
Our research and development teams are at the forefront of that. 2020 has impacted us all.
Sellafield, like everyone else, was profoundly affected by the lockdown implemented to combat the spread of COVID-19, and we know we will continue to see its effects for months, if not years to come.
But throughout it all, we continued to work on new ideas, whether we were at home, in our offices or on the site itself. It is said that necessity is the parent of invention and I am sure that in future editions of this report, we will be talking about the new ideas which were formulated and worked on from kitchen tables and almost-empty offices, discussed and polished through online video chats, and implemented despite the limitations of strict social distancing.
These R&D professionals – from inside and outside the nuclear sector, working at and with Sellafield to solve problems – are among the best in the world. And they need to be, to understand and create and ultimately implement solutions to the complex issues only a 70-year-old nuclear facility built on a constricted site can offer, and then try to anticipate what the next problem might be.
It is a fascinating business to be in, and I hope this report gives you an insight into the incredible, diverse, historic and ground-breaking world we operate in.
Rebecca Weston
Chief Operating Officer, Sellafield Ltd
Introduction
Welcome to the 2019/20 Research and Development Review featuring highlights from our ongoing technical programmes that will enable our mission to safely remediate the Sellafield site.
We have prepared this report while the world is in the midst of the COVID-19 pandemic and hope that during this time we find you well.
Over the past few decades operations at Sellafield have strived to reduce the environmental impact from radioactive discharges to near zero.
As we approach the completion of reprocessing and the site changes to decommissioning activities, we are increasingly focussed on environmental remediation and waste management.
In recent years we have placed emphasis on reducing hazards from ageing waste storage infrastructure which could potentially have a significant impact on the environment. We are now moving to a phase where we want to reduce the impact of all of the activities we undertake.
Research and development (R&D) is fundamental to the delivery of our mission, new technologies and techniques can improve safety, security and reduce costs, timescales and environmental impact.
Our R&D programmes are aligned to the Nuclear Decommissioning Authority’s (NDA) Grand Challenges. This year we have included a number of waste reduction initiatives, such as alternative treatment options and improved waste sentencing, monitoring technologies, techniques that remove the human away from harm and a section on environmental management which explains how R&D supports environmental compliance at Sellafield.
The challenge we have isn’t just to minimise our impact on the environment, but to work sustainably and to be responsible for our role in our society. Actions can be taken every day to reduce consumption of resources and work more sustainably.
Our 2019 Dragons Den style competition showed us just how creative we can be, identifying 3 initiatives featured in this report which will have a positive effect on our environment.
The COVID19 crisis has been a challenge for everyone, people have adapted and responded well to the crisis. It has shown us that with the benefit of remote working, with the aid of digital technology, we are able to achieve our objectives in a way that could reduce our environmental impact.
I hope you enjoy the review and do not hesitate to get in touch with questions and ideas.
Andrew Cooney
Technical Manager, Sellafield Ltd
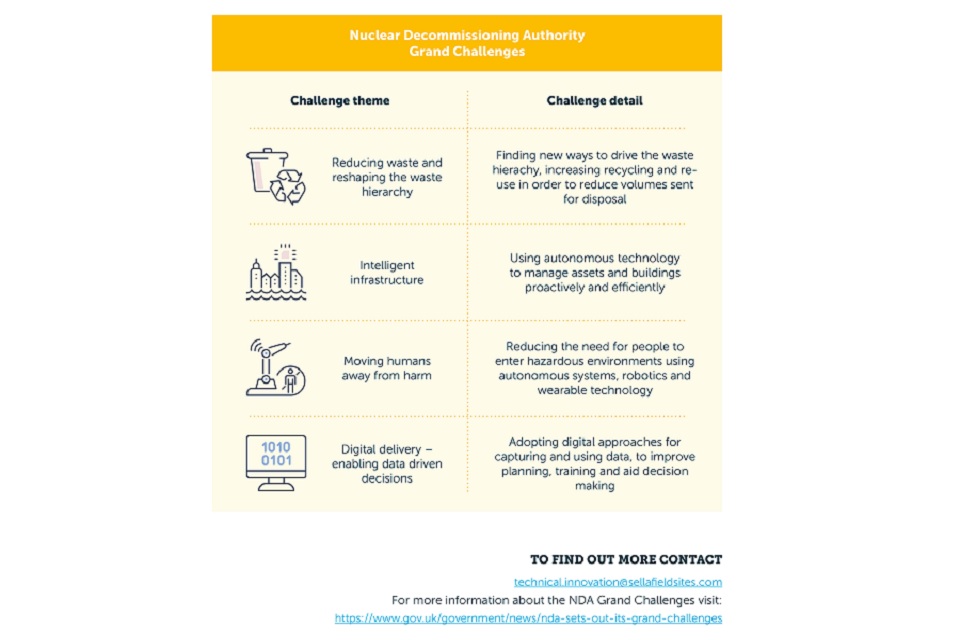
Technical case studies and staff profiles
Central Technical
Science – the first step in any development cycle
Integrated Research Teams
Hydrogen detection in storage facilities - Steve Hepworth, Senior Scientist
Wall cleaning in legacy facilities - Chris Ballard, Robotics and Artificial Intelligence IRT Lead
Alternative treatment options for future waste challenges
Robotic glovebox operations
Effluents modelling - Felipe Basaglia, Technical Manager
Dawn Watson, Head of Strategy and Technical Analytical Services
Horizon scanning - Andres Alfaro, Emerging Technology Team
Dragons’ Den style competition
Game Changers
Frank Allison, CEO, FIS360 Ltd.
Spent Fuel Management
In-situ container monitoring in the Fuel Handling Plant
John Rowley, SFM Ponds Technical
Dan Pocock, Technical Support
High Level Waste Plants technical programme
SIXEP strategy
Andrew Riley, Effluents Strategy Lead, SFM Technical
Toni Warwick, Senior Technical Advisor, SIXEP Technical
Ian Armstrong, Magnox Reprocessing Technical Manager
Special Nuclear Material
The Special Nuclear Material R&D Programme
Robert Bernard, Senior Technology Manager
Ewan Williams, degree apprentice
Retrievals
Corrosion of uranium in encapsulated products
Development of in-situ monitoring for waste packages
Development of ex-situ monitoring for waste packages
Stephen Farris, Cement and Process Centre of Expertise Lead
Charlotte Jackson, scientific degree apprentice
Remediation
Reducing the size of gloveboxes for disposal
Waste processing of legacy plutonium contaminated material
Characterisation of borderline intermediate level waste
Chris Hope, Remediation Capability Development Manager
Alan Cardwell, Alpha Active Demonstrator Manager
Remote characterisation of inaccessible areas
In-situ analysis of lead
Dan Fielden, Waste Capability Development Manager
James Sant, Capability Development Team Member
Remediation Capability Development Team
Environmental Management
How R&D supports environmental compliance at Sellafield
David Smith, Environmental Strategy and Development Specialist
Richard Hill, Environmental Specialist
Simon Booth, Environmental Specialist
Central Technical
The Central Technical team is responsible for the R&D programmes that address the medium to long-term needs of the business.
The key science and technology themes where there are opportunities for the development of innovative technologies, tools and techniques, to reduce costs, improve safety and reduce timescales are managed by Integrated Research Teams (IRTs).
The R&D programme is focussing on:
- science, including sub-themes on materials, process chemistry, particulates, data and environment
- waste treatment, conditioning and packages
- condition monitoring and inspection
- in-situ measurement and analysis
- post operational clean-out
- protecting people
- robotics and artificial intelligence
- future asset management
The team is also responsible for representing Sellafield Ltd on the various university engagement programmes and ensuring coordination across the business.
It also manages the Game Changer programme and the horizon scanning capability featured in this chapter.
Science - the first step in any development cycle
Science is at the beginning of any innovation cycle and the Science IRT (sIRT) is Sellafield Ltd’s approach to the management of the ongoing research and underpinning science programme.
Activities naturally fall within the academic environment and innovative companies and due to the nature of the work tends to be at the lower end of the technology readiness levels (TRL) scale.
It is also important to note that research and underpinning work tends to be longer term, with delivery often ten years in the future.
Sellafield Ltd has identified and documented its needs and opportunities and the science programme has been organised around these. It is managed by the sIRT and is part of the overall science and technology programme illustrated in this document.
The technology IRTs also illustrated, manage higher TRL R&D. More about the role of IRTs can be found on in this document.
2019/20 was a year of growth for sIRT, it continues to support:
University programmes
GREEN (Growing Skills for Reliable Economic Energy from Nuclear) Centre for Doctoral Training.
TRANSCEND (Transformative Science and Engineering for Nuclear Decommissioning).
CINDe (Centre for Innovative nuclear Decommissioning).
Sellafield Ltd collaborates with its key partner the National Nuclear Laboratory (NNL) on scientific projects, a relationship that goes back many years and a natural fit since NNL also conducts fundamental research, manages the NDA’s PhD bursary scheme and has partnerships with many universities.
Sellafield Ltd centres of expertise
These include materials, effluents, reactive metals and flammable gases all of which have university partners. The Flammable Gas Centre of Expertise (CoE) partnership was retendered and awarded to London South Bank University.
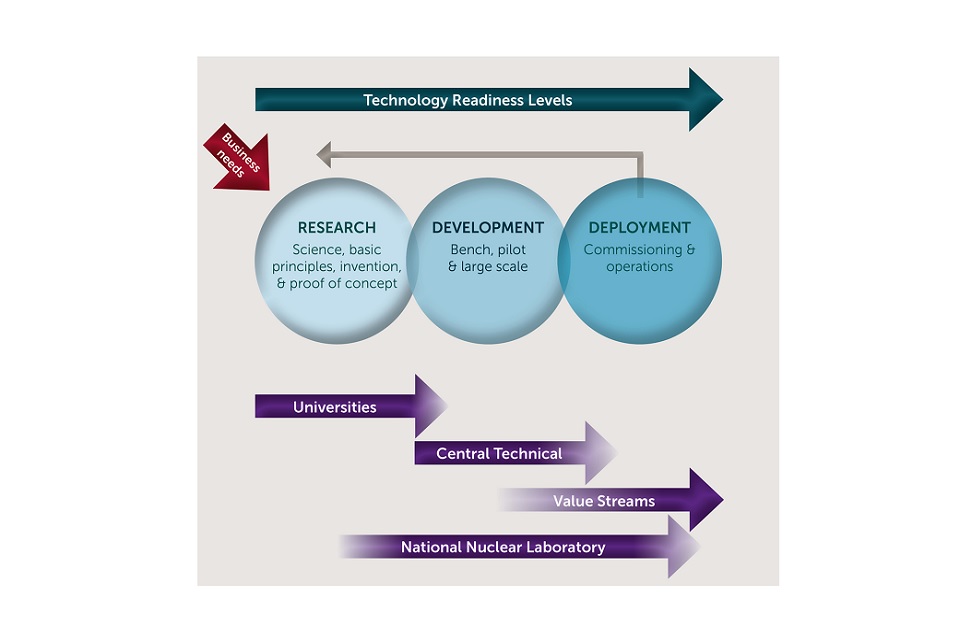
Sellafield Ltd doesn’t just have academic partners, in 2019/20 the company agreed a partnership with Studsvik which will provide access to global information and fundamental research in spent fuel storage.
The science programme
- maintains a steady flow of new ideas through to development
- provides highly educated post graduates with a good understanding of the nuclear industry
- is an innovative and unconstrained workspace
- is the first step in implementing any commercial off-the-shelf (COTS) or modified off-the-shelf (MOTS) products
- attracts significant leverage from multiple sources
- gains access to expertise from the wider scientific community
To find out more contact, Simon Malone technical.innovation@sellafieldsites.com
Integrated research teams
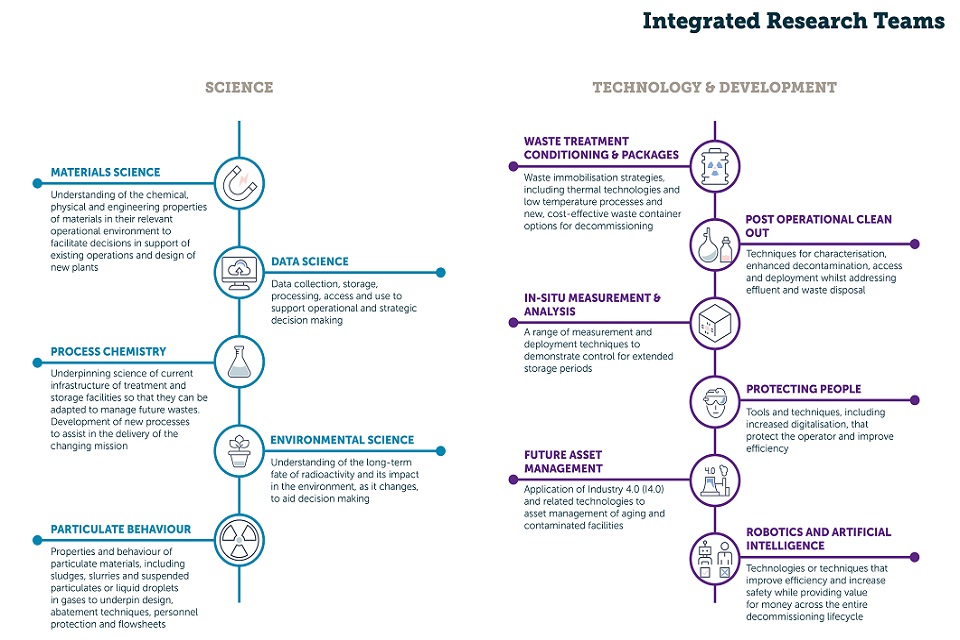
The role of central technical is to ensure transformational solutions are delivered into the value streams across a range of R&D topics.
Within central technical, a number of IRTs provide a collaborative approach with input from the end-user to deliver technologies to address decommissioning challenges.
An IRT:
- understands challenges and coordinates R&D
- delivers R&D which provides value across the enterprise
- is a space for more speculative longer term, high value R&D
- helps the value streams engage with the wider external R&D community
- finds technology in the supply chain that can be of use to the value streams and helps them demonstrate the value of this technology
The individual IRT subject areas can be found in this document for both science and technology. The longer term R&D programmes managed by the IRTs, complement the shorter term R&D programmes delivered by the value streams as illustrated below.
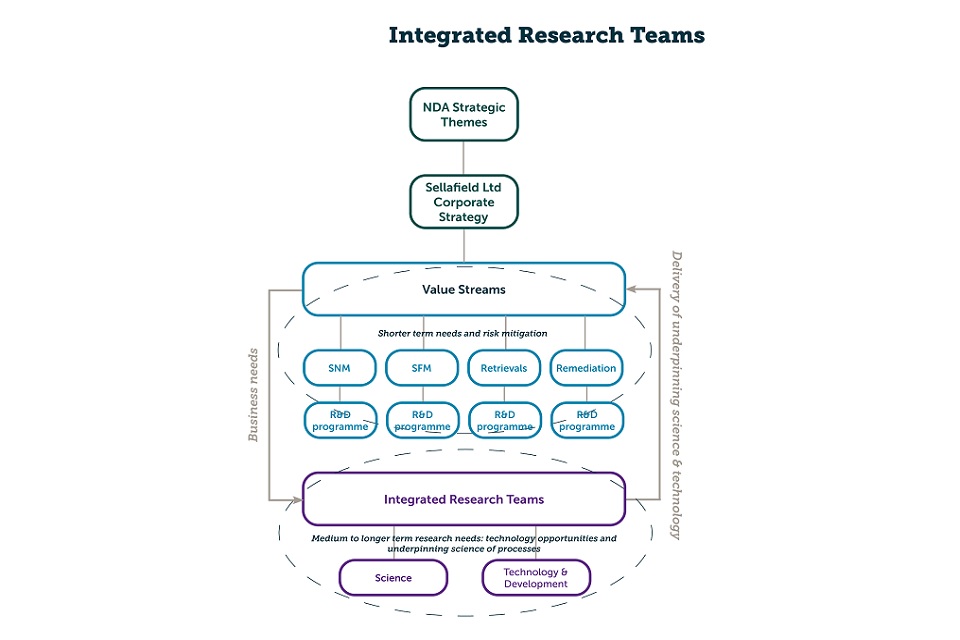
Hydrogen detection in storage facilites
Waste packages are expected to be stored on the Sellafield site for long durations and throughout this time they need to be monitored to demonstrate that they are evolving in line with predictions made about their behaviour.
