Developing a suitable sampling methodology
Published 21 March 2024
As a materials facility (MF) operator you will develop, record and implement a methodology for sampling and measuring that meets all legal and statutory requirements.
Any sampling methodologies developed should be in writing, form part of your permit management system and must be made available to the regulators when requested.
You can select the most suitable methodology according to the available equipment, space and presentation of the materials, whether loose, bagged or baled.
Your sampling methodology must be robust, well documented and representative of the wastes received and operations used at your facility.
Your sampling methodology for taking samples should include, but is not limited to, the following information:
- the process for taking samples
- how the process for taking samples accounts for variations in the waste stream, suppliers and other variables, such as seasonality or on-site processes
- the type of weighing equipment used and how they are used to meet the requirements of the regulations
- evidence and records of the calibration of weighing equipment used
- if and how moisture content or presence of other contamination is accounted for and whether the sample weight is wet or dry weight
- details of training provided to the staff for taking a sample
- method used by staff to determine the different materials separated within the samples for measurements. This might include evidence and records of staff training
- the evidence for categorisation used, such as how materials are identified as target or non-target
- criteria used to assess what is packaging material
You can update your sampling methodology at any time if you ensure that the updates represent the MF’s current operations. Use document version control to make clear which methodology was being used during a given time period.
You can find information regarding appropriate risk assessments (specific to your operations), personal protective equipment (PPE) and control procedures in the Health and Safety Executive (HSE) guidance.
It is your responsibility to ensure that the staff undertaking sampling and measuring have received full training, both from a practical and a health and safety perspective.
Methods and considerations for taking samples
You may choose a suitable and appropriate sampling approach based on the operations carried out in your MF. Additionally, you may refer to the following methods and considerations while taking samples. These methods and considerations largely reflect manual sampling processes, although some may be applicable to the use of visual detection and recognition methodologies.
Use of visual detection and recognition technology to carry out sampling
There are no restrictions to the use of visual detection and recognition technology for MF sampling, including artificial intelligence technology. However, it will remain the responsibility of MF operators to measure, record and be able to demonstrate to the regulator how their sampling methodology meets the regulations and produces representative sampling results, whatever technology is in use.
See ‘Visual detection and recognition technologies’ for more information.
Designate a sampling area
Sample collection should be carried out in an undercover area where possible, sheltered from the elements and away from moving equipment and vehicles, including fork lift trucks and loading shovels.
You should consider a spacious area to allow waste to be isolated without getting cross contaminated with materials from other sources.
Use appropriate equipment for taking samples
You may choose to use the equipment suggested in this guidance or any other equivalent equipment based on your individual needs and circumstances.
While choosing equipment, you should consider equipment that is most appropriate for the task. For example, incoming waste material may be weighed on a weighbridge. However, a weighbridge will not be appropriate for weighing a 50kg sample.
A non-exhaustive list of typical equipment that you may use to gather samples includes :
- platform scales with a calibration certificate and a minimum accuracy of +/- 500g
- 1kg and 5kg weights for calibration of scales
- electronic tablets connected to the weighing scales to automate recording the weights of material being sampled
- shovels, brooms and containers for mixing samples, cleansing areas of spillages and sweeping up material particles for measurement
- long handled wire cutters for cutting straps on baled material
- different types of containers suitable for storing, transporting and weighing materials, such as stillages or bulk bags
- pickers for removing hazardous items, such as hypodermic needles
- sharps bins for safely disposing of sharps
- fork lift truck or hydraulic trolleys for transporting material from the sampling area to the measuring area
- loading shovel or telehandler for mixing samples and loading containers
- waterproof labels and pens for labelling samples
- sample sheets to record the sample measurements
- automated or mechanical bin lifts for emptying samples collected in wheeled bins onto the sorting area
Plan a schedule for taking samples
You should be able to demonstrate to the regulator that the approach you use for taking samples is structured and managed to provide representative results. Developing a sampling schedule at the start of each reporting period can form part of your sampling methodology.
The number of input samples you should include in your sampling schedule will depend on the overall weight of input waste material delivered by each supplier.
Similarly, the number of output samples will depend on the overall quantity of specified output material produced by your MF.
The guidance on waste sampling and reporting has more information on sampling frequency.
Regular monitoring and recording of incoming and outgoing waste material weights can support sample collection planning.
For input sample schedules, you may consider the tonnages for each supplier as a guide for the number of input samples for that supplier. In doing so, considering the same reporting period in the previous year will help provide a representative estimate.
