Finding a replacement for HFE 7100
Published 31 December 2024
Cessation of HFE 7100 and requirements for a replacement
HFE 7100 was introduced in fingermark development processes as a replacement for chlorofluorocarbons (CFCs) following their discontinuation in the 1990s. The unreactive nature of HFE 7100 (and other similar chemicals) makes them ideal carrier solvents for amino acid processes. The environmental persistence of these ‘forever chemicals’ is a global cause for concern though. This is why 3M will cease manufacture of all per- and polyfluoroalkyl substances (PFAS) in 2025 (which includes Novec™ 7100)[footnote 1]. The European Chemical Agency (ECHA) has also proposed a ban on the manufacture and use of PFAS[footnote 2]. The earliest a ban could be enforced is mid-2026, if a derogation for forensic use is not granted.
We have developed the requirements for a replacement carrier solvent with UK Police Fingermark Enhancement Laboratories (FELs). These requirements include acceptance criteria for the functionality and performance of a new process, as well as the ranked priorities. The current focus of the fingerprint research team is to maintain an amino acid development capability within the PFAS restriction timeframe, through the reformulation of Indandione for laboratory use. The Defence Science and Technology Laboratory (Dstl) will monitor other developing research in the area. For example solvent-less approaches which could provide a more sustainable process in the future. These techniques are still in development and require optimising before undergoing validation.
Chemically equivalent replacements
‘Drop-in’ replacements with the same chemical structure as Novec™ 7100 are recently available to purchase. These products do currently come under the definition of PFAS, but they provide a short-term alternative to 3M’s Novec™ 7100.
Based on a market survey at the time of testing, Dstl analysed 2 of these chemically equivalent alternatives. These were:
- Samsol™ HFE71 FP, supplied by Samuel Banner Chemicals, UK
- Promosolv™ DR3, supplied by Inventec Performance Chemicals, France
This analysis found both solvents to have the same structure as Novec™ 7100. There was also no meaningful difference in purity that would affect performance. The suppliers also provided details of their own chemical analysis comparing their solvent to Novec™ 7100, which supports Dstl’s chemical analysis.
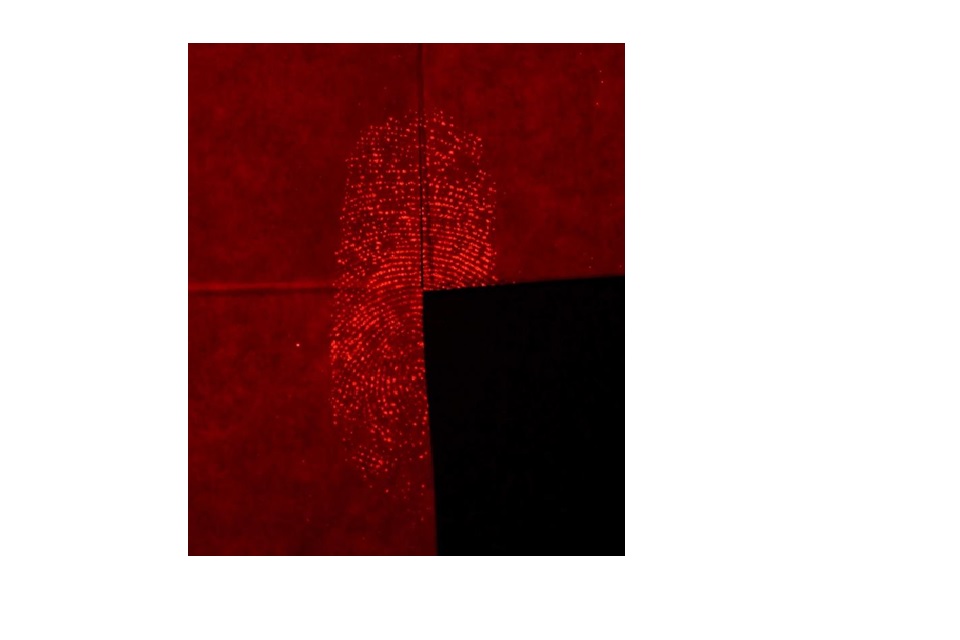
Figure 1: image of a quartered mark comparing Promosolv DR3 (top left), Novec™ 7100 (top right), and Samsol™HFE71 FP (bottom left).
We carried out a small performance test using these alternatives in a one-to-one swap for Novec™ 7100 in the FVM recommended Indandione formulation (figure 1). There were no observed differences in the quality of the mark visualised by either of the products.
Dstl’s analysis did not investigate batch variation, so we recommend basic assurance checks are carried out to satisfy organisational requirements. Other ‘drop in’ replacement products may be available - although these products have not been tested independently, they may also be suitable alternatives to Novec™ 7100.
Non-PFAS options
Chemically equivalent products help in the short-term to maintain fingermark development capability. FELs do need a suitable alternative that complies with the PFAS proposal though.
Option A: flammable solvents
Dstl surveyed international fingermark enhancement laboratories and completed a literature review. The survey identified alternative carrier solvents to HFE 7100 - flammable formulations are in regular use, with Petroleum Ether as the most common. During the CFC replacement, the fingermark research team investigated Heptane in the Ninhydrin formulation as another flammable alternative[footnote 3]. We have tested the reagent compatibility of Petroleum Ether and Heptane, and carried out comparisons of various formulations to establish performance to narrow down the options.
Initial screening tests did not use ovens while health and safety checks were explored. This increases development time by several days. This may not be as effective overall but it is an option to avoid heating items treated with flammable solvents. We do intend to repeat these experiments using an oven to achieve operationally representative results.
Health and safety
As Petroleum Ether and Heptane are both highly flammable, treatment of items must comply with appropriate controls. This ensures the safety of staff and meets UK legislation. Dstl have instructed an independent Dangerous Substances and Explosive Atmospheres (DSEAR) assessment on the process, which proposed recommendations to limit the hazard of heating these solvents.
One method being explored ensures the volume of solvent going into the oven is below the lower explosive limit. A robust process must be in place. This could include checks to ensure the item is fully dry before loading into the oven. This is less ideal for routine work and relies heavily on the:
- competence of the user
- type of substrate
- lab environment
An alternative method involves using a specialised oven designed to heat flammable solvents safely. As these ovens are designed for this purpose, they would provide an engineering control which reduces the possibility of user error. We are exploring commercially available ovens, but we need to determine the performance of flammable formulations first; by using our current development oven under strict protocols before we propose any recommendations.
Option B: non-flammable solvents
A solvent containing a mixture of isomers of 1-Chloro-2,3,3-trifluoropropene is sold under various trade names, including:
- Amolea™ AS-300
- Maxion™ 100
- Promosolv™ Neo A1
- Prosolv® AS-1
- Tergo™ XCF1
This chemical remains the focus of non-flammable solvent research as it is the only non-PFAS currently identified on the UK market that could replace HFE 7100. Dstl have completed early trials to determine its effectiveness as the carrier solvent in the current UK Indandione formulation. Initial indications are promising (figure 2), but performance is reduced on certain surfaces as the solvent can cause substantial ink running.
Figure 2: split mark test with Indandione formulations containing: Novec™ 7100 (left half), Amolea™ AS-300 (right half).
Ink running
Discussions with UK FELs highlight that the prevalence of ink on exhibits is significant. Substrates with written and printed inks have been included in exploratory testing to cover this requirement.
The initial approach looked at a pre-treatment process to either affix the ink to the substrate or to remove the ink before treatment. Ink fixatives were unsuccessful and, although the ink removal process was reasonably effective with most ink types, it could result in diffusion of the friction ridge detail if exposure was too long. If implemented into practice, it would be important to establish time-sensitive protocols to protect the fingermark evidence.
One of the key issues perpetuating the ink running was the over saturation and directional flow of the working solution using the trough method - currently employed in the amino acid technique. We are looking at alternative application methods to decrease both of these factors. Preliminary trials have looked at spraying to apply the Indandione working solution. Early results (seen in figures 3 and 4) are promising and so we will continue developing this method.
Figure 3: trough application of the Indandione formulation containing Amolea™ AS-300 (top) compared to sprayed application of the same formulation (bottom) on items with Biro ink (left) and Permanent Marker (right).
Next steps
Dstl will continue to refine both the flammable and non-flammable options; optimising each process before we conduct comparative experiments. We will also carry out a pseudo-operational trial to evaluate the performance in relation to the current HFE 7100-based formulation across more complex substrate types commonly encountered in UK FELs.
Although the chemically equivalent products provide a short-term replacement to the supply cessation of Novec™ 7100, Dstl aim to optimise a non-PFAS alternative for use in UK FELs to align with the potential introductions of PFAS restrictions in 2026.
-
D.F. HEWLETT and V.G. SEARS. Replacements for CFC113 in the Ninhydrin Process: Part 1. Journal of Forensic Identification, 1997, 47(3), 13. ↩
-
3M, 3M to exit PFAS manufacturing by the end of 2025, (accessed: 20 December 2022). ↩
-
EUROPEAN CHEMICALS AGENCY (ECHA), ECHA publishes PFAS restriction proposal, (accessed: 2023). ↩