The wastes inside some packages, such as Magnox Swarf Storage Silo (MSSS) boxes stored in the Box Encapsulation Plant Product Store (BEPPS), can produce hydrogen as a result of chemical interactions with water and measuring this is the best way to understand that the reactions are within predicted parameters.
In a store with high dose levels and where packages are packed in columns, nine boxes high, access for monitoring purposes becomes very challenging and therefore a solution has been developed that can measure hydrogen from a distance with the added benefit of using existing infrastructure already present in the store.
Fraunhofer Centre for Applied Photonics(FCAP) took up the challenge and developed a system for the detection of hydrogen using Raman spectroscopy with the proof-of-concept experimental technology ready in 2019.
Hydrogen molecules are difficult to detect, this technology uses lasers to excite the hydrogen and measures the scattered light from the molecules that it interacts with.
This is Raman emission and the frequency of this light is specific to the molecule that it is scattered from, thus enabling concentrations of hydrogen to be calculated.
Raman spectroscopy is a long established technique which has benefitted from many technical advances throughout its development.
The reason rapid progress has been made now is due to advances in the speed of electronics. For example, pulsed lasers, gated detection systems and avalanche detectors now make this technique viable for the application.
Work planned on the project in 2019/20 was initially focussed on the long-range detection of hydrogen (>30m) around the filters of stored MSSS waste containers but following a change in business priorities, work switched to the measurement of hydrogen at a shorter range (<2m) in older special nuclear materials (SNM) storage facilities.
In February 2020, following a complete system redesign and many challenges overcome, a prototype system hydromap was tested at the NNL’s Workington Laboratory.
On its first active deployment, the system was confirmed as working and hydrogen levels were measured to be below the limit of detection in 20 channels of a special nuclear material store, where previously this was not possible.
Hydrogen detection in storage facilities
Project - Hydrogen detection using Raman spectroscopy
Benefits
The work carried out during 2019/20 demonstrated that hydrogen can be measured in situations where it is impossible to deploy standard hydrogen detectors:
In the Box Encapsulation Plant and Product Store environment this technology will enable early detection of any changes in chemical reactivity from all packages. If increased levels are detected this may lead to early interventions thus avoiding costly rework of packages.
In the event of reduced levels of activity, this may lead to increased skip filling and hence fewer packages being produced.
For special nuclear materials (SNM), the benefits are largely around safety case development. In the absence of hydrogen measurement, assumptions are often made leading to conservative engineering and operational constraints, these are costly and time-consuming and could now be avoided.
This development could be beneficial in supporting safety cases whenever assumptions are made in the absence of hydrogen measurements.
Current status - The development of the SNM short-range system took priority in 2019/20, with the long-range system development planned for 2020/21.
Confirmation of hydrogen levels at other locations within SNM are also planned.
Publications - Gamechangers
Delivery partners - Fraunhofer Centre for Applied Photonics
Contact details: Stephen Hepworth and Simon Malone technical.innovation@sellafieldsites.com
As the Senior Scientist within Sellafield Ltd Steve Hepworth is responsible for developing a more effective internal science community and to broker links between them and external research organisations such as UK universities and overseas institutions and funding bodies to assist with scientific knowledge development and peer review.
Steve first entered the nuclear industry with BNFL in 1986 as a craft apprentice and after gaining an HNC in Plant and Mechanical Engineering he left the business to pursue his academic studies at university.
Steve gained a BSc (Hons) in Applied Physics, an MSc in Medical Physics and then completed his PhD thesis entitled 3D polymer gel dosimetry for use in radiotherapy.
He joined Sellafield Ltd in 2002 as a radiometric physicist, managed the Decommissioning R&D Team and led a large leak mitigation study in support of MSSS before taking over the role of head of technical standards and assurance.
Following this appointment Steve returned to R&D in central technical and led the implementation of the IRT approach.
Steve is a Chartered Physicist, a Fellow of the Institute of Physics and is the Physics Scheme Leader for Sellafield Ltd graduates.
Steve said:
Sellafield’s strength is with its people, not simply their technical ability but their willingness to support each other through difficulties and conflicts.
Wall cleaning in legacy facilities
Project - Hydrogen detection using Raman spectroscopy
Benefits
The work carried out during 2019/20 demonstrated that hydrogen can be measured in situations where it is impossible to deploy standard hydrogen detectors:
In the Box Encapsulation, Plant and Product Store environment this technology will enable early detection of any changes in chemical reactivity from all packages.
If increased levels are detected this may lead to early interventions thus avoiding costly rework of packages. In the event of reduced levels of activity, this may lead to increased skip filling and hence fewer packages being produced.
For special nuclear materials (SNM) the benefits are largely around safety case development. In the absence of hydrogen measurement, assumptions are often made leading to conservative engineering and operational constraints, these are costly and time-consuming and could now be avoided.
This development could be beneficial in supporting safety cases whenever assumptions are made in the absence of hydrogen measurements.
Current status - The development of the SNM short-range system took priority in 2019/20, with the long-range system development planned for 2020/21. Confirmation of hydrogen levels at other locations within SNM are also planned.
Publications - Gamechanger
Delivery partners - Fraunhofer Centre for Applied Photonics
Contact details, Stephen Hepworth and Simon Malone technical.innovation@sellafieldsites.com
With over 25 years of experience in the IT industry, Chris Ballard is passionate about technology, specifically the adoption and innovation of novel ones.
His current role is focussed on robotics and artificial intelligence that will both remove people from extreme environments and assist the business with its mission to decommission and clean-up the site in a safer, more cost effective and timely manner.
In addition to this, Chris has a personal interest in how technology, such as digital media, can be used to enhance productivity and training to ensure that people have the best experience possible and the most suitable tools to address even the most complicated nuclear challenges.
Chris began his career as a software developer and later as a senior software engineer on the Sellafield site, he graduated from the University of Salford with a BSc (Hons) in Multimedia and Internet Technology and furthered his academic career through achieving his post graduate certificate in education (PGCE/PGCFE) and teaching in both schools, colleges and universities.
Chris is a Science, Technology, Engineering and Maths ambassador and a member of a number of professional organisations such as the British Computer Society (BCS).
Alternative treatment options for future waste challanges
Investigations into alternative treatment technologies is an ongoing R&D programme managed by central technical to deliver credible alternative options for the future treatment of higher activity wastes (HAW) arising from clean-up and remediation activities on the Sellafield site.
The 2 main strands of the programme include:
- thermal treatment
- alternative encapsulants such as geopolymers and novel inorganic cements
Thermal treatment
This project is ongoing and has been working to robustly underpin the benefits that thermal treatment can deliver, such as significant volume reduction, improved environmental performance, simplified storage requirements and lifecycle cost savings.
The preliminary output of this study recommended the formation of a tiger team to establish a way forward for the evolving strategy and which delivered its findings in January 2020.
The study concluded that 3 active demonstration facilities are required for:
- pumpable wastes such as sludges
- plutonium contaminated material (PCM)
- wastes arising from decommissioning activities such as mixed beta gamma waste
The learning from the operation of these facilities will be used to underpin the design of a future full-scale thermal treatment capability required to treat UK wide highly active waste.
In parallel with the strategy development, the project supports an ongoing experimental programme and in 2019/20, large scale thermal treatment trials were completed on PCM waste simulants using plasma technologies with successful results.
Alternative encapsulants
As part of the NDA strategy to expand the range of treatment options for highly active waste, Sellafield Ltd has been supporting research to increase cement encapsulation capability, recognising the changing nature of future feeds from decommissioning activities and security of supply issues.
In 2019/20 research activities focussed on the development of alternative encapsulation matrices for the improvement of performance, in particular alumina silicates, magnesium phosphates and calcium sulfoaluminate mixes as well as geopolymer based solutions, both bespoke and commercially available.
Trials undertaken so far have been small scale to assess the basic performance characteristics of each formula, to understand their limitations and to establish product quality envelopes.
This information has been used to select formulations that can be progressed to the next phase and plans for larger scale trials are in progress for 2020/21 to better understand scalability, repeatability and structural and physical properties.
Project - Waste treatment IRT
Benefits
Thermal treatment offers a range of benefits including significant volume reduction and alternative encapsulant materials can address security of supply issues.
Current status - The thermal treatment strategy is now an enhanced study and will conclude in December 2020, it aims to progress the technical and economic aspects of the demonstrators to the next stage.
The alternative encapsulant programme is also ongoing and will move towards larger scale demonstration and testing in the next financial year.
Delivery partners - National Nuclear Laboratory, TÜV SÜD- Nuclear Technologies Division, NSG Environmental Ltd., University of Sheffield
Contact details, Mark Dowson technical.innovation@sellafieldsites.com
Robotic glovebox operations
Glovebox use on the Sellafield site is typically by manual operations where personnel undertake tasks by inserting hands into long polyvinyl chloride (PVC) gloves built into panels without breaking containment.
This requires operators to manipulate plant and equipment and deploy tooling, however the predominant risk associated with this type of operation is exposure following penetration of the glove.
Sellafield Ltd has been researching ways in which tasks can be undertaken using remote technologies and a project is ongoing to investigate the development of an integrated system that could remove the need for operators to work in gloveboxes.
With end user engagement from the value streams, a prototype of a robotic remote handling system has been developed and demonstrated in a non-active environment representative of a potential scenario in which the technology may be used.
The technology can be remotely operated from a control room and has the ability to perform cutting, gripping and rotating movements all of which were demonstrated.
Further work is planned to progress the technology and address its current limitations through to demonstration in an active environment.
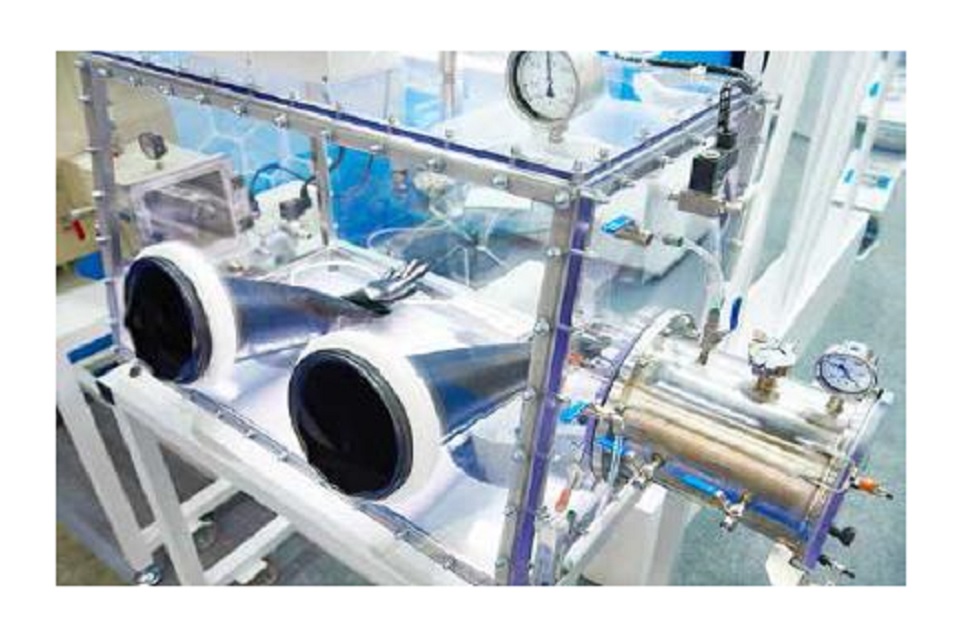
Project - Removal of hands from glovebox activities
Benefits
Removal of risks to operators associated with working with hazardous materials such as internal dose from a sharp object penetrating the skin through the glove or dose to the hands or fingers due to their proximity to radioactive materials.
Current status - Ongoing with the next phase endorsed for progression in 2020/21.
Delivery partners - National Nuclear Laboratory, Jacobs
Contact details, Kevin Burns technical.innovation@sellafieldsites.com
Effluents modelling
As Sellafield Ltd’s mission changes to focus more on environmental remediation, existing effluent treatment facilities will begin to operate outside of their original design envelope in order to support post operational clean-out (POCO) of process facilities.
These substantial changes in flowsheets will pose significant challenges and uncertainties for facilities which have been operated with well understood flowsheets since they were commissioned.
The Enhanced Actinide Removal Plant(EARP) provides a means of removing radioactive components from liquid waste streams.
The current treatment process, which is based around chemical precipitation and ultrafiltration, is relatively well understood in terms of its treatment of a well-defined waste stream.
During POCO and decommissioning activities, the feed streams to EARP will change from their current composition and it is essential that there is an understanding of how they will challenge the plant.
Sellafield Ltd has supported an ongoing research programme in recent years with the aim of understanding the underlying processes and considerable progress has been made.
To enhance this understanding and to aid decision making, data from the research programme have been incorporated into a qualitative model that is able to predict the likely abatement and performance which the plant will achieve in the future.
The development of this model is an ongoing project with NNL with the following progress achieved in 2019/20:
- completion of validation and verification of the model by NNL
- continuation of the programme of work to generate laboratory-based data to support the model
- creation of an updated ultrafilter model using output from a recently completed CINDe PhD to enhance the predictive capabilities of the model
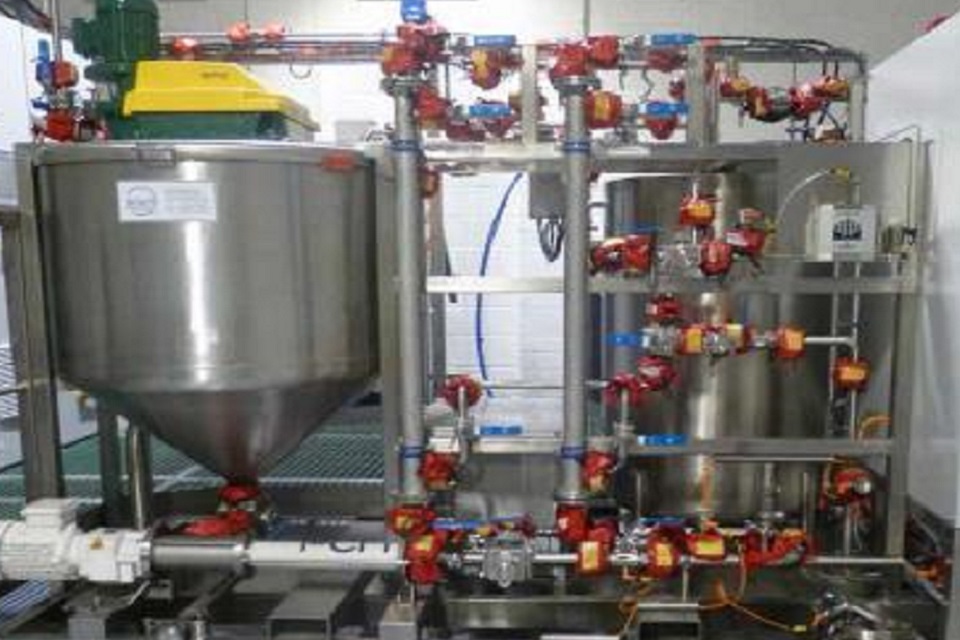
The EARP rig in NNL’s Central Laboratory
Project - The EARP model
Benefits
The model will be used to:
- provide underpinning of the impact of Thorp and Magnox POCO operations on EARP operations, abatement and performance
- generate data to support the ongoing review of Sellafield Ltd’s Environmental Permit for Radioactive Substances Activities (RSA)
- support the optimisation of disposal of plutonium containing waste bottles from Analytical Services to EARP
- produce improved understanding of the EARP process such as residence times within the facility
Current status - Ongoing with further work planned for 2020/21.