Where you receive waste from irregular customers that may supply smaller amounts of waste material at unknown frequencies, you will need to consider and determine when and how to take a sample for each 75 tonnes of the supplier’s waste received in a reporting period. This should be reflected in your sampling methodology.
For output sample schedules, you may consider total tonnage of specified output material produced by your MF for determining the number of output samples required. In doing so, considering the same reporting period in the previous year will help provide a representative estimate.
When developing a sampling schedule you may consider:
- accounting for variations in the composition and quality of input material due to supplier, collection rounds or seasons
- accounting for changes in output material due to the speed of the sorting process, timing, day or shift
- accounting for quality and composition variations by sampling regularly and frequently assessing inputs from different suppliers prior to waste consolidation
Taking a sample
You may remove any exceptional items, such as large or heavy items that might damage equipment or impact on the sorting process prior to taking a sample. These items do not need to be weighed as part of the sample. You should avoid any other sorting activity prior to taking a sample.
You can choose different sampling approaches depending on whether the incoming waste material and specified output materials is loose, bagged or baled.
You may consider the following while sampling incoming or outgoing material :
- mixing the sample to redistribute heavy items, such as glass bottles, that have settled to the bottom of the load
- using a support structure and tools, such as push walls and loading shovels, to allow easy mixing of samples if needed
For sampling from loose material, you may mix the material by separating a proportion of the load, lifting it up and dropping it back on the floor at least twice using a loading shovel. You may choose your own sampling methodology but may want to consider the following :
- removing a slice or section from each end of the tipped material and shovelling these into appropriate sample storage containers
- direct tipping of material into a container using a loading shovel until it fills up to the appropriate level and correct sample weight.
- using a divert loop from the main conveyor belt, to gather the sample from incoming waste material at the start of the sorting process for input material
Similar considerations can apply to sampling of specified output material. You may also consider :
- adding divert loops to conveyor belts carrying the specified output material and directing them to the sample collection and storage containers
- adding a suitable container or bulk bag under the conveyor that feeds the storage bay to gather the required sample weight
- gathering a sample from the output material storage bay using appropriate methods depending on whether the material is loose, bagged or baled
While sampling bagged material, selecting a range of bag sizes and weights can enable randomisation of the sample. Randomisation helps to ensure that the gathered samples are representative and reflect the variations in composition and quality of the waste material. For example, you may create a circular pile of bagged material with the loading shovel before gathering the sample and consider the following :
- use the ‘points of a compass’ technique by selecting bags from north, south, east, west and then north-east, north-west, south-east and south-west and repeating the process
- use the ‘bagged section approach’ by randomly removing one whole section of the pile from top to bottom, centre to outside edge, without any bias
When sampling baled material choosing a bale at random after production and prior to it entering stock can help randomisation. Additionally, you may also gather materials from different sections of the bale.
The sampling you conduct should illustrate the variation of incoming waste material and specified output materials. Therefore, you will need gather samples of appropriate sizes in one go and not as multiple smaller samples. For example, you may gather one 60kg sample rather than 6 small samples of 10kg to obtain the required 60kg sample size.
Offsite sampling
If you are a small MF without adequate space to conduct sampling, you may undertake offsite sampling. Your sampling methodology for offsite sampling should fulfil all regulatory requirements. You may consider the following while developing an offsite sampling methodology :
- use of an appropriate sample gathering approach to ensure the sample is representative and reflects the variability in input and output material
- use of a sealed or covered container to store sample prior to being taken to the offsite location to prevent cross contamination
- suitable labelling or identification of containers to ensure the correct results are allocated to each supplier
- avoiding long delays between taking a sample and measuring it at an offsite location to prevent material degradation and delays in recording and reporting information within the relevant reporting period
Image 1: Example of sample storage
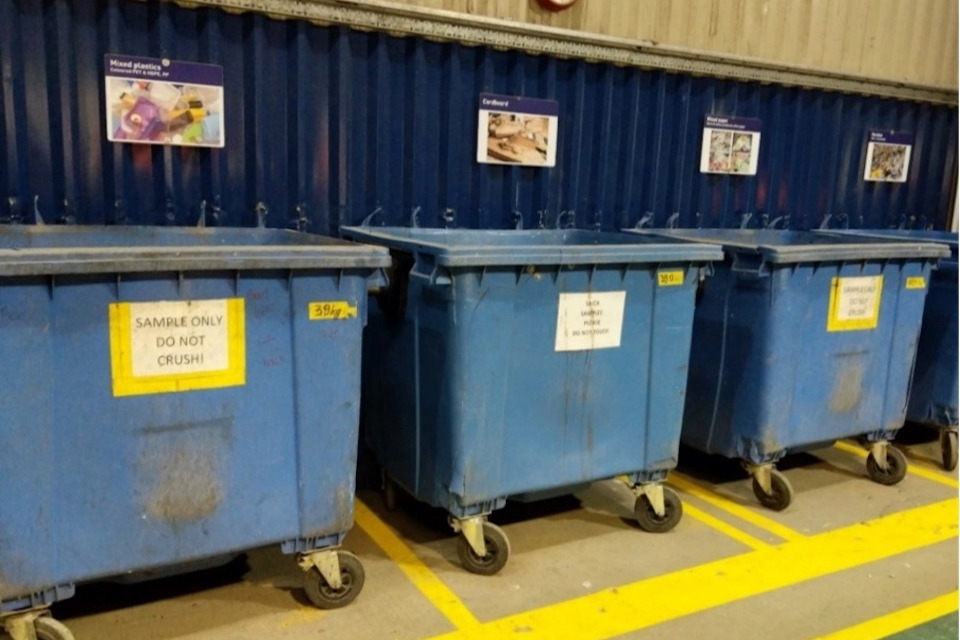
In the image, several samples are stored separately in bins that are appropriately labelled and stored in marked bays. Each bay is demarcated and identifiable using an image above the bay, by the specific waste stream type contained within the sample. For example, the bin containing mixed plastics is stored below an area labelled with an image of mixed plastics.
Labelling samples
You must label the sample with the required information and record the information for reporting to the regulator. This includes :
- date and time the sample was taken
- sample weight
- the details of the supplier the sample was taken from, for input samples
- details of the batch of specified output material the sample was taken from for output samples
Labelling samples securely can help prevent damage during transit or due to inclement weather.
Methods and considerations for measuring samples
You may choose a suitable and appropriate measurement approach based on the operations carried out in your MF. Additionally, you may refer to the following methods and considerations while measuring samples.
Design and preparing the measuring area
Sorting and weighing of materials to be measured should be carried out in a separate undercover area and away from moving equipment and vehicles, including fork lift trucks and loading shovels.
In designating a suitable area for measuring samples, you may consider :
- the use of an undercover area that is protected from vehicle movements and sheltered from the elements
- the use of a suitably spacious area to store samples to prevent any cross contamination with materials from other sources
- keeping the area and containers to be used for sorting clean, dry and free from any materials that might cross-contaminate the sample to be sorted
- the ergonomic design of the sorting area, using tables of optimal working height and adequate number of containers
- having necessary measurement equipment available and ready for use
You can plan and design the area either using custom made sort tables, containers and equipment or those that are already available on the market.
Image 2: sample measuring area
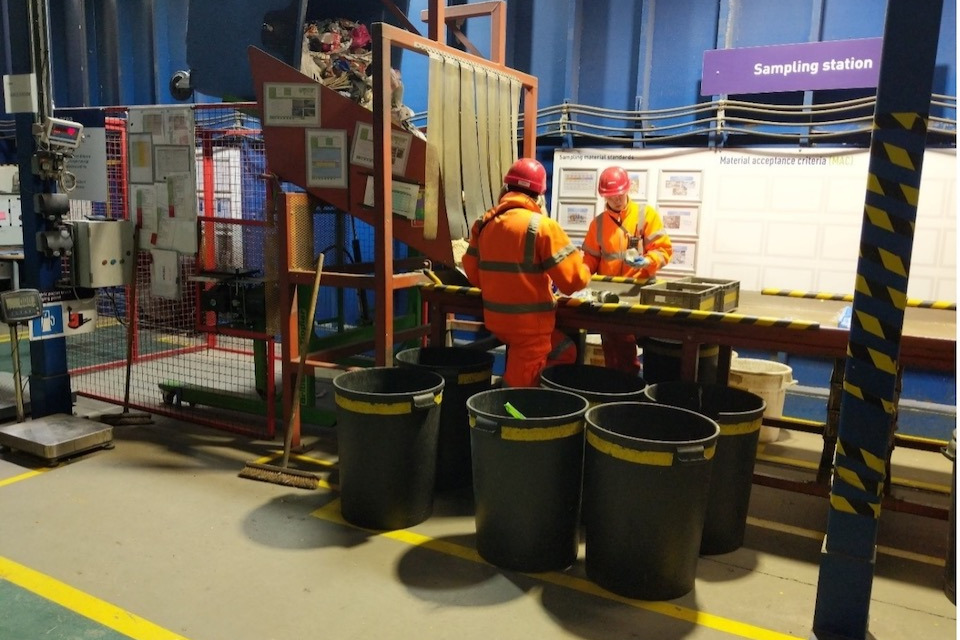
The image above shows the different parts of a sample measuring area within a MF :
- the testing area is clearly marked with a ‘sampling station’ sign
- a caged area contains the sample bin and a bin hoisting mechanism to lift the bin over the adjacent sorting table
- the controls for the hoist mechanism are located outside the cage, thereby allowing the sort operative to control the flow of material on to the sorting table
- a curtain shield is located at the start of the sorting table to prevent excess material falling through at once and helps spread it out
- the table is positioned to allow sorting operatives to stand on either side of the long side
- each operative has several smaller bins around them to enable convenient sorting and separation of material types into their respective bins
Image 3: sorting table layout
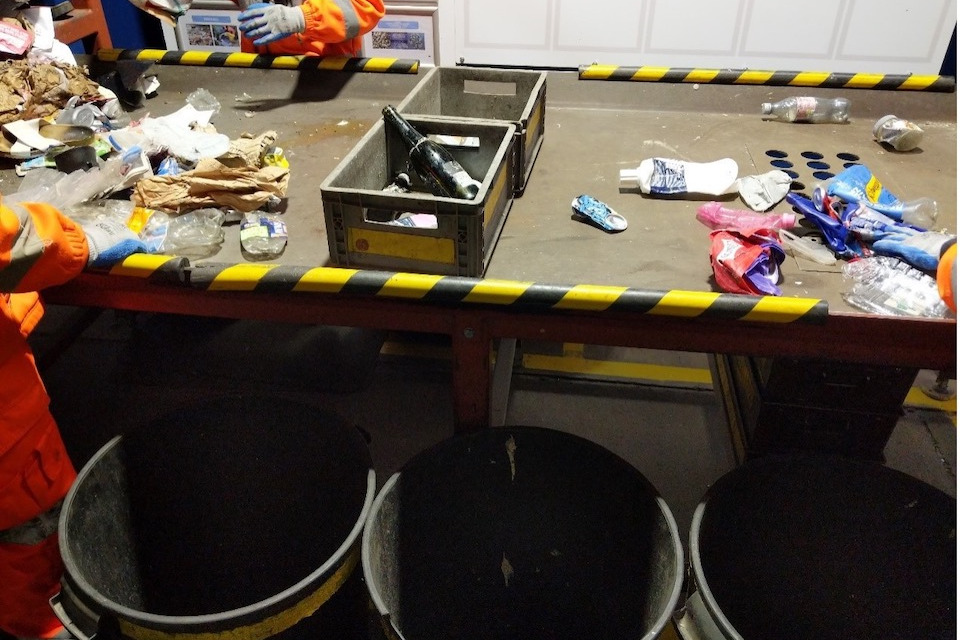
The image above presents an example layout and different components of the sorting table :
- two operatives are standing on either side of the long side of the sorting table
- they both have access to two small boxes placed on the table itself used to separate out items like a glass bottle
- larger bins placed below the table are also visible next to one operative for separating the other various constituents of the sample being measured
- the sort table also has a built in screen for the separation of material particles
Use of appropriate measurement equipment
You may choose to use the appropriate equipment provided in this guidance or any other equivalent equipment based on your individual needs and circumstances.
A non-exhaustive list of typical equipment that you may use can include :
- fork lift truck or hydraulic trolleys for transporting material from the sampling area to the measuring area
- loading shovel or telehandlers mixing samples and loading containers
- platform scales
- bench scales with a calibration certificate and an accuracy of +/- 10g
- 1kg and 5kg weights to check calibration of scales
- electronic tablets connected to the weighing scales to automate record the weights of material being sampled
- containers of different sizes, such as stillages, buckets or other containers for storing, transporting and weighing materials
- pickers to remove hazardous items, such as hypodermic needles
- sharps bins for safely disposing of sharps
- sorting screens with a maximum 55mm and 13mm mesh sizes for sorting material particles
- sorting tables either with built in mesh or trestle legs to support screens
- flat tables for containers and bench scales
- mini sort conveyors to aid the sorting process
- sample sheets to record the outcomes of the testing
While choosing equipment, you should consider tools most appropriate for the task. For example, larger quantities of materials such as 50kg samples may be weighed on platform scales with an accuracy of +/- 500g. In contrast, bench scales with an accuracy of +/- 10g provide greater precision for smaller quantities such as the lighter fractions of specified output material such as film plastics.
Weighing and sorting the sample
You should record all necessary information regarding the sample before commencing. You may consider the following data points :
- the name of the supplier and source, such as the bulking point, if applicable
- grade of material
- delivery vehicle registration
- incoming weighbridge ticket number and the date and time the sample was taken
- details of the person who has taken the sample and who conducts the testing
Prior to sorting you should also weigh and record the sample weight. This will allow:
- adequate checks to ensure that the sample weight meets the requirements of the regulations
- the combined weight of sorted materials to be cross-checked with the original sample weight
While undertaking sorting thereafter, you may consider the following :
- taking care that no material is lost from the sides while tipping the sample onto a sorting table
- the weight of liquids remaining in bottles in the sample as a non-recyclable category
- manual or hand sorting of materials other than material particles into different containers based on the recommended categories
- weighing of each hand sorted category on scales with taring to ensure weight of containers is not recorded
- taring of the scales between each weighing
- use of an ‘other’ category to capture the weight of any material that does not have a specific category
- checking that the combined weight of the different categories recorded for the sample is equal to or within 5% of the original sample weight to avoid any errors
- use of screens with a maximum size steel mesh of 55mm in any one direction for all material particles other than glass
- use of screen with a maximum size steel mesh of 13mm in any one direction for glass material particles
- checking that the weight of material particles categories are weighted to the proportion of material categories of the non-material particle fraction
Image 4: using screens for material particles
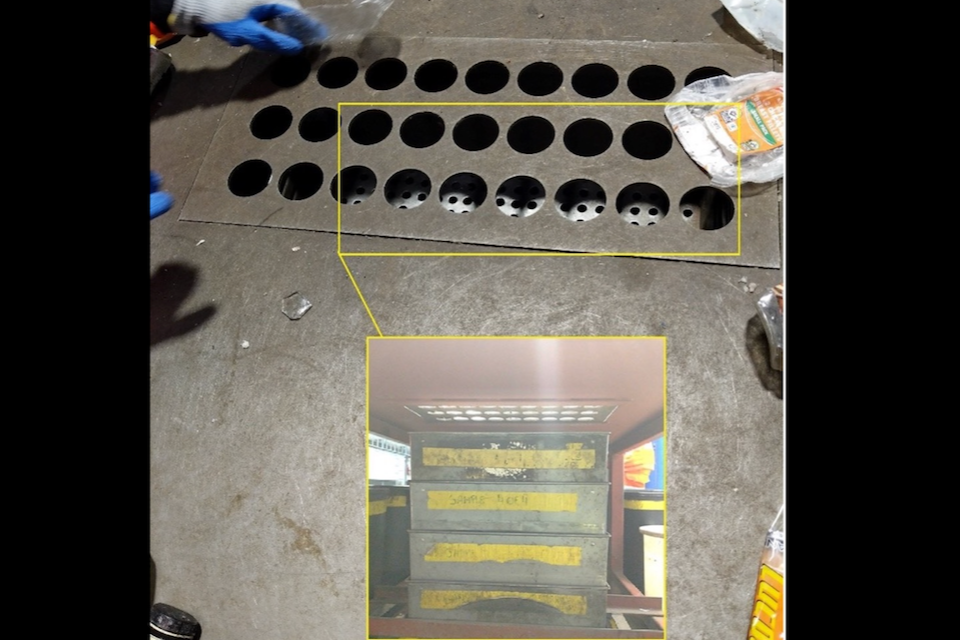
The image above presents an example of a screen built into a sorting table to enable quick and easy separation of material particles. The figures shows that :
- an operative’s hand is visible trying to move material to be sorted over the screen to allow material particles to fall through
- the inset image highlights containers with sequentially smaller screens below the sorting table to allow screening of material particles of decreasing sizes
On completion of measuring, the measuring area should be cleared and made ready for measuring the next sample. Target materials should be placed back in the incoming material bay and the other materials in the residual bay where appropriate.