Locomotive derailment at Doncaster, 21 December 2018
Updated 18 April 2019
1. Important safety messages
This accident highlights the increased risk of derailment for vehicles with newly turned wheels with P1 profiles, operating on curves of around 200 metres radius or less, without a check rail and adequate lubrication. It is important that:
- track curves with a radius of 200 metres or less on passenger carrying lines are fitted with check rails, in accordance with standard NR/L2/TRK/2102;
- track curves with a radius of between 201 and 300 metres are risk assessed in accordance with standard NR/L2/TRK/2102, to determine if they need any specific derailment mitigation measures, taking into account lubrication provision, track usage, deterioration history of the curve, surrounding environment and the likely consequences of any derailment; and
- the railway industry’s own investigation of derailments on running lines should be pursued in a timely manner after an incident/accident, in order to preserve evidence and learn lessons to prevent or minimise recurrence.
2. Summary of the accident
At around 17:17 hrs, a train formed of four locomotives left Roberts Road depot in Doncaster following wheel reprofiling. The train changed direction to travel to York, and while negotiating a tight curve, the third locomotive in the formation derailed at 13 mph (21 km/h).
Nobody was injured during the derailment, but the resultant track damage and recovery operation blocked the line between Sheffield and Doncaster for 36 hours and caused significant disruption to passenger services.
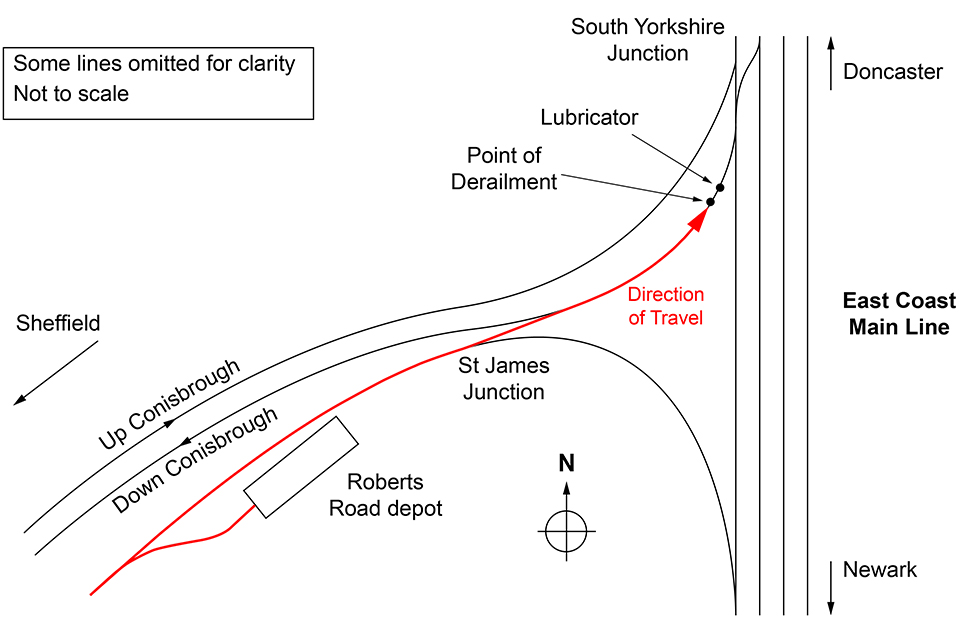
The track layout south of Doncaster station
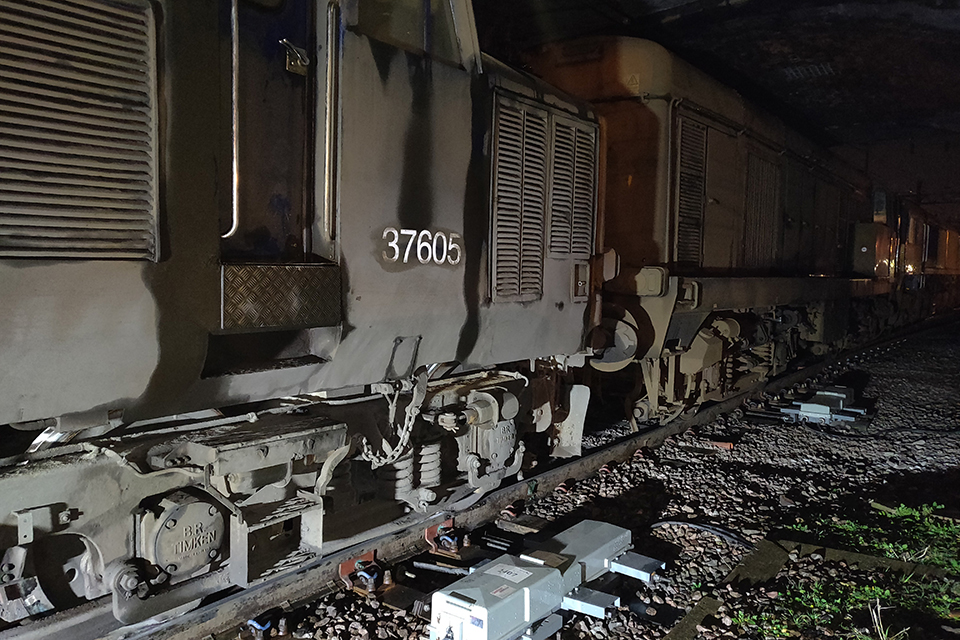
The Class 37 locomotive involved, with the second wheelset of its front bogie derailed
3. Cause of the accident
The train involved consisted of four locomotives, a class 66, a class 20, a class 37 and another class 66 and was operated by Direct Rail Services (DRS). It was travelling from Roberts Road depot to York. After departing from the depot, it changed direction and headed towards Doncaster station via St James Junction. The train traversed a curve on the Down Conisbrough line, a signalled move in the opposite direction to normal passenger trains.