Delivery partners - National Nuclear Laboratory, The University of Manchester
Contact details, Felipe Basaglia technical.innovation@sellafieldsites.com
Felipe Basaglia, Technical Manager
Felipe graduated from The University of Manchester with an MEng in Chemical Engineering and an MSc in Nuclear Science and Technology with the Dalton Institute before joining Sellafield Ltd in 2012 and is passionate about the nuclear industry.
An active participant in the Nuclear Institute and Institution of Chemical Engineers (IChemE), Felipe supports young learners in their STEM activities in the North West, giving technical talks at international conferences and delivering training to regulatory bodies.
He is a member of the One Million Mentors Scheme which provides young people with mentoring and support as they transition into adulthood.
For his achievements and advances in process modelling, Felipe was nominated for two IChemE Global Awards in 2019 and received the ‘Highly Commended Award’ in the water category.
Felipe manages the team of engineers responsible for the assessment of the long-term performance and operability of the Site Ion Exchange Effluent Treatment Plant (SIXEP) and its donor plants, the R&D effluents portfolio and routinely engages with regulatory bodies delivering key documentation.
He is the Flowsheet CoE and leads a working party that successfully designed, developed and implemented a structured governance and audit programme for flowsheet development and management, now used across all teams within Sellafield Ltd.
Further a field Felipe has been selected to undertake a World Association of Nuclear Operators (WANO) engineering review of the Embalse Nuclear Power Plant, Argentina, a very exciting opportunity.
Felipe said:
Working for Sellafield as a chemical engineer has been both incredibly rewarding and interesting; the site offers a real challenge and no two problems are ever the same.
In my current role, I support both of the site’s effluent abatement facilities (SIXEP and EARP), ensuring data driven decision making is used to underpin site strategic and tactical decisions so that we can successfully deliver the Sellafield mission.
Dawn Watson, Head of Strategy and Technical Analytical Services
Playing a central role in supporting Sellafield site activities the analytical services programme runs the laboratories on the site and analyses a wide range of samples, in the region of 10,000 per year
Dawn’s current role is to manage the team responsible for studies and decisions associated with the analytical programme and more widely is responsible for the technical capability of the entire department and works hard to ensure people feel valued and the work that they do is recognised.
Dawn graduated from UMIST with a physics degree and began her nuclear career with NNC (now Jacobs), based in Knutsford.
She spent a number of years delivering safety case work and project management whilst studying for an MBA in Engineering Management before moving to Cumbria in 2004 and joining Sellafield Ltd in 2005.
The majority of Dawn’s roles with Sellafield Ltd have been project management and with her strong technical background this has provided her with a good understanding of project business cases and the skills to spot alternative approaches to major capital spend.
Dawn is an active member of Women in Nuclear (WiN) and looks after the mentoring programme which provides guidance and support to women in the industry. Dawn has a been a Fellow of the Institute of Physics since 2017, sits on the Diversity and Inclusion Committee and is Treasurer for the Institute’s Women in Physics Group.
She is proud of her roles and has a keen interest in the development of people and works with others to promote diversity within the scientific community.
Dawn said:
I really enjoy the challenge that my job brings – every day is different. Working at Sellafield means you meet lots of different types of people and there is always something to learn from them.
Working as part of a team and encouraging and mentoring people to better themselves and accept new challenges is one of the most rewarding things to do, and I’m lucky that in my role I can do that.
Horizon scanning
There is a wide and diverse range of challenges associated with decommissioning, clean-up and remediation activities on the Sellafield site.
As an organisation Sellafield Ltd needs to develop the capability to find the best solutions to solve these challenges and is continuously seeking tools and techniques to improve the visibility of available technologies.
Additionally, an awareness of technology changes and trends in the wider external environment is also important because these can have a significant impact on future operations by, for example, improving efficiency, attracting new skills, reducing the impact on the environment or by providing cost savings.
In 2019/20, a number of initiatives were progressed as the company moves towards improving the horizon scanning capability within the business:
Horizon Scanning Group
This was established with representatives from across multiple areas of the Sellafield Ltd business and is responsible for staying abreast of changes and trends in the external environment which could provide opportunities or risks to the enterprise.
Strategic foresight training
Completion of a training course at Cranfield University provided the Emerging Technology Team with the opportunity to use horizon scanning to create and explore various scenarios and to determine whether the business needs to adjust its strategies or decisions to either capitalise on an opportunity or to mitigate risk.
Following this training a draft methodology was developed to systematically analyse information and challenge assumptions about the future, so that strategies can be prepared accordingly. This is expected to be trialled in FY 2020/21.
Work also continued on other tools such as the IdeaCatalog technology database (developed by Cogentus Consutling Ltd.) to help provide visibility of technologies and insight on longer term trends beyond the Sellafield site.
The pace of change in technology is increasing and with it brings an increasing level of uncertainty. With systematic horizon scanning methods and tools in place to explore and assess this uncertainty, Sellafield Ltd can move forward with confidence that the future holds many opportunities.
To find out more contact, Andres Alfaro horizon.scanning@sellafieldsites.com.
Andres Alfardo, Emerging Technology Team
With a BA (Hons) in Marketing Management from Manchester Metropolitan University, Andres began his career with Carat Manchester before joining Sellafield Ltd on the graduate programme.
Andres is part of the team responsible for improving the business’s horizon scanning capability for new technologies. The team creates methods that can be used to analyse external technology trends and explores the opportunities and risks they could present to the business in the future.
Andres also searches for tools and techniques that can help scan the growing range of technologies that could be used, increasing confidence that the right solutions can be found to meet the needs of the business.
Continuing professional development is important to Andres, he has gained the APM Project Management Qualification, as well as APMG Change Management Foundation Certification.
He also recently completed training in strategic foresight at Cranfield University, which has provided him with the skills needed to identify, analyse and communicate insights about the future.
Andres said:
We live in uncertain times, and our relationships with technology are changing. To deliver the remainder of its mission successfully, Sellafield – like every other business today - will need to embrace this uncertainty and continuously challenge its own assumptions.
My role allows me to explore how to do this; I enjoy helping the business prepare for the future, which is a major part of its responsibility.
Dragons’ Den style competition
An initiative has been adopted by Sellafield Ltd to encourage the creative thinking of Sellafield Ltd staff.
A Dragons’ Den style competition is an event for employees to submit their ideas against themed challenges.
These ideas are then taken forward for judging by business leaders and the winners given time and funding to develop and implement their ideas.
Building on the success of its first event in 2018, Sellafield Ltd invited all employees to come up with ideas for improving communication and efficiency with the winners announced in June 2019.
Another initiative that impressed the Dragons was SellaCycles proposed by Joshua Shepherd, Viv Winter and Tom Durcan.
The innovative idea is a bicycle bank that could be used by staff to move around the site, a simple but effective idea that is also good for the environment and is being taken forward.
To find out more contact, Claire Cleaver-Jones technical.innovation@sellafieldsites.com
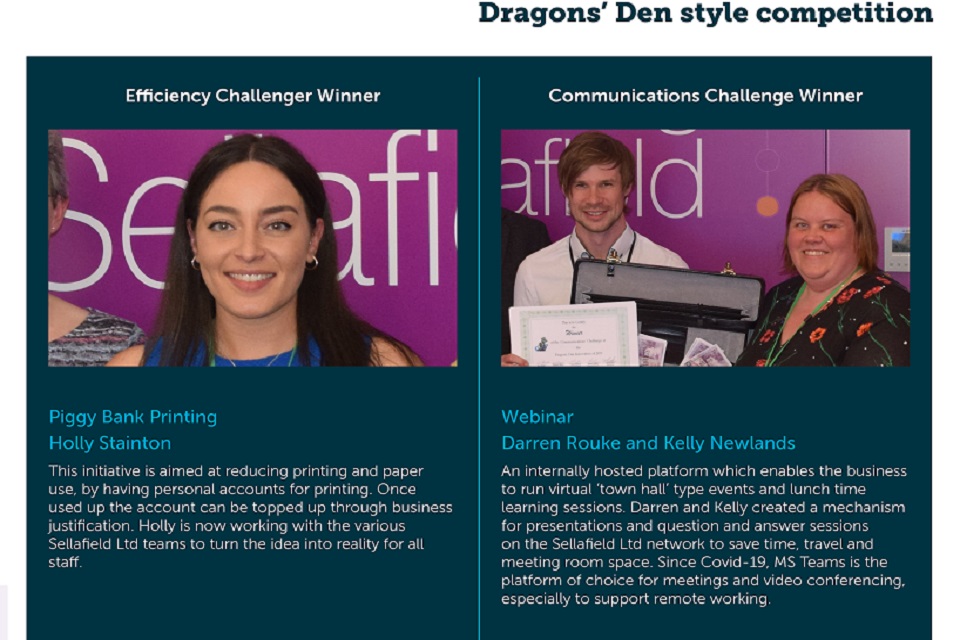
Game Changers
Now in its 5th year, Game Changers continues to attract and progress innovative projects to solve decommissioning challenges at Sellafield.
In 2019/20 5 calls for innovation resulted in >100 funding applications for feasibility studies, focussing on:
- asset management, in collaboration with EDF Energy
- the use of robotics and artificial intelligence
- machine learning
Proof-of-concept is the follow-on stage from a feasibility study where projects have demonstrated the technology or produced a prototype.
Ongoing projects awarded this funding in 2019/20 included:
- extending the life of battery powered sensors with Sensor Driven Ltd.
- exploring the use of high power ultrasonics to remove blockages and clean pipelines with Brunel University London and NNL
- developing a modular access toolkit for POCO tasks in difficult to reach areas with Eadon Consulting
- the development of a mobile remote inspection platform for waste containers with Creid 7
- sharp object recognition using 3D with i3D Robotics
- the use of hydrophobic sponges to concentrate and recover contaminated organic material with NNL
- real time gamma optical imaging with Loughborough University
- image enhancement for improved visual inspection of nuclear waste stores with the University of Strathclyde
A new partnership was established with the Knowledge Transfer Network (KTN) to promote Sellafield Ltd challenges using their innovation exchange, an online platform that promotes innovation transfer and a call for innovative ways to address the challenges of POCO was opened for proposals.
This call attracted 14 applications, 5 of which were awarded funding for feasibility studies.
Ongoing success stories that have progressed well and have continued to be supported by Game Changers to fully develop their technology include:
- Rawwater Engineering Company Ltd.’s crack repair system
- Cryoroc Ltd.’s freeze casting for waste immobilisation has been awarded funding for a full-scale trial in conjunction with NNL
- detecting hydrogen at range with the Fraunhofer Centre for Applied Photonics
And finally, Capsa Solutions Ltd. is a new innovative waste management organisation, which was incorporated as a direct result of engagement with Sellafield through the Game Changers process.
To find out more, contact Andrew Cooney or visit Game Changers
Delivery partners were National Nuclear Laboratory, FIS360 Ltd.
Frank Allison, CEO, FFIS360 Ltd.
Based in Penrith, Dr Frank Allison, is the founder and CEO of FIS360 Ltd. managing a specialist team of consultants with significant experience in supporting early stage technologies from concept through to commercial products and for the development and delivery of large scale innovation programmes including Sellafield Ltd’s innovation programme Game Changers.
Whilst delivering Game Changers, Frank has worked with many Sellafield Ltd staff employed in multiple roles across the company and has gained a good understanding of the range and magnitude of the decommissioning challenges.
Building on this experience Frank is now developing partnerships with other Site Licence Companies (SLCs), sharing the learning gained through working with Sellafield Ltd and identifying common challenges across different sites.
The Game Changers team has managed many exciting projects over the years and a few of Frank’s highlights include:
The active deployment of innovative hydrogen detection technology
Developed by the Fraunhofer Centre for Applied Photonics, the Game Changers programme has supported this project for 18 months from an initial idea through to a deployable system.
The technology has enormous potential for the nuclear industry and other sectors where gases need to be detected remotely without placing operators or instruments in sensitive or hazardous areas.
This is the first Game Changers project to complete a successful active trial at Sellafield. Supporting Rawwater to transfer their proven molten metal manipulation technology (M3) repair system from the oil and gas sector into nuclear.
M3 is a novel alloy system which can be used to seal large openings or fill micron sized cracks or pores in civil structures or metallic components such as pipework.
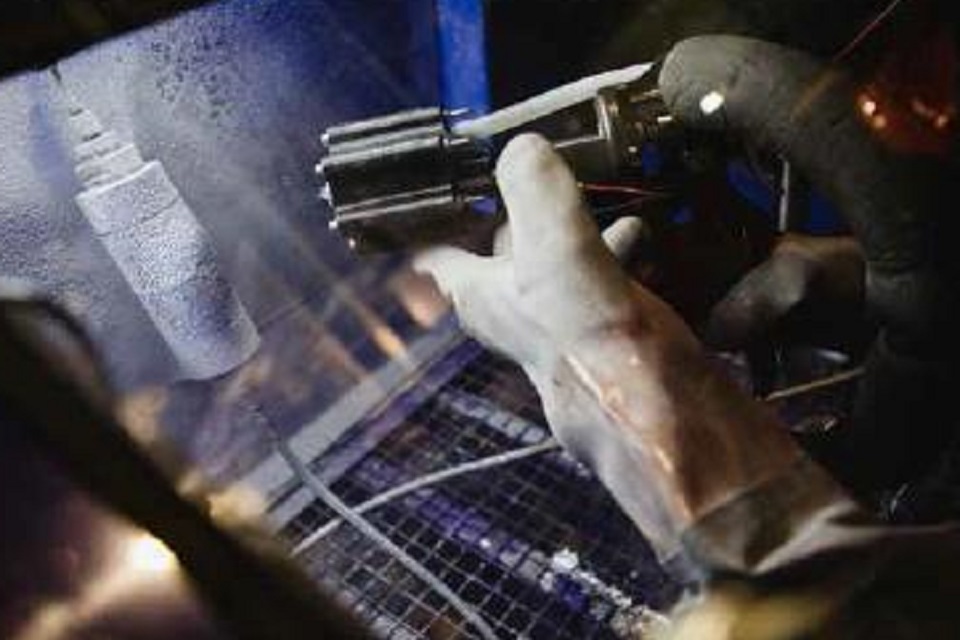
Rawwater’s crack repair system
The support provided by Game Changers has led to Rawwater securing a contract with the Japanese energy operator Tokyo Electric Power Company (TEPCO), in collaboration with NNL. Rawwater technology has also secured significant follow-on funding from Innovate UK and the Ministry of Defence.
Frank said:
I have a real passion and enthusiasm to make a difference and feel incredibly lucky to work with so many motivated people at Sellafield, across the nuclear industry and indeed across multiple supply chains.
I’m excited for the future and I’m looking forward to seeing increased partnership working across the nuclear industry to overcome shared challenges.
Spent Fuel Management
The Spent Fuel Management (SFM) value stream is responsible for the receipt, reprocessing and storage of spent nuclear fuel with the R&D programme focussing on ensuring:
- long-term capacity and capability for the storage of spent fuel
- the management of highly active wastes until the hazard has been removed
- effluent and encapsulation facilities have the capacity and capability to support current operations to completion, high hazard risk reduction, POCO and decommissioning operations
- long-term management of encapsulated and vitrified products and their storage
In-situ monitoring in the Fuel Handling Plant
The Fuel Handling Plant (FHP) is an operational facility on the Sellafield site storing Magnox fuel prior to reprocessing as part of the Magnox Operating Programme (MOP), it also stores fuel from the EDF reactors.
To support the hazard reduction programme, a decision was made to retrieve legacy fuel from the First Generation Magnox Storage Pond (FGMSP) and consolidate it in FHP, however it is important to understand the impact of this transfer on the ongoing operations in FHP.
Because of the challenging complexities of taking liquor samples for analysis from within a Magnox container, Sellafield Ltd has supported the development of an in-situ technique using a gamma detector deployed ~4m underwater to measure the Cs-137 activity.
Following a programme of design and manufacture of the container monitoring system, the technology has been in use for most of 2019/20 to collect data that are used to calculate the rate of corrosion of the fuel in the skips and to monitor the rate of activity build up within the container.
This information provides confidence that future activity releases via the effluent route are within their predicted levels so that the impact on downstream treatment facilities can be managed effectively.
The innovative solution is simple but effective; it consists of a sampling pipe extending from one of the containers to a shielded box system, installed underwater within the pond, this shielded box also houses the gamma detector which sends data to a display unit outside the pond area for review by an operator.
This method provides a controlled measurement system that does not require physical sampling, the operator simply turns on the machine for a few minutes per week from a remote location away from the hazardous environment.
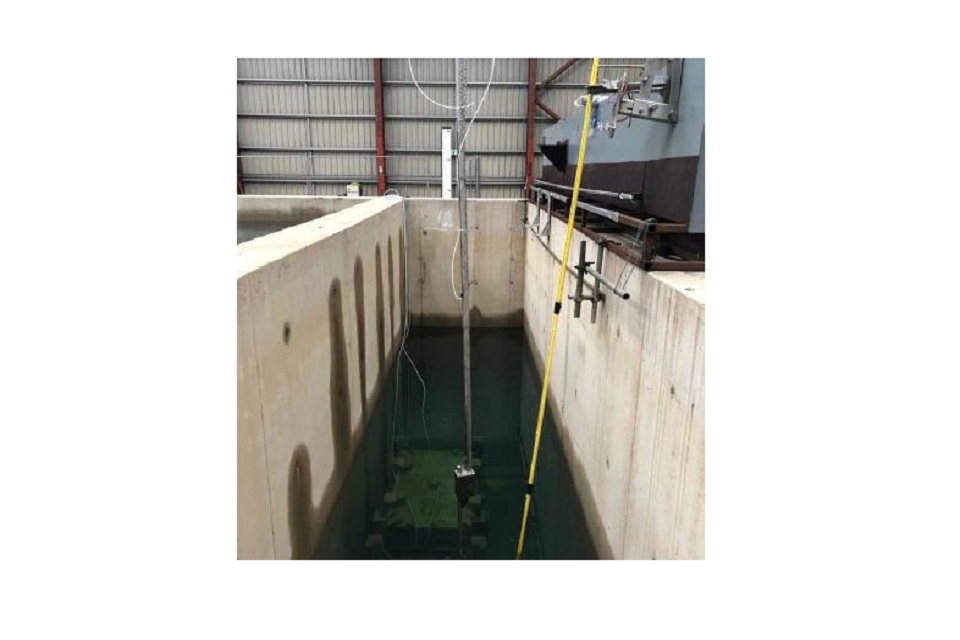
Container monitoring equipment during testing. The gamma detector is housed in the shielded box just below the water line.
Project - In-situ container monitoring in FHP
Benefits
Understanding the activity levels within storage containers supports the strategy for the ongoing safe storage of legacy fuel in FHP and its impact on other operational activities.
The final design of the system also has the potential to be used to monitor the container water activity increase caused by other fuels should they be stored in FHP.
Current status - The project is complete, and the technology is in operational use at Sellafield.
Delivery partners - Cumbria Nuclear Solutions Ltd (CNSL) delivered via the Decommissioning Delivery Partnership (DDP)
Contact details - John Rowley technical.innovation@sellafieldsites.com
John Rowley, SFM Ponds Technical
John joined Sellafield Ltd as a physics graduate directly from university in 2007 and is currently involved in supporting the forward strategy for reprocessing Magnox fuel.
He also manages the forward R&D programme for FHP which recently included a project to develop an underwater container monitoring system to enable the activity of water to be monitored without the need for physical sampling.
John maintains a keen interest in the nuclear research undertaken in universities, such as the TRANSCEND programme and regularly supervises PhD students. Recent examples include research on Advanced Gas-cooled Reactor (AGR) fuel storage and behaviour.
Further afield, John represents Sellafield Ltd on the International Atomic Energy Agency’s (IAEA) spent fuel research programme.
John said:
Sellafield is very specialised, one day you could be working on very technical challenges and interacting with technical experts and PhD students and the next you could be planning the size and function of a facility that will be delivered 10 years in the future.
Dan Pocock, Technial Support
Before graduating from Newcastle University, Dan completed a 12-month industrial placement with Analytical Services at Sellafield.
He then joined SFM technical on the graduate programme, after gaining a MEng in Chemical Engineering.
Dan’s role in providing technical support to Magnox Reprocessing includes conducting technical investigations into emerging plant issues, preparation for POCO following the completion of reprocessing and support to plant operations.
Dan is also the secretary of the Magnox Reprocessing Technical Committee.
As an active member of IChemE Cumbria Members Group, Dan manages the group’s communications and social media, liaises with IChemE to organise events and manages the website.
Dan said:
I enjoy the variety of work, we often do things that none in the world has ever done before, like finding new and innovative ways to deal with orphan nuclear wastes.
I find it rewarding that my work is meaningful and adds real value to society - helping clear up the UK’s nuclear legacy has enabled us to be a key global player in the world today.
High level waste plants technical programme
Highly active wastes generated from reprocessing activities from both Thorp and Magnox operations have been vitrified in the High-Level Waste Plants (HLWP) for many years, prior to storage on the Sellafield site in the Vitrified Product Store (VPS).
With the site mission moving towards POCO and decommissioning, the technical programme aims to provide the essential underpinning for future feeds such as POCO wastes from Highly Active Liquor Evaporation and Storage (HALES), asset management of all facilities and support for ongoing operations.
POCO feeds vary significantly in their composition and it is important to ensure that they can be processed through the plant safely and without significant interruption to the hazard and risk reduction mission.
During 2019/20 the team made significant progress on 2 key elements of the technical programme:
Glass formulations
With support from NNL’s research and fullscale vitrification test rig, a key milestone in the move towards the routine processing of POCO feeds to HLWP was reached.
A new formulation of glass, calcium/zinc glass, was tested on vitrification line one in a trial spanning from October 2019 to January 2020.
The trial was successful and supported agreement for continued use of the new glass in line one operations and the transition of lines 2 and 3 to the new formulation once processing of POCO feeds begins.
Vitrified Product Store
Also supported by NNL, camera inspections of VPS were completed in 2019/20 to monitor corrosion, a key step in its care and maintenance.
The inspections used a ‘bullet camera’ developed by NNL passed through a previously unused existing port, enabling different areas of the store to be observed.
The project was completed earlier than originally planned and avoided the costly refurbishment of the shielded camera flask that was no longer fit-for purpose.
Understanding the condition of the store is crucial to assess how long the containers can safely remain in storage and whether there is a requirement to build a second product store.
Project - HLWP technical programme
Benefits
Implementing a new glass was an important step because this formulation is able to achieve increased quantities of molybdenum per vitrified container resulting in fewer containers and therefore a reduced impact on storage and disposal arrangements.
The camera inspection of VPS allows the condition of the store to be assessed providing information for decision making on the interim storage requirements for highly active wastes prior to final disposal.
Current status - The HLWP technical programme is ongoing providing further underpinning as the site moves towards POCO and decommissioning. It will be used to support future decisions such as the requirement for a second product store expected in 2020/21.
Delivery partners - National Nuclear Laboratory, Cera Dynamics Ltd.
Contact details - Fiona Wright technical.innovation@sellafieldsites.com
SIXEP strategy
One of the Sellafield site’s effluent treatment plants, SIXEP, has been operational for 35 years and has been integral in reducing discharges from the Sellafield site during reprocessing operations.
SIXEP has supported a number of fuel storage facilities and more recently the high hazard and risk reduction programme in legacy facilities.
Current plans require SIXEP well into the future and this poses major challenges for the plant. It is the role of strategy and technical in SFM to advise on the most appropriate strategy for the continuation of the SIXEP capability and to manage the R&D programme that will underpin it.
Working with key stakeholders, a significant piece of work was undertaken in 2019/20, to review the operating plans for SIXEP and to develop a strategy for its continuing operations.
The technical challenges for the plant were reviewed against outputs from the ongoing R&D programme, in particular:
- chemical modelling to assess the impact of current and future feed streams on abatement performance.
- research on interactions between alpha species and uranium colloids to improve understanding of their behaviour in the SIXEP process and reduce uncertainty in the flowsheet.
- potential technologies and deployment techniques to improve the quality and coverage of the inspection regime to inform assessment into the risk of failure of key vessels and pipework.
An updated strategy and delivery plan are now in place for SIXEP with support from key stakeholders, it has been underpinned by the R&D programme, with future R&D requirements and priorities identified.
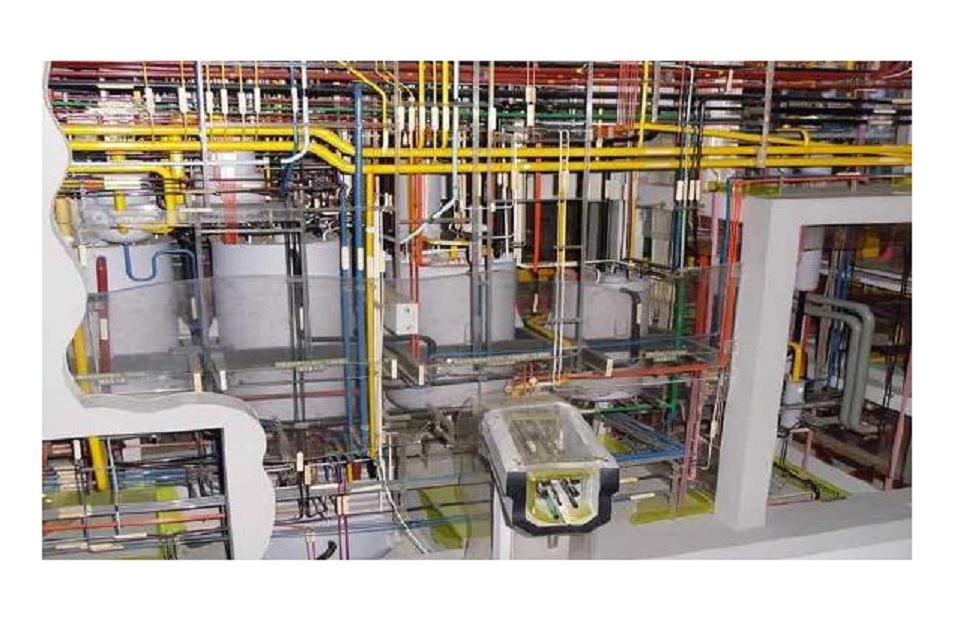
SIXEP Sea Discharge Treatment Cell which is the focus of development work to improve inspection quality and coverage
To find out more contact, Tom McMillan technical.innovation@sellafieldsites.com
Andrew Riley, Effluents Strategy Lead
Andrew has been in the nuclear industry for more than 30 years and has gained extensive experience from working in various science and engineering roles over the years.
Originally joining BNFL’s R&D department in the mid-1980s with a BSc (Hons) in Chemical Engineering, Andrew focussed on lab and rig scale research to support the new generation of effluent treatment plants and processes to support Thorp which began operations in 1994.
As the Sellafield site enters a new phase of decommissioning and clean-up following the end of reprocessing, Andrew is once again at the heart of the effluent strategy for the Sellafield site and responsible for its development.
His role includes chairing the committee responsible for the coordination of all effluents work across the site and the definition and sponsoring of studies to support decision making as the strategy develops.
Andrew also manages the technical team that supports current operations, carries out process engineering development and scientific studies and leads investigations to identify and solve problems.
Andrew is a Fellow of IChemE, a Chartered Engineer and a member of the Institute of Leadership and Management.
Throughout his career he has been interested in the professional development of graduates and degree apprentices and regularly acts as a mentor.
Toni Warwick, Senior Technical Advisor
Toni graduated with a MSci in Forensic and Analytical Chemistry from the University of Strathclyde before she joined Sellafield Ltd on the graduate programme in 2011.
The graduate programme offers structured placements across a variety of disciplines and Toni was able to complete part of her training with NNL, she delivered a project on the impact of organic materials present in effluent prior to encapsulation and investigated novel technologies for retrieving stored sludge material.
As part of a technical team, the work Toni carries out is quite varied, ranging from working with plant operators on emerging issues to the assessment of the impact of current and future donor feeds on the SIXEP process and the management of longer term R&D with NNL.
This means that Toni can often be found at different locations to the Sellafield site or in one of the NNL facilities.
Keen to pass on her experiences, Toni plays an active role in the professional development of others. She is a mentor for technical specialist trainees, degree apprentices and for chemists progressing through the Royal Society of Chemistry (RSC) accredited scheme.
In her role as STEM ambassador her interests extend to facilitating STEM activities in local schools and she has represented Sellafield Ltd at both local and national Big Bang events.
Toni said:
Working for SIXEP, you rarely have two days the same. Collaborating with colleagues across the effluent stream and NNL, I have the opportunity to tackle a different challenge every day.
I enjoy the variety and I’m proud that my work contributes to ensuring SIXEP can support MOP and high hazard risk reduction activities whilst minimising environmental impact.
Ian Armstrong, Magnox Reprocessing Technical Manager
After studying metallurgy and materials science and then gaining a PGCE, Ian spent 20 years in education before joining Sellafield Ltd in 2013.
Ian’s current role is to manage the team which supports Magnox reprocessing by undertaking investigations, supporting plant restarts and preparations for POCO.
He also supports both the Materials and Actinide Chemistry CoEs. Ian is a member of the Institute of Materials Minerals and Mining (IOM3) and has continued his professional development by undertaking courses in portfolio management and in metallurgy and corrosion with the University of Surrey.
Ian said:
my role provides a variety of challenges, managing and developing a team of young professionals, on plant support, desk based technical support and financial/business management. My work can range from desk work to training or a night shift on plant.
Special Nuclear Material
The Special Nuclear Material value stream is responsible for the safe, secure and appropriate storage of special nuclear materials with the R&D programme focussing on:
-
understanding the chemical and physical behaviour of plutonium bearing materials to ensure longterm safe management and storage, focussing on aspects such as radiolysis, evolution of sealed packages, corrosion, behaviour of impurities such as chlorides and the requirements for future conditioning
-
innovative approaches to the safe operation of facilities handling and storing plutonium, these could include technologies such as robotics, automation and digital applications for alpha environments
- continued technical underpinning of POCO and decommissioning plans for alpha facilities
- techniques for the monitoring, retrieval and processing of residual product in gloveboxes, plant, equipment and facilities during POCO and decommissioning
- direct support to the special nuclear materials consolidation programme
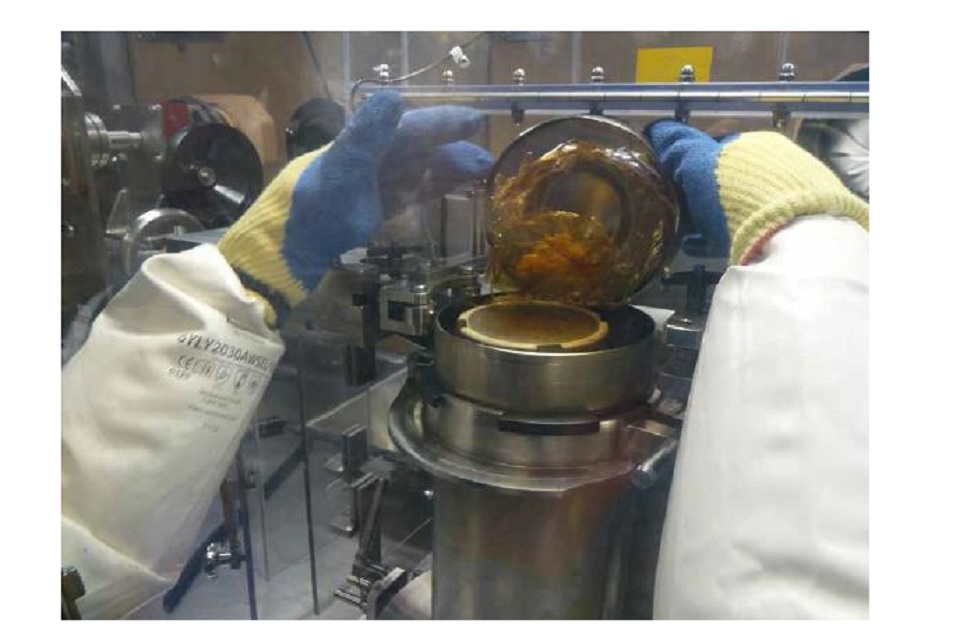
Outer can cut open to reveal the inner can and degraded polythene (Courtesy of the National Nuclear Laboratory)
The SNM R&D programme
The Special Nuclear Material value stream is responsible for the safe, secure storage of special nuclear materials.
With a key focus on the increased safety of people by identifying technology that removes the operator away from the hazardous part of the task, this section describes the progress the SNM value stream has made during 2019/20 in the following areas:
- long-term safe management and storage of nuclear materials
- glovebox operations
Long-term safe management and storage of nuclear materials
A key objective of the SNM R&D programme is the long-term integrity and safe storage of packages containing special nuclear material and an important element of this is an understanding of how they will evolve over time, this includes radiolysis, corrosion and the behaviour of impurities such as chlorides.
Innovative solutions supported by the value stream are not only addressing can design and their performance over long timescales but developing technologies to enable the packages to monitor themselves and techniques to monitor for surface defects and changes to the store environment.
Smart cans
The current cans in use at Sellafield have a design life of about 25 years and a process of repacking material into modern, 100-year cans, ready for long-term storage begins with the commissioning of the Sellafield Product and Residue Store Treatment Plant (SRP).
The new cans will be placed in a modern facility, the Sellafield Product and Residues Store (SPRS) where inspection and monitoring will be required to ensure long-term integrity is maintained.
The development of technology to enable “smart” packages to monitor themselves and to communicate warnings if they are not performing as expected, has been developed by Nuclear AMRC and The University of Manchester.
This approach also aims to use the heat generated by the cans to power the smart sensors negating the need for additional power sources.
Some initial tests on the equipment have provided positive results and additional work in FY 20/21 is planned, focussing on the miniaturisation of the components for use with modern cans.
Package defect detection
Like all materials that could be stored for many decades it is important to demonstrate that the performance of the packages is as expected. Current technology used to inspect packages in stores at Sellafield is via CCTV which can provide limited information and therefore an alternative more modern approach is being sought via the Game Changer programme.
A potential solution that will be progressed in FY 2020/21 to identify corrosion and other surface defects is hyperspectral imaging.
Long range hydrogen detection
Over a period of time there is potential for some legacy packages to release low levels of H2, however this is considered to be unlikely.
During 2019/20 occluded air regions within one of the legacy stores were sampled via long range hydrogen detection using Raman spectroscopy developed by the Fraunhofer Centre for Applied Photonics.
This innovative approach to the remote detection of hydrogen has been developed with funding obtained via the Game Changer programme.
Planned work in FY 2020/21 will investigate the potential for modular storage facilities and automated stores to increase safety and improve efficiency.
Glovebox operations
Gloveboxes have been used on the Sellafield site for many years for a variety of purposes such as R&D, analysis and more general operational activities.
To support the continued safe operation of gloveboxes there are a number of initiatives being progressed to improve efficiency and protect the operator:
- an innovative technique has been developed to simplify the cleaning of window panels in gloveboxes at a significantly reduced cost. The new process developed by ORANO, works by using polishing technology and is expected to be in use on the Sellafield site in FY 2020/21
- the Virtual Engineering Centre, University of Liverpool has developed a technology that enables an operator to receive voice activated instructions through an earpiece, whilst undertaking operations in a glovebox. The feasibility of this technology has been demonstrated and it is expected to be progressed through FY 2020/21.
- the UK Alpha Resilience and Capability (ARC) programme is a collaborative initiative which aims to sustain and enhance alpha capabilities across the UK nuclear industry.
In line with this, the SNM R&D programme is supporting the development of a virtual reality glovebox training facility with Tannahill Reay Visual Communications Ltd.
Traditionally PVC has been used to bagout SNM containers from gloveboxes, PVC has the disadvantage that it breaks down in the presence of heat and radiation releasing chloride which can challenge package containment as a result of corrosion.
An initiative to secure a modern technique to seal the plastic casing as an alternative to that traditionally used on the Sellafield site, identified a sealing process designed by a French manufacturer - The ORA Company.
This technology, now ready for installation at Sellafield, also allows for the use of polyurethane (PUR) instead of PVC which can degrade and generate corrosive hydrochloric acid.
Manual glovebox activities require operators to manipulate plant, equipment and tools with regular close proximity to nuclear materials. The predominant risk to operators when carrying out these tasks is potential exposure to hazardous materials as a result of penetration of the glove.
To address these challenges a robotic approach has been developed to replace manual working in gloveboxes
As previously described, gloveboxes on the Sellafield site will continue to be used to support a range of operational activities but there are more than 500 that require POCO and decommissioning over the next few years.
The SNM programme has been exploring initiatives for the retrieval of residual nuclear material using technology adapted from a handheld vacuum cleaner to recover plutonium oxide powder from gloveboxes, particularly from areas that are difficult to access.
This successful project was described in the 2018/19 report and is ongoing with further testing on radiation effects on the equipment.
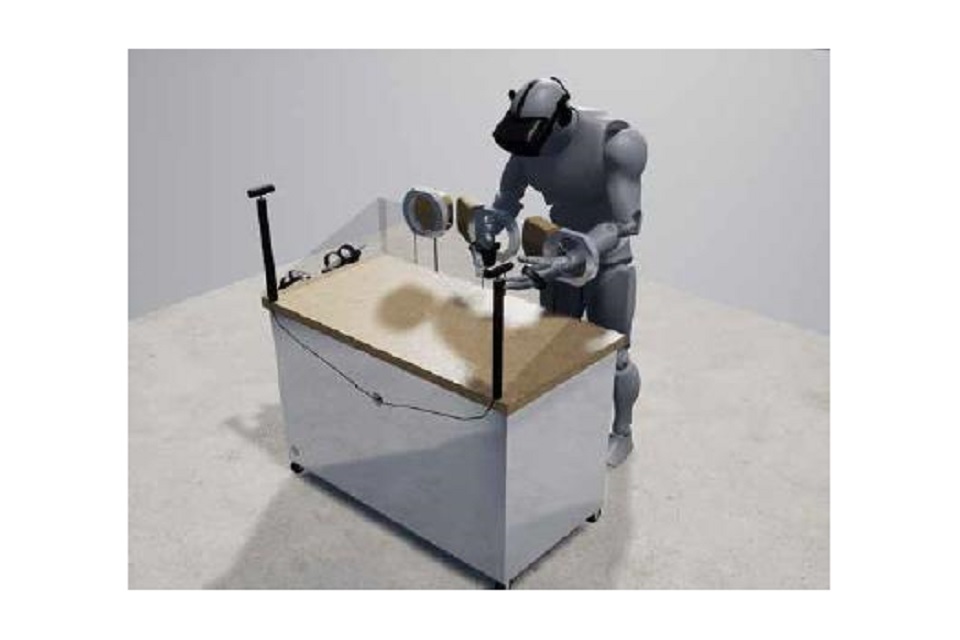
Virtual reality training capability for glovebox operations
The image below shows the can puncture and gas sampling rig with an unpunctured outer can in the foreground. In support of the underpinning science to understand how packages will evolve over time, this equipment is used for puncturing SNM packages so that gases in the head space of the outer can may be analysed (Courtesy of the National Nuclear Laboratory).
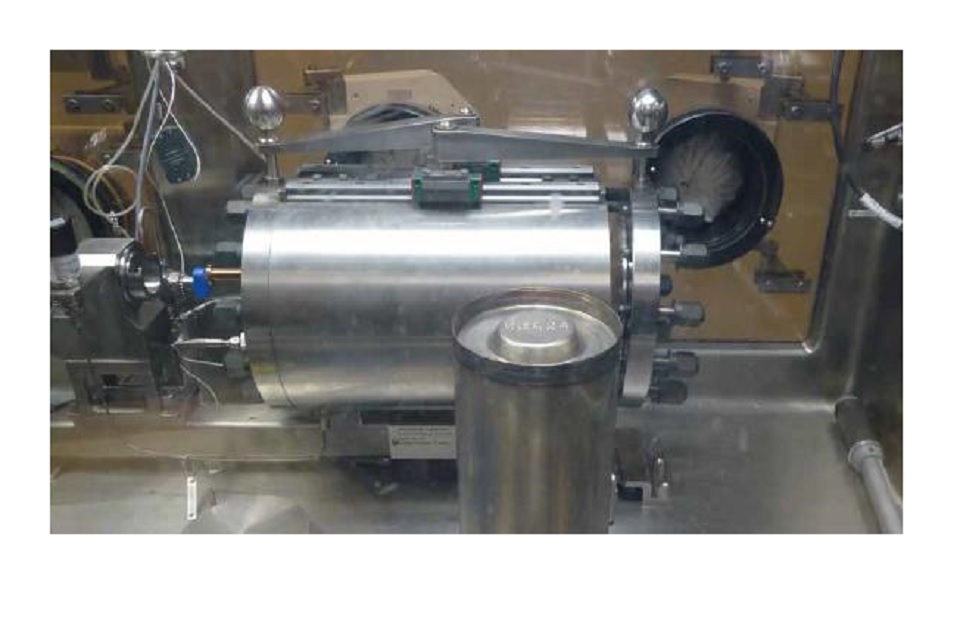
Project - SNM R&D programme
Benefits
The programme aims to provide the SNM value stream with new technologies and processes to enhance current and future operations to improve safety, accuracy and efficiency.
Current status - Ongoing programme
Delivery partners - The ORA Company, The University of Manchester, Fraunhofer Centre for Applied Photonics, University of Liverpool, Tannahill Reay Visual Communications Ltd., National Nuclear Laboratory, ORANO, Nuclear Advanced Manufacturing Research Centre
Contact details - Paul Mort technical.innovation@sellafieldsites.com
Robert Bernard, Senior Technology Manager
Rob studied at the University of Strathclyde and gained a BSc (Hons) in Applied Chemistry followed by a PhD in Polymer Chemistry before joining the nuclear industry.
Originally with BNFL’s Research and Technology (R&T) function, Rob researched batchwise dissolution chemistry of natural uranium, silver (II) electrochemical dissolution processes and electroreduction of zirconia in molten salts before moving into Thorp to support finishing line operations for a significant part of its operational life.
Rob has been based on the Sellafield site for almost 20 years and is now focussed on leading R&D projects with universities and research organisations to improve can and store inspections in the SNM value stream.
Interested in professional development, he is involved in the progression of chemists to Chartered Chemist status, through the RSC accredited scheme.
Robert said:
In my near 20 years career on site, I can safely say no 2 days have been the same. It is pleasing to see some of my ideas “get on to plant.” I particularly enjoy bringing academics and research institutes together to resolve SNM technical challenges.
Ewan Williams, Degree Apprentice
Ewan joined SNM as a degree apprentice with his first role in the team responsible for identifying new techniques and technologies across the value stream.
Some of the projects in which Ewan has been involved include:
- Image recognition software for identifying SNM package contents (presented in the 2018/19 Annual Research and Development Review)
- glovebox window cleaning, using tools to improve the visibility inside gloveboxes
- the ORA Welder work, a thermal welder designed to weld PVC/PUR bags for glovebox bagging out operations
Ewan said:
Working in this team was challenging yet very rewarding because a lot of the work carried out has not been attempted before in SNM but when delivered, can make a positive visual impact.
Currently on secondment, Ewan is now part of the inspection team that provides technical support to the continuing safe and secure storage of materials and hopes to gain some practical experience from remote inspections of SNM packages.
In parallel with his everyday duties, Ewan is part of a team of trainees working with the ARC programme, on a project to create an online knowledge management hub for SNM and is working towards membership of the Nuclear Institute.
Ewan said:
The apprenticeship programmes offered by Sellafield Ltd are a fantastic opportunity to develop key skills whilst gaining valuable experience in an engineering environment.
Retrievals
The Retrievals value stream is responsible for the retrieval of nuclear waste, fuel and sludge, stored in legacy ponds and silos with the R&D programme focussing on:
- ensuring existing facilities and ongoing operations are not adversely affected by the introduction of planned retrievals activities
- developing condition monitoring and inspection capabilities to demonstrate that retrieved waste behaviour is consistent with predicted behaviour during the storage period
- continued development of innovative techniques for waste retrievals
- preparing for the decommissioning of legacy facilities, such as concrete characterisation in preparation for pond dewatering
- conditioning, storage and disposal solutions for metallic uranic fuel and uranium bearing material
- assessing treatment and finishing requirements for unconditioned waste together with Letter of Compliance (LoC) requirements.
Corrosion of uranium in encapsulated products
For many years fuel debris containing uranium metal has been encapsulated in a grout matrix, typically consisting of ordinary Portland cement (OPC) and blast furnace slag (BFS), within a stainless-steel container for storage prior to disposal.
This method provides a solidified matrix containing immobile radioactive species and it is underpinned with an understanding of the corrosion behaviour of uranium within the matrix to provide confidence in the longterm package integrity.
More than 15 years ago, 2 sets of trials were initiated on uranium pennies in a range of matrices, undertaken in 25l ‘top-hat’ shaped vessels, designed to measure the rate of hydrogen generation and therefore calculate the corrosion rate of uranium metal:
Trial 1 - Sets of 32 pennies evenly distributed and suspended by cotton twine Trial 2 - Sets of 30 pennies suspended on multiple layers of plastic-coated stainless steel mesh at varying heights
Experimental matrices included varying OPC, BFS/OPC and PFA/OPC and several trials also contained inorganic simulants and an organic superplasticiser.
In 2016/17, 2 samples from trial one, were analysed in a controlled environment to preserve the nature of the retrieved corrosion product. The results indicated the presence of corrosion product, in the UO2-U3O7 range but that it was tightly constrained by the grout matrix despite its expansion into the matrix with some localised cracking.
Further analysis could not positively detect the presence of UH3 but minor quantities of this species could not be discounted.
Further recent investigative work was undertaken on samples from trial 2 in which the uranium pennies were found to have settled at the bottom of the cement matrix and therefore potentially representative of the encapsulation of uranium fragments within ‘bit bins’, legacy materials within FGMSP that may be cemented to form an encapsulated product.
Under controlled conditions, 28 corroded pennies were retrieved and characterised together with cement samples from the matrix.
Analysis showed that the grout matrix containing the samples appeared to be uniform, of high integrity despite uranium corrosion and expansion and had significant mechanical strength, with radial cracking adjacent to the immobilised uranium pennies.
The research concluded that:
- there was a broad distribution of corrosion rates, consistent with expectations
- the corrosion product lay in the UO2 -U3O7 range. None of the uranium samples contained detectable levels of UH3 on inspection using x-ray diffraction
- there was some variation in the extent of uranium corrosion suggesting that oxygen ingress into the cement matrix appeared to be limited to specific areas within the grout and therefore cracking was not continuous throughout the matrix
- corrosion behaviour of uranium is not significantly altered over varying geometries of the uranium within a grouted product.
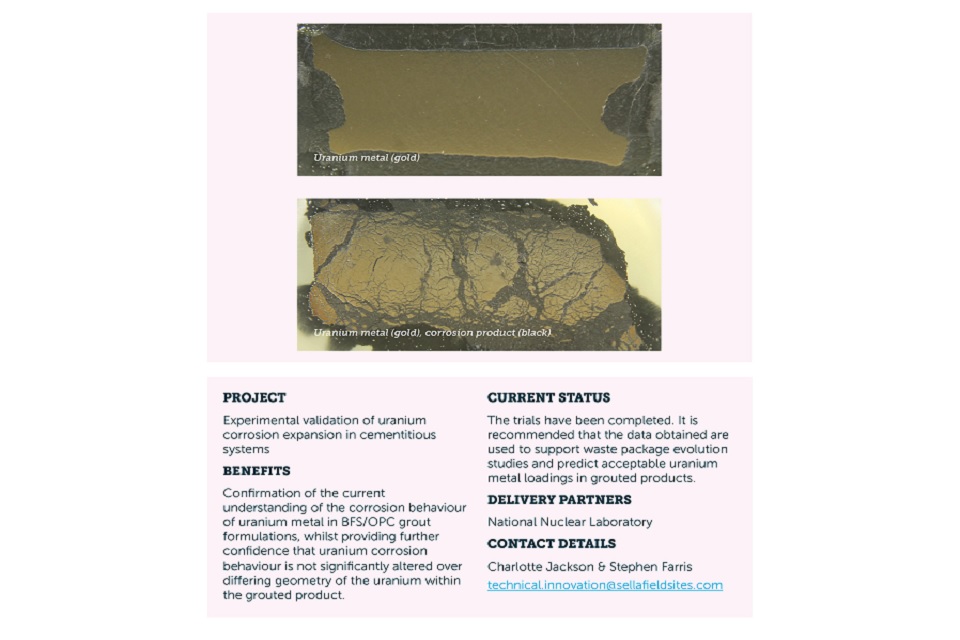
Development of in-situ monitoring for waste packages
facilities it will be packaged and stored in surface stores on the Sellafield site and it is important that the performance of the packages is as expected and that this can be demonstrated through condition monitoring and inspection (CM&I).
Sellafield Ltd is supporting the development of a combination of solutions; in-situ techniques that can monitor packages without removal from the store, and ex-situ techniques to monitor packages removed from the store into a designated area.
In addition to monitoring temperature, humidity, activity in air, contamination deposition and acoustic deflagration detection, the intended in-situ CM&I regime will usevisual external package monitoring through in-store cameras and thermal imagers.
In-situ thermal monitoring is subject to performance indicators and trigger levels, which highlight the degree of non-conformance of any packages, identifying those which may require further monitoring via ex-situ CM&I.
Thermal imaging trials were undertaken by TÜV SÜD - Nuclear Technologies Division and RED Engineering to assess the practicality of identifying problematic packages within the store, using scaled down 3m3 boxes in a stack arrangement.
This showed that the thermal cameras are able to pick up variations in temperature between boxes and between smaller items.
The trials demonstrated that the thermal camera measurement was accurate regardless of the distance between the camera and test box. The trials also used Light Detection and Ranging (LIDAR) and showed that a small movement in a box stack can be identified.
The final test in these trials was to monitor a full scale 3m3 box and the effect of internal heating on the external box surfaces.
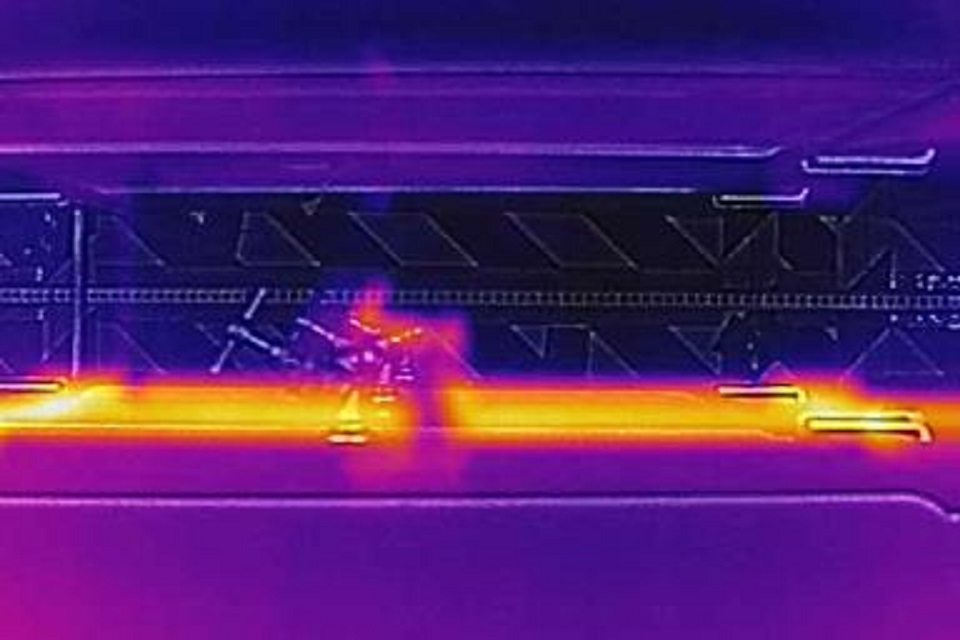
Thermal imaging of the gaps between stacks of scaled down 3m3 boxes (RED Engineering trials)
In parallel to this, the National Physical Laboratory (NPL) studied the feasibility and proof-of-concept of thermal imaging for identifying higher temperature 3m3 boxes within a store, using scaled down boxes, including measuring the surface temperatures of filters and box wall temperature between stacks.
NPL reviewed the state-of the-art thermal imagers to determine the most viable for deployment into the stores. The work also included testing the thermal imager’s ability to detect gaseous discharge from the waste packages.
Project - Development of in-situ monitoring for waste packages
Benefits
To provide confidence that unconditioned wastes are evolving as predicted and evidence that an appropriate level of CM&I can be provided in line with regulatory expectations.
Current status - Thermal imaging is considered to be a viable technique for in-situ monitoring and inspection of waste packages as evidenced by the successful demonstrations. Further technical trials and an assessment of the plant deployment methodology is expected to be undertaken in 2020/21.
Delivery partners - RED Engineering, TÜV SÜD - Nuclear Technologies Division, National Physical Laboratory
Contact details - Alex Allen technical.innovation@sellafieldsites.com
Developement of ex-situ monitoring for waste packages
Ex-situ CM&I (monitoring packages once removed from the store) will be used to confirm waste packages are trending within the expected envelopes through routine sampling of packages, or through monitoring specific packages identified by in-situ CM&I.
Ex-situ CM&I will provide a greater quality of information but has a greater number of constraints than insitu CM&I due to space and movement restrictions.
The 2 ex-situ technologies currently under investigation are high energy x-ray imaging and muon tomography. Proof of principle trials on both techniques were undertaken in 2019/20.
High energy x-ray imaging trials
This technique provides the capability to examine very dense materials and a typical arrangement utilises a fan beam x-ray moving along a frame along rails to monitor the side profile of a package.
X-ray photons are absorbed by high density materials, fewer photons pass through these materials resulting in a profile of a package showing different material densities.
Two trials were undertaken by Jacobs at Rapiscan Systems to evaluate the feasibility of the technique with the following results:
Trial 1 - successfully demonstrated the ability of the technology to measure the water levels within a wooden box, distinguish sludge from water and identified high density objects including steel and lead.
Trial 2 - used the same wooden box as the first trial together with a full scale MSSS 3m3 box and was successful in determining both sludge and water levels in both containers. This trial was also used to determine the optimal angle for the x-ray beam.
Muon tomography
Muons naturally occurring from background radiation are highly penetrating particles that can be used to identify materials based on their densities.
The technology used by Lynkeos Technology Ltd. uses detector panels above and below the package to generate a 3D image of the materials present from the path taken by the muons through the detector system.
A number of trials were undertaken in 2019/20 on a scaled down version of the MSSS 3m3 box to identify high density materials within the box, monitor the integrity of the container wall and measure the sludge and water levels.
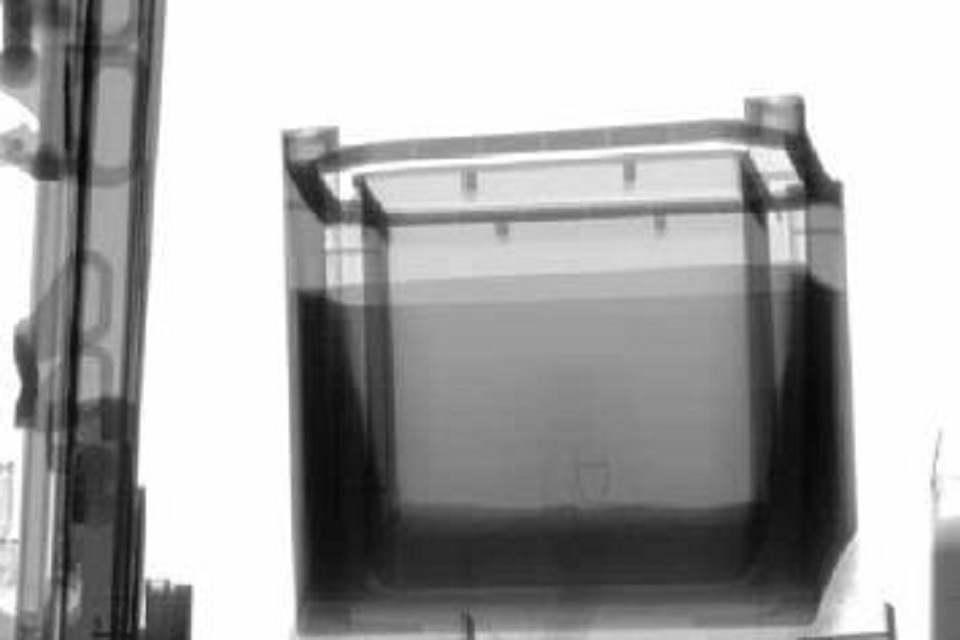
Side-view of a high energy x-ray scan of full scale 3m3 box
The assessment also evaluated the effects of the gamma dose on the detector capabilities. In parallel with these trials the feasibility of installation into the interim stores at Sellafield is being evaluated by React Engineering Ltd. and conclusions from this are expected in 2020/21.
Project - Development of ex-situ CM&I monitoring for waste packages using muon tomography and high energy x-ray imaging
Benefits
To provide confidence that unconditioned wastes are evolving as predicted and evidence that an appropriate level of CM&I can be provided in line with regulatory expectations.
Current status - This is an ongoing project with the most promising technology progressed through the TRL scale in 2020/21.
Delivery partners - Jacobs, Rapiscan Systems, National Nuclear Laboratory, Lynkeos Technology Ltd., REACT Engineering Ltd.
Contact details - Alex Allen technical.innovation@sellafieldsites.com
Stephen Farris, Cement and Process Centre of Expertise Lead
Stephen is part of the solids waste team which provides the technical expertise in support of legacy waste retrievals and disposal.
As CoE Lead he also provides independent support to both operational and future encapsulation plants and processes, technical oversight of research projects such as alternative encapsulants and is a member of the NDA Encapsulation Coordination Group which is responsible for addressing supply issues for cementitious materials across the NDA estate.
With a BSc (Hons) in Materials Chemistry, Stephen’s expertise in cementitious materials started with his PhD at Keele University followed by early career years with microscopy and thermal services at Blue Circle Cement, primarily responsible for the analysis of products for UK based manufacturing.
He then joined the Waste Encapsulation team in BNFL’s R&T function in 2001 providing technical support to the encapsulation plants. A change in scenery took Stephen to Dounreay for 9 years with Cavendish Nuclear (formerly UKAEA) where he focussed on encapsulation formulation development for liquid and solid wastes and had additional opportunities for work at other UK nuclear sites and in the US.
Stephen’s return to Cumbria in 2015 was prompted by the opportunity to become involved in the technical development work required to underpin the Box Encapsulation Plant (BEP) process, a major plant in the high hazard and risk reduction programme at Sellafield.
Stephen said:
Sellafield offers many opportunities to be involved in unique technical challenges. I enjoy working in a multidisciplinary environment providing novel solutions for legacy waste retrievals as well as the varied work arising within the CoE seeking to implement novel encapsulant materials where traditional cementitious materials may not be fit-for-purpose.
Charlotte Jackson, Scientific Degree Apprentice
Charlotte joined the Degree Apprenticeship Scheme in 2017 after leaving school with 3 A-Levels, she is in her third year of the programme and on successful completion will obtain a foundation degree in applied chemistry.
She then aims to continue her studies and progress to a BSc.
Charlotte is part of Strategy and Technical and a member of the cement and process CoE carrying out a variety of technical tasks.
Some of the projects in which she has been involved include finishing plant requirements for legacy waste 3m3 boxes, water transport mechanisms into annular cemented silo cans and trials work to support the alternative encapsulant materials programme.
Charlotte will be working towards Chartered Chemist status with the RSC in the coming years as her degree work and experience progresses.
Charlotte said:
I enjoy being on the degree apprenticeship scheme with Sellafield Ltd as it allows me to engage and work on a wide array of topics.
I am able to apply the chemistry I have learned to my role which reinforces my understanding and is of substantial benefit.
Remediation
The Remediation value stream is responsible for the clean-up of nuclear and non-nuclear facilities across the Sellafield site with the R&D programme focussing on:
- characterisation, POCO and decontamination of facilities
- forecasting and modelling to support decommissioning planning
- enablers such as access to facilities, deployment platforms, containment systems and operator working conditions
- tools and techniques for the removal of plant and equipment
- surveillance and maintenance and care and maintenance tools and techniques
- a range of waste processing technologies for waste treatment and conditioning
- waste transfer, handling, storage and export
- developments in demolition techniques
- land remediation technologies
- waste disposal and records
Reducing the size of gloveboxes for disposal
Gloveboxes used for research, development and operations that have come to the end of their life will be decommissioned as part of the site’s clean-up programme.
Many of these are contaminated with alpha bearing material and current decommissioning plans include manual techniques which are often hazardous and time consuming.
There is a driver to address this challenge using alternative technologies to deliver safer, more efficient decommissioning at a lower cost.
The alpha active demonstrator consists of a facility that will be used to test technologies for decommissioning, it is an ongoing project which aims to:
- generate data to underpin the strategy for managing large alpha contaminated items such as gloveboxes
- test the process on sufficient gloveboxes so that it may be optimised with opportunities to learn from experience
- explore the opportunity to enhance the capability with other technologies and techniques if there is sufficient demand and benefit
Working with the supply chain, the first stage of the project, in 2019/20, focussed on the refurbishment of a laboratory in a quiescent facility on the Sellafield site into a laser cutting modular facility ready for trials which will commence in 2020/21.
These will be on non-active surrogate boxes followed by active ones and include:
- laser cutting of alpha contaminated gloveboxes using a 6 degrees of freedom robotic arm
- recovery of waste with minimum human intervention
Project - Alpha active demonstrator
Benefits
The project aims to develop a safer process for the size reduction of alpha contaminated items that is more efficient when compared to manual approaches. The demonstrations will generate operational data that will aid decision making.
Current status - The project is ongoing with the facility ready for non-active trials planned for 2020/21.
Delivery partners - Integrated Decommissioning Solutions (IDS), Taylor Kightley Engineering Co.Ltd., Lasermet Ltd., Cyan Tec Systems Ltd.
Contact details - Alan Cardwell future.decommissioning@sellafieldsites.com
Waste processing of legacy plutonium contaminated material
Management of plutonium contaminated material (PCM) is expensive and over the lifetime expected for the Sellafield site, this cost will be very significant.
A major benefit in the management of PCM is through the improved sorting and segregation of items that fall into the low level waste (LLW) category and Sellafield Ltd has been supporting work to develop this capability for the past 2 years.
The alpha sort and segregation project aims to improve PCM/LLW separation by developing a process for decontamination, waste sorting, segregation and assay within an active demonstration facility and by optimising the approach by processing legacy crates through it.
The methodology for processing legacy crates in an active demonstration facility will require a range of capabilities such as:
- operations using manual techniques for a range of working conditions, from substantially clean to those requiring appropriate respiratory protection (i.e. C2 to C5)
- local containment options to manage the spread of contamination
- a toolbox of decontamination, characterisation, and size reduction techniques
- robust ‘real-time’ sentencing of PCM/LLW
- transportation and import routes for legacy crates
- export routes for PCM and LLW
Project - Alpha sort and segregation active demonstrator
Benefits
The project aims to develop an improved and cost-effective method for sorting and segregation of alpha contaminated wastes. The demonstrations will process legacy crates so that the approach may be tested and optimised and therefore aid the decision making for a future facility.
Current status - The project is ongoing with the preliminary design work completed. A contract has been placed with Cumbria Nuclear Solutions Ltd. via the DDP framework to cover the next phase which includes detailed design through to non-active commissioning.
Delivery partners - Cumbria Nuclear Solutions Ltd. with sub-contractors: North West Projects Ltd. and Cavendish Nuclear Ltd.
Contact details - Bill Johnson future.decommissioning@sellafieldsites.com
Characterisation and size reduction of borderline intermediate level waste
There are some larger items in Sellafield facilities that are categorised as intermediate level waste (ILW) but for which the level of radioactivity means that they can be handled without the need for special remote operations.
This is called contact handled ILW (CHILW) or discrete items.
The removal of high hazard wastes from legacy facilities is constrained by the current limited options for handling items of this nature. As more plants are decommissioned a capability is needed to process discrete items in accordance with best achievable technique (BAT) to generate waste forms suitable for storage and disposal and to reduce the burden on higher activity storage facilities.
Working with the supply chain, a project has been initiated to develop an active demonstration facility with the capability to process large items that fall into this category, using FGMSP wastes as the feedstock.
The facility will provide a number of significant benefits and aims to:
Enable acceleration of the retrievals programme
Currently items that are too large for miscellaneous beta gamma waste (MBGW) storage containers are transferred to the Windscale Advanced Gas-cooled Reactor (WAGR) store.
Processing these items in the new demonstration facility will create storage capacity in the WAGR store which will enable removal of miscellaneous items from FGMSP Wet Bays and allow access to fuel and sludge.
Provide capability for improved characterisation of waste in a lower background area, size reduction and liquor removal.
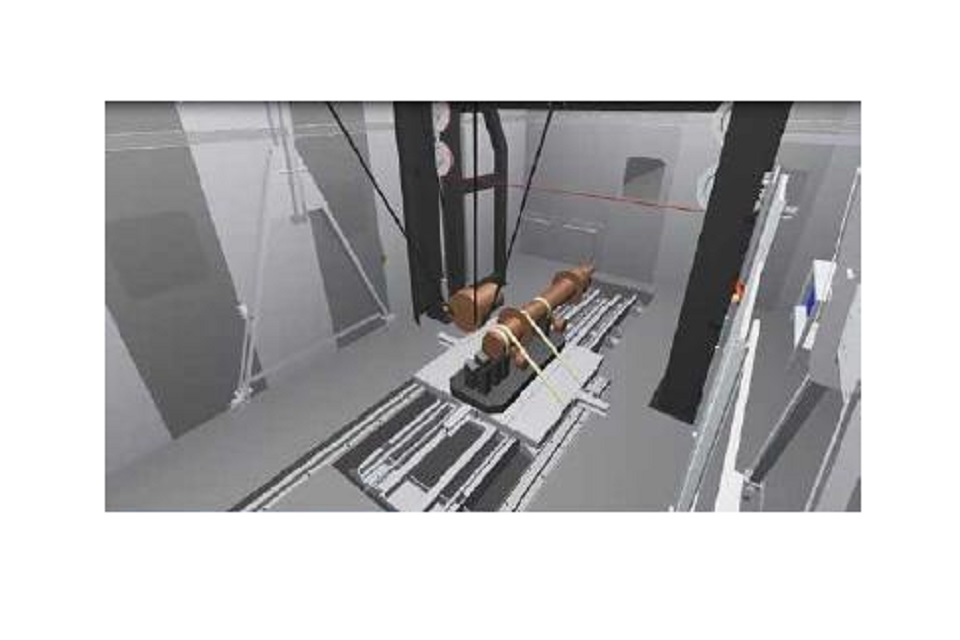
Representation of the facility with diamond wire cutting technology to size reduce large items
To date, items of this nature and level of activity do not have a waste route.
The project is innovative and has seen successful collaboration between Sellafield Ltd and Integrated Decommissioning Solutions.
The current phase of the project began in September 2019 with all of the equipment procured including a factory tested diamond wire cutter and ongoing enabling work to modify the building which will house the facility on-site.
Project - Decommissioning Waste Services Partnership
Benefits
The project aims to understand the requirements for a large scale CHILW handling facility and to aid decision making for it.
The demonstration facility will provide characterisation and size reduction in a way that is currently not possible and in the short term it will enable the retrievals of legacy wastes to continue.
Current status - The project is ongoing with plans for the next phase progressing, the scope of which will be to process items directly from FGMSP with parallel work to capture learning from the active demonstrator.
Delivery partners - Integrated Decommissioning Solutions
Contact details - Rachel Campbell future.decommissioning@sellafieldsites.com
Chirs Hope, Remedation Capability Development Manager
Chris manages a team of 20 people responsible for identifying, developing, demonstrating and implementing new technologies, techniques, waste routes and processes to address the remediation challenges across the Sellafield site using a wide range of methodologies from feasibility studies to active demonstration.
His team aims to deliver five major active demonstrators, which have the potential to enable a step change in decommissioning and waste management for the future.
They include remote and semi-remote size reduction of large waste items, in cell decommissioning, enhanced characterisation waste sorting and segregation.
After graduating from university with a BSc (Hons) in Marine Chemistry, Chris joined Sellafield Ltd as an environmental specialist before moving into a technical specialist role.
He spent time developing expertise in solid waste management, in particular characterisation, compliance and disposal requirements. In his next role Chris managed a small team to deliver characterisation projects for a range of customers across the site before moving to Future Decommissioning, the predecessor to the current team.
He was able to take an active role in the structure and direction of the team and became its manager in 2018.
Chris said:
I enjoy promoting new technologies with the aim of making a significant impact on the nuclear industry, by overseeing diverse challenges that are first of their kind.
I also take pleasure in working with the various disciplines within the business and the supply chain to help reach this aim.
Alan Cardwell, Alpha Active Demonstrator Manager
Alan has had a very interesting and varied career in the nuclear industry for 36 years. He currently works as part of an integrated team made up of Sellafield Ltd, IDS and CNSL personnel with a part challenges.
The team has taken a major project to manage large alpha contaminated items from initial concept through to installation and testing in two and a half years.
Following completion of his apprenticeship with BNFL, Alan spent many years at Calder Hall first as an electrician and finally as the foreman responsible for the day to day operations of the Turbine A Station.
When Calder Hall ceased generation, Alan moved onto decommissioning projects developing expertise in glovebox and vessel removal and continued his professional development by gaining a foundation degree in project management and project control.
Alan said:
I’m particularly proud to be working as part of the Active Demonstrator Team with our supply chain; partnering with IDS/ CNSL, I’m currently based at the Atkins office on the Westlakes Science Park, this really helps form great working relationships with key individuals who want to make a difference and change the way in which we work on the Sellafield site, it is both inspiring and rewarding.
Remote characterisation of inaccessible areas
Nuclear environments are extreme, they are often congested with complex networks of pipes and vessels, access issues and little room for manoeuvre, making decommissioning operations complicated.
Added to this, they can be very hazardous for the nuclear operator with dose intensive, contaminated conditions. data collection, is an essential part in the decommissioning planning process, generating radiological, physical and chemical information about the environment which can be very challenging in complex contaminated environments.
One potential solution is to use remote characterisation using ground based robotic technologies to access areas.
Sellafield Ltd has been working with RED Engineering, to adapt an off-the-shelf remotely operated robotic platform for use in contaminated facilities and in 2019/20 tested the technology, which has the following modifications:
- aether for communications, power and retrievals
- detachable wheels so they can be decontaminated or changed to suit the terrain
- electronics sealed into the base unit for easy decontamination
- a baseplate designed to handle varying payloads of characterisation equipment and is fitted above front and rear facing camera and light systems
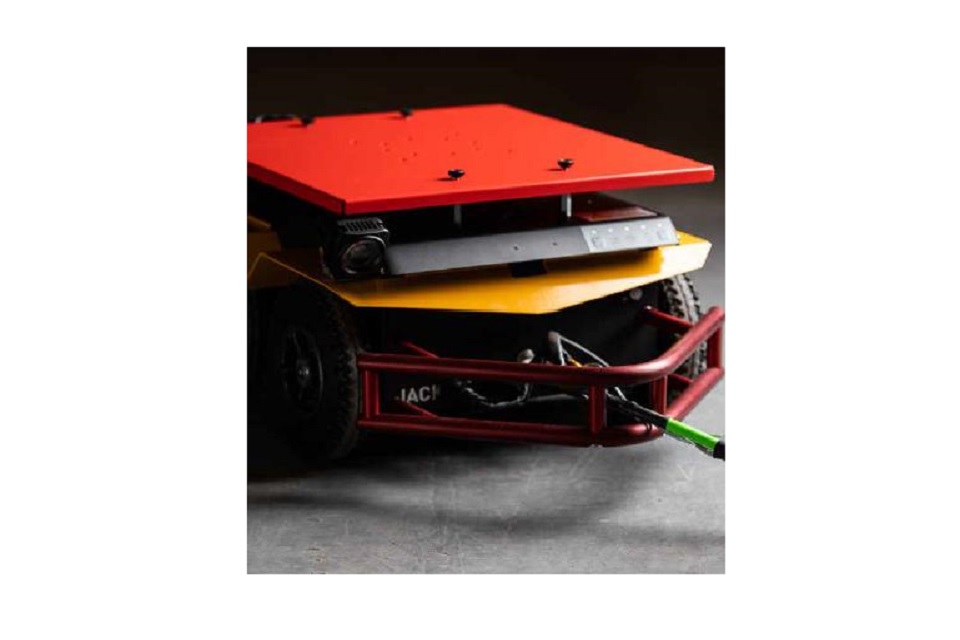
Ground based robotic platform adapted for use in contaminated environments
Project - Ground based robotic platforms
Benefits
Improved safety by providing a remote solution to the characterisation challenges in contaminated and congested environments.
Current status - Testing of the technology has been completed and further demonstrations are planned in 2020/21.
Delivery partners - RED Engineering
Contact details - James Sant future.decommissioning@sellafieldsites.com
In-situ analysis of lead
Challenges on the Sellafield site can often include other hazardous materials such as metallic and wooden items coated with lead-based paint, particularly from legacy facilities, these items need to be managed and sentenced correctly for disposal.
Painted items from buildings known to have used lead-based paint are currently either sentenced as hazardous waste or samples are sent for off-site analysis.
In-situ analysis of these materials offer significant benefits in terms of quicker analysis, less secondary waste and reduced costs.
In 2019/20, a study was undertaken to identify commercially available technologies to detect and/or analyse potentially hazardous materials in-situ and it concluded that hand-held x-ray fluorescence (XRF) devices will provide these benefits.
XRF is an established and widely used technique for elemental analysis of a broad range of materials such as metals, plastic and building materials.
Although XRFs are routinely used on the Sellafield site, in 2019/20, a new model was tested to expand portable analytical capability to routine lead screening.
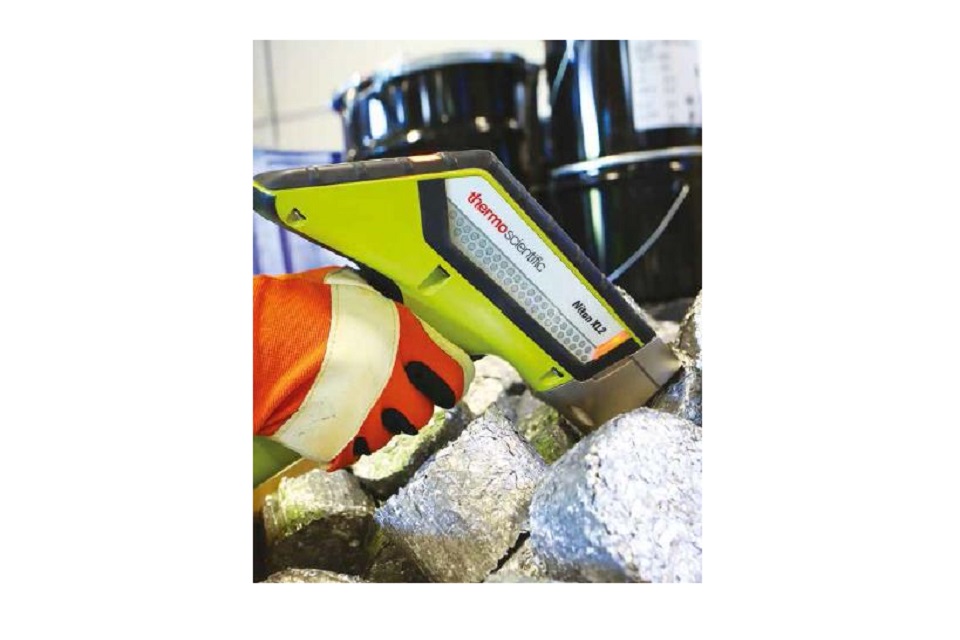
Portable XRF analyser on metal billets (Courtesy of Niton UK)
Project - X-ray fluorescence analyser
Benefits
In-situ analysis has the potential to offer significant benefits in terms of quicker analysis, less secondary waste and enabling real-time decision making.
Current status - This equipment can now be used routinely on-site, once personnel are trained.
Delivery partners - Niton UK
Contact details - James Sant future.decommissioning@sellafieldsites.com
Dan Fielden - Waste Capabiltiy Development Manager
After graduating from Newcastle University with a BSc (Hons) in Chemistry, Dan spent six years with OCF, a company delivering high performance computing, he joined Sellafield Ltd in 2007 and has held various waste management and technical roles in functions across the site.
His broad expertise in environmental and waste management comes from overseeing aerial effluent discharges, understanding the environmental perspective of design, construction and commissioning of major new build projects and advising on all areas of waste across the Sellafield site.
Dan now manages the team tasked with identifying, trialling and implementing new waste management and characterisation technologies, processes, waste routes and logistical improvements on the Sellafield site.
The team is responsible for a diverse portfolio, often managing more than 10 live large projects at any one time. It works closely with the supply chain and various other internal groups including radiometric, I.T, characterisation and legal specialists with the aim of creating an efficient, compliant and economic waste management tool box suitable for Sellafield Ltd’s future mission.
Dan is a Chartered Chemist and a Chartered Environmentalist with the Royal Society of Chemistry.
Dan said:
I really enjoy the challenge of changing the way we work at Sellafield to prepare us for our future mission. It is critical that, as a company, we evolve and develop our technology and processes, as other industries have done.
Nowhere is this more important than in waste management as everything we are trying to achieve ultimately produces waste which needs to be dealt with.
James Sant - Capability Development Team Member
James joined the team as a degree apprentice spending his first year on projects such as biometric vests and photogrammetric technology. After completing a secondment in Alpha Package Delivery, he returned to the team to progress technologies for integration into the business, including ground based deployment platforms and in-situ chemotoxic analysis.
As part of his role, James, assesses commercially off-the-shelf technologies for their suitability against challenges and their potential to bring new capabilities to the business.
In parallel with his daily activities James has gained a foundation degree in plant engineering and is now working towards.
I believe the learning and experience I am getting at Sellafield has been amazing. It has been interesting working with a variety of Sellafield Ltd teams and the supply chain in bringing new technologies onto site and seeing the impact on how we carry out projects.
I’m looking forward to getting involved with more projects and seeing the ones I’m currently working on come into fruition.
Remediation Capability Development Team
As the mission at Sellafield changes from reprocessing operations to decommissioning and waste treatment activities, the business is continuously identifying opportunities where innovative technologies can be adopted to improve safety, efficiency or reduce wastes.
An important part of this process is the demonstration programme managed by the Remediation Capability Development Team, which acts as the interface between the supply chain and end users on plants.
Through engagement with the value streams, the supply chain and the NDA, the team aims to identify potential solutions that may be able to address a specific gap in the Sellafield technology ‘toolkit’.
To meet the needs of the value streams, the team undertakes small scale technology trials, these are compared with current baseline decommissioning and waste management approaches to see if they offer safer, faster or cheaper solutions.
This is achieved by:
- analysing the benefit of commercial off-the-shelf technologies
- supporting innovation in the supply chain, to adapt tools or techniques
- supporting lower TRL research through central technical
The team has grown and strengthened it’s skills over the years with professionals dedicated to each of these approaches.
It has overseen a number of major active demonstrators incorporating several new technologies and techniques to solve the Remediation value stream key challenges. These have reached varying levels of maturity and as well as delivering solutions, they are able to offer the opportunity to change the way in which people work in the business.
In 2020 the team expanded further to include capabilities for the management of waste from the high hazard risk reduction programme and from the large volumes of excavated material generated by the major new build projects.
To find out more contact - The Remediation Capability Development Team future.decommissioning@sellafieldsites.com
Click on the link for more information on the Integrated Innovation in Nuclear Decommissioning (IIND) competition.
Remediation Capability Development Team
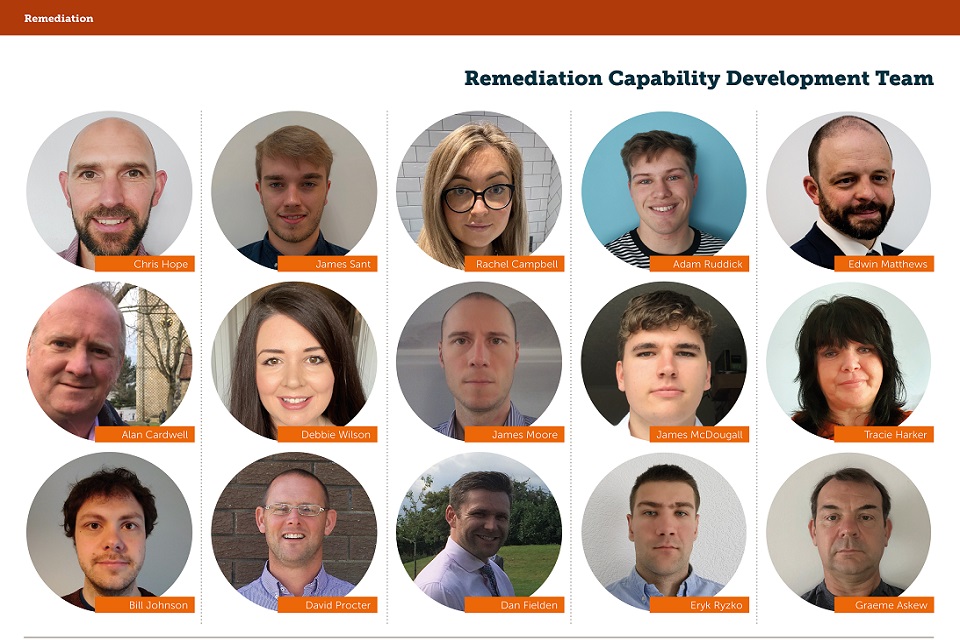
Environmental Management
The Environmental Management Team comprises of 30 technical staff, is part of the Sellafield Ltd Environment, Safety and Security Directorate and acts for the benefit of the whole site for:
- environmental compliance and standards
- environmental monitoring and assessment both on and off the site
- obtaining and maintaining permits
- strategic direction of the capability
The team forms part of the wider environmental community which extends across the business with local environmental specialists responsible for ensuring that operational and planned activities are consistent with environmental requirements.
How R&D supports environmental compliance at Sellafield
Environmental permits are issued by the Environment Agency (EA) and are a legal requirement that allows Sellafield Ltd to operate facilities, discharge into the environment and dispose of solid waste.
This includes an obligation on the site to ensure that decisions made today continue to remain valid into the future as articulated through the Environment Agency RSA guidance:
<What constitutes BAT and an optimised outcome will evolve over time, to reflect changes in, for example, technology, knowledge and local environmental issues. This means that the operator must keep these matters under review and be ready to implement changes.
Click on the link for more information on the guidance.
The 2 main permits are:
- Radioactive Substance Activities (RSA) Permit
- Installations Permit
The application of best available techniques (BAT) across the Sellafield site is a means by which Sellafield Ltd is able to demonstrate compliance with these permits and R&D is key to supporting the application of BAT. This article presents two recent case studies on the application of R&D for optimising the delivery of the Sellafield Ltd’s environmental responsibilities and discusses the future strategic direction:
- aerial discharges
- the beach monitoring programme
Aerial discharges
Sellafield’s aerial discharges have reduced significantly over the years to very low levels, particularly due to the widespread use of abatement processes such as caustic scrubbers and HEPA filtration, but also as a direct consequence of operational facilities reducing throughputs and ramping down or ceasing operations.
They are typically measured and reported at the analytical ‘limit of detection’ (LOD). Given the large number of ‘accountancy’ sample points and high volumes of air through the ventilation systems radioactive aerial discharges are ‘over reported’ and due to the analytical methods involved the costs are considerable.
Through agreement with the EA a number of changes have been made to the RSA permit to enhance operational flexibility and to how discharges are reported.
Discharge limits
The site’s discharge limits were optimised through a major review of the RSA Environmental Permit effective from April 2020.
This review introduced a tiered approach to the site’s limits and therefore flexibility for operations, recognising that whilst the environmental impact of routine Sellafield aerial and liquid discharges is now extremely low, significant challenges remain in managing wastes and discharges from future operations with potentially varying discharges.
Standard reporting
The EA has prepared and issued guidance for the reporting of discharges to minimise over reporting where discharges are typically LOD and where there is evidence to show that nothing has changed. In these cases, discharges can be reported as a ‘standard value’, however monitoring remains an option if required.
The EA has agreed to the implementation of this method for reporting discharges from the Separation Area Ventilation (SAV) stack following a BAT case made in the major review of the RSA Environmental Permit. Once implemented the experience with the SAV plant will be used to share best practice for similar cases across the site.
Through this work the site has demonstrated the application of BAT and realised considerable cost benefits and significant improvements in the reporting of radioactive aerial discharges.
The future
A key future environmental challenge relates to preparing and strengthening the business in the face of a changing climate.
In the more immediate future, ongoing research will explore how Sellafield’s carbon footprint will change between now and 2050 and how this will contribute to the UK Government’s 2050 net zero commitment.
Some carbon reduction improvements are already progressing well, for example the introduction of ultra-low emission vehicles within the Sellafield Ltd fleet and installation of solar panels to an off-site location.
Going forward, research will help to predict the longer-term environmental effects through changes in factors such as utilities usage, aerial and liquid effluent discharges, solid waste generation, chemicals usage and construction work.
Planned work includes the potential use of modelling and scenario software to integrate other geopolitical drivers and understand how these could influence future mission delivery.
However, this is just a flavour of what’s happening. Sellafield Ltd’s sustainability principles will draw the link between delivering a sustainable mission and the global challenges being faced, through reference to the UN sustainable development goals and the second edition of the Annual Review of Sustainability will provide details of the progress being made across the business to meet its sustainability ambitions.
Both are due for publication in 2020.
For more information on the UN sustainable development goals visit their website.
The beach monitoring programme
Sellafield Ltd undertakes an ongoing programme to monitor radioactivity in the environment as a condition of the environmental permit issued by the EA.
For a number of years wide area beach monitoring has been provided by Nuvia Ltd., using a vehicle mounted detection system.
Operations must employ BAT and therefore reviews are undertaken periodically to consider all aspects of the programme including a cost-benefit analysis to ensure that the monitoring programme is proportionate and whether changes or modifications to the equipment or methodologies are required.
Detector technologies
The types of radiological detectors that could be applied for beach monitoring will be an important consideration for the forthcoming 2020 BAT assessment.
Golder Associates (UK) Ltd. and Eden Nuclear and Environment Ltd. have been commissioned to carry out a technology review, bringing together opinions from leading national and internationally recognised academic and industry experts.
In addition, in-house work has been progressed, trialling novel detector systems and methods of deployment. This includes trials of an unmanned aerial vehicle (UAV) system scheduled for later in 2020.
Outcomes and shared learning
The beach monitoring programme represents a significant investment by Sellafield Ltd and is high priority for stakeholders. The technology review will provide assurance that the most appropriate technologies and methods of deployment are currently being applied and it is an opportunity to identify likely avenues for future improvements to the programme to enable the timely realisation of benefits from new developments.
These include continuing to ensure that the programme meets the requirements of stakeholders whilst optimising the resources required for the delivery of the work.
In addition, a wide interest has been expressed in the review across the NDA estate and the results will be shared with other SLCs for use in their BAT considerations.
Supply chain companies and organisations
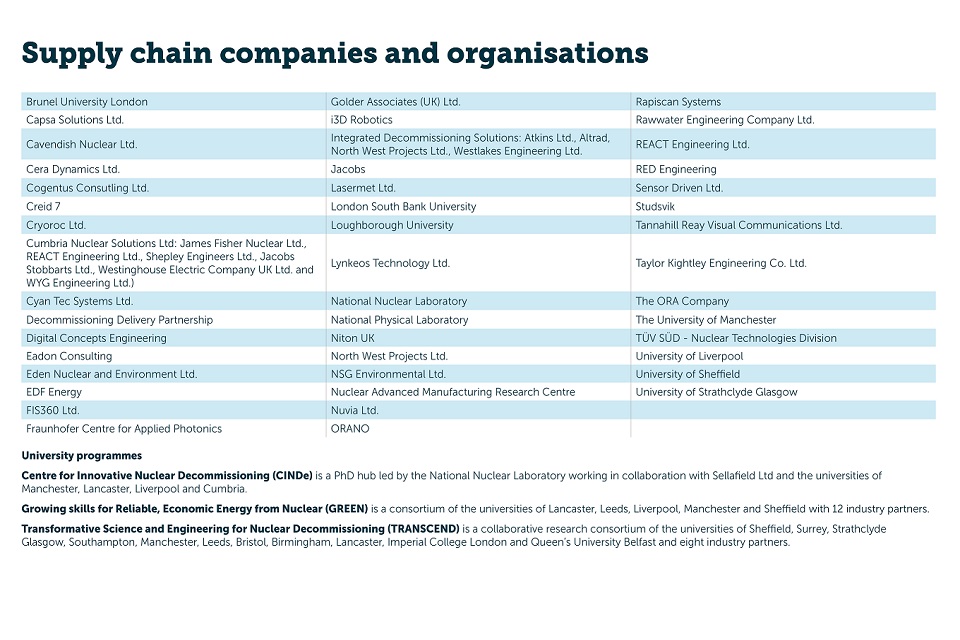
Abbreviations and acronyms
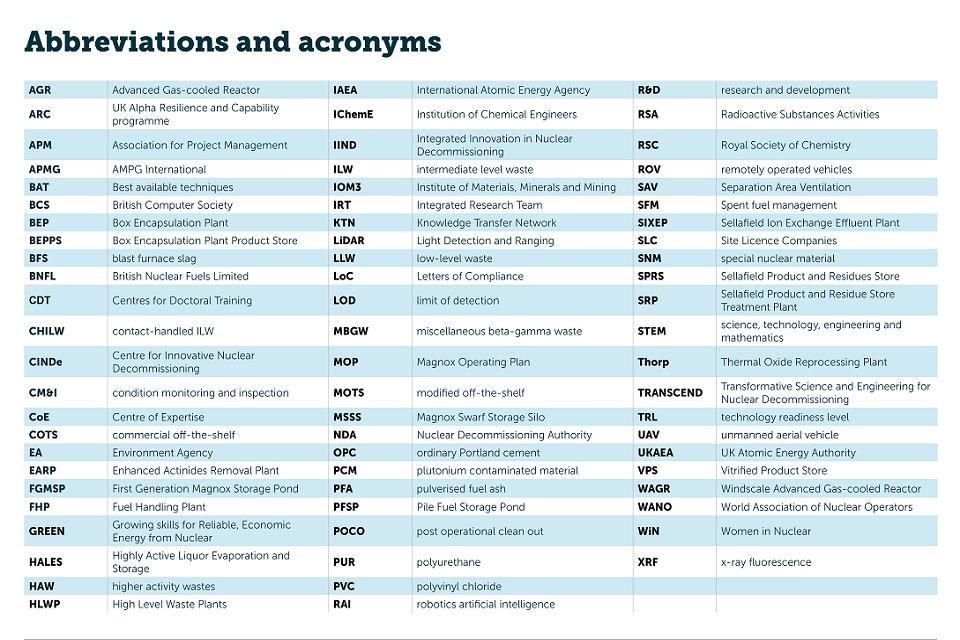