ETL800 Hot water, biomass and steam boilers
Updated 20 April 2020
Hot water boilers
Hot water boilers are products that are specifically designed to heat water by means of a heat exchanger that transfers heat from combustion into the water as it passes through the product. Hot water boilers are used to produce hot water for space heating, process heating and domestic uses.
The efficiency of hot water boilers is primarily determined by the surface area, arrangement and materials of construction of the heat exchangers and the design and control of burners.
The Energy Technology List (ETL) covers 4 categories of products:
- high temperature, high pressure, high efficiency hot water boilers with rated outputs greater than 400 kilowatts (kW). Boilers designed to operate with a water pressure greater than 6 bar and/or outlet water temperature greater than 105°C, and that are not designed to recover latent heat from flue gases by condensing water vapour.
- low temperature, low pressure, high efficiency hot water boilers with rated outputs greater than 400 kW. Boilers designed to operate with a water pressure up to and including 105°C that are not designed to recover latent heat from flue gases by condensing water vapour.
- condensing hot water boilers with rated outputs greater than 70 kW. Boilers designed to recover latent heat from flue gas water vapour.
- condensing hot water boilers with rated outputs up to 70 kW. Boilers designed to recover latent heat from flue gas water vapour.
Example
By installing an ETL listed, gas-fired, condensing hot water boiler with an output of 200 kW, as opposed to a new, non-ETL listed model, the potential annual savings are calculated as:
- £951
- 36.8 megawatt hours (MWh)
- 6.74 tonnes CO2
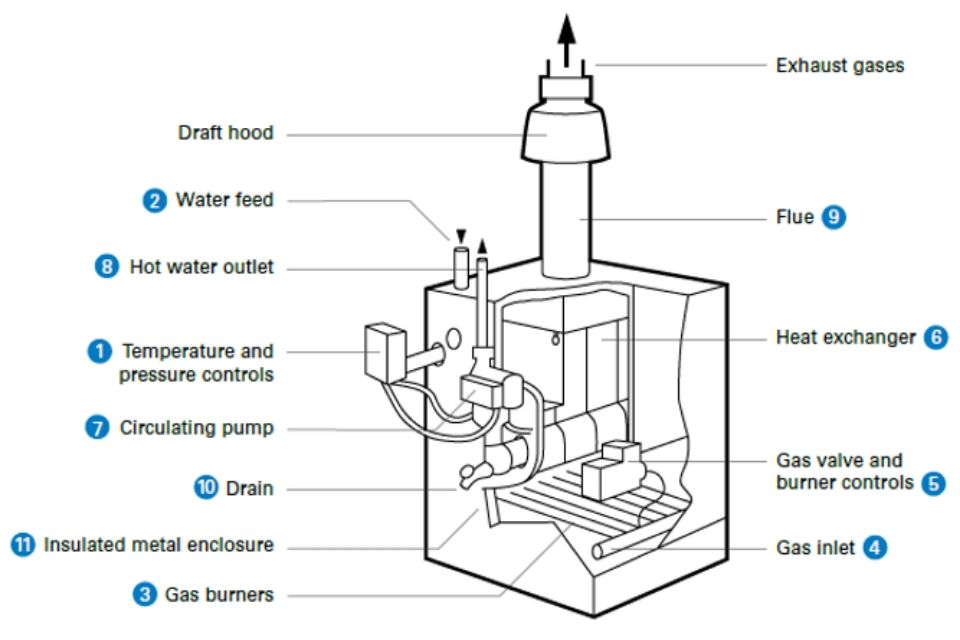
Biomass boilers
Biomass boilers are products that are specifically designed to burn solid biomass fuels (which include logs, wood pellets and wood chips) in order to heat water, for process or space heating.
Biomass boilers offer an alternative to fossil fuel boilers, in particular oil-fired boilers which are the main option for areas where mains gas is not available.
Changing from liquid petroleum gas (LPG) and oil-fired heating to wood fuel delivers CO2 emission savings of approximately 80% to 94%. Even when displacing natural gas, emission savings of between 73% and 90% are possible.
The main types of product available use the following processes:
- direct combustion of biomass is the most common process – where sufficient air is supplied to the burning fuel to ensure complete combustion
- 2-stage systems, which are less common for biomass boilers
- stage 1 – the fuel is either gasified by reacting it with a limited amount of air (insufficient air is supplied to allow combustion, or CO2 or steam is supplied instead of air); or pyrolyzed by heating in the absence of air
- both processes produce a fuel gas and solid char, and in Stage 2 both of these can be burned to release heat
Eligible biomass boilers must:
- be designed to burn wood, cereal straw, or solid fuels derived from them
- heat water for process or space heating
- meet the following air quality emission limits:
- particulate matter (PM) emissions must not exceed 30 grams per gigajoule (g/GJ) net heat input
- oxides of nitrogen (NOx) emissions must not exceed 150 grams per g/GJ net heat input
Biomass boilers are typically eligible for subsidies under the renewable heat incentive (RHI), which is a financial incentive and cannot be claimed alongside an ECA. Those looking to buy products should carefully consider the financial benefit from both schemes in order to select the most appropriate.
Example Installing a wood pellet-fired biomass boiler with an output of 180kW, running with a load factor of 25% and efficiency of 92%, as opposed to a new gas oil boiler offering the same energy output and 95% efficiency, the potential annual savings are:
- £1,375
- 0 kWh
- 112,767 tonnes CO2
Steam boilers
Steam boilers are products that are specifically designed to convert water into pressurised steam by means of a burner and use the steam for process heating, space heating and water heating. They consist of a burner, a pressure vessel containing a heat exchanger, and associated burner control systems and boiler control equipment.
The ETL aims to encourage the purchase of the higher efficiency gas and oil-fired steam boilers, including products that are designed to use liquid and gaseous biofuels.
Fuel savings from an ETL steam boiler compared to a typical non-specified energy savings ETL steam boiler are around 7%. Fuel savings of between 2% and 5% can be achieved at part load conditions by fitting a modulating ETL burner rather than a basic 2 stage (hi/low) burner.
Eligible steam boilers:
- can be gas and/or oil-fired
- must use an appropriately matched forced draught burner
- shall automatically respond to changes in steam demand by modulating their output in a continuous manner across a minimum specified turndown ratio without initiating a purge cycle
Steam boilers can be used for a wide variety of applications, including but not restricted to:
- distributing heat
- providing effective and safe humidification
- achieving efficient sterilisation
- using waste heat to provide chilled water
This extensive range of applications results in steam boilers being integral to both industry and commerce, especially within the chemicals, food and drink, paper, refining and primary metal manufacturing sectors.