As the train negotiated the curve, the first two right-hand wheels of the leading bogie of the class 37 locomotive climbed the outside rail of the curve and derailed to the outside of the curve. The third wheelset on the leading bogie stayed on the rails until the bogie reached the crossing of a set of trailing points, at which point it also derailed.
The driver of the train reported feeling a jolt and hearing a loud bang. He looked out of his window, saw sparks from the class 37’s front bogie and immediately applied the brakes. As the train came to rest with the class 37’s leading bogie over a set of trailing points, the first wheelset of the leading bogie rerailed and the second and third wheelsets became trapped between the switch and stock rails. The points were damaged and required a half set of switches, numerous sleepers and other components to be replaced. There is no evidence that the actions or driving style of the driver contributed to this accident.
Derailments of this type, where the flange of a wheel climbs the outer rail of a curve, are complex and dependent on a number of factors. These include the lateral and vertical forces applied where the wheel flange contacts the rail, the flange contact angle (which depends on both the flange angle of the wheel and the profile of the rail), the level of friction between the wheel and rail and the presence or absence of a check rail. An adverse combination of some or all of these factors can lead to a derailment, and such a combination is likely to have been the cause of this derailment.
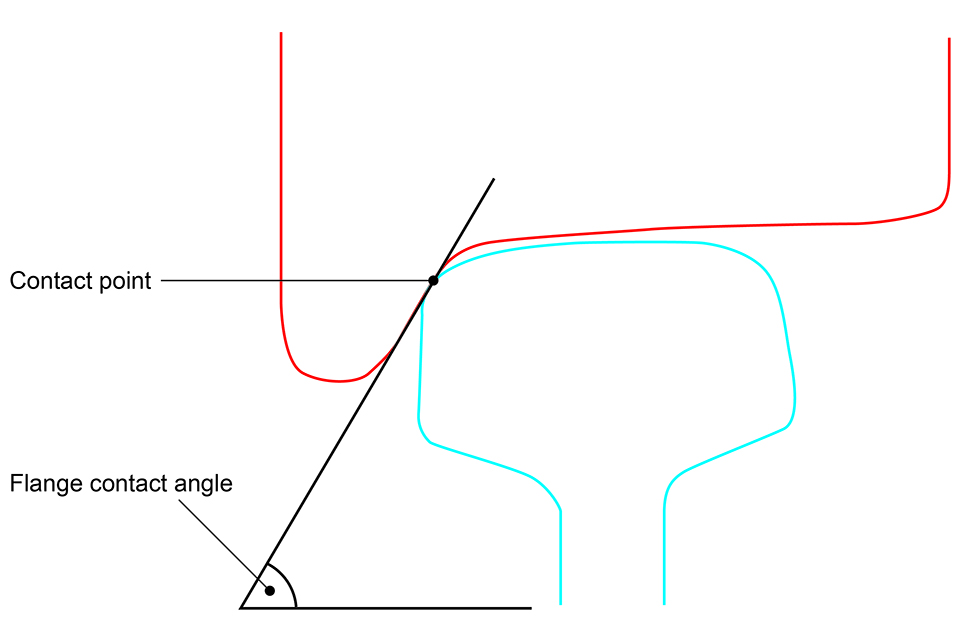
Representation of the flange contact angle as a wheel begins to climb the rail
Prior to the journey, the wheels of all the locomotives in the train had been reprofiled on a wheel lathe at Roberts Road depot. This process removes material from worn or damaged wheels in order to restore the shape of the wheel to the design profile. The class 66 locomotive wheels were restored to a P8 profile, while the class 20 and class 37 locomotives were restored to a P1 profile. Records provided to the RAIB, supplemented by measurements of the wheel profiles, show that the lathe was functioning correctly and turned the wheels within the correct geometric and surface finish tolerances.
As part of the investigation into a derailment at Ordsall Lane (RAIB report 07/2014), the RAIB commissioned a review of published literature concerning the wheel surface finish and wheel-rail contact friction following wheel reprofiling. This found that the relationship is complex and there is contradictory evidence as to whether a rougher surface finish may necessarily result in a higher level of wheel-rail contact friction.
A consequence of the wheel reprofiling is that the wheels would have been clean and dry at the time of the derailment, increasing the friction between the wheel and the rail and hence the likelihood of derailment.
The P1 wheel profile used on the class 37 locomotive is common across many older rail vehicles in the UK and has a designed flange angle of 62°. More modern wheel profiles (such as the P8 found on the class 66 locomotives) are designed with flange angles of between 68° and 70°. The shallower flange angle of a P1 profile increases the risk of derailment compared to a P8 profile, and as a result the P1 profile has less resistance to climbing the rail. As a P1 profile wears, the flange angle increases and hence the derailment risk decreases.
The bogies of the class 37 locomotive each have three wheelsets, which increases the overall wheelbase compared to a two-axle bogie, and this is likely to have adversely affected the ability of the bogie to corner.
Two weeks after the derailment, the RAIB and DRS undertook a visual inspection of the locomotive over an inspection pit at Roberts Road depot. No significant issues were observed. However the visual inspection was limited in scope and a more detailed inspection would be required to determine whether any other vehicle factors may have contributed to the derailment, such as excessive resistance to bogie rotation. At the time of writing, DRS had not arranged for the locomotive body to be lifted off the bogies to allow further investigation, and the locomotive remains out of service.
Rail-mounted lubricators are installed across the network to reduce the friction between the wheel and rail, primarily to manage rail wear, but also to reduce curving noise. Reduced friction also lowers the risk of derailment. Although the curve had a functional lubricator installed, it was located at the far end of the curve and because the train was travelling in the opposite direction to normal train movements, it did not pass over the lubricator. Any lubrication encountered by the train wheels would have been the residual grease left on the rail by other trains travelling in the opposite (normal) direction.
The track on the curve where the derailment occurred was within the allowable geometric tolerances. Surveys undertaken by the RAIB and Network Rail show that the gauge measured up to 1455 mm, 20 mm wider than the nominal figure. This reading had just reached the alert limit for the line speed of this curve (25 mph (40 km/h)), where Network Rail is required to plan maintenance, but not make any immediate intervention. However, even moderately wide gauge such as this increases the angle of attack (ie angle of the wheel relative to the rail when viewed from above) of wheels as they traverse the curve, which in turn increases the risk of derailment.
The track surveys also showed that the cant (the difference between the elevation of the two rails) and the twist (the difference in cant over a fixed distance; usually 3m) were within acceptable tolerances. The twist found in one isolated area around the point of derailment was approaching the point where Network Rail would be required to plan maintenance, but was not severe enough to require immediate action.
Network Rail’s records indicate that the curve has a radius of 207 metres, and was installed in 1999 during the upgrade of the route between Sheffield and Doncaster. The Network Rail track engineer responsible for the maintenance of that section of track reports that the rails were changed in 2010 or 2011. The RAIB undertook a survey and found portions of the curve which measured below 200 metres radius. Railway Group standard GCRT5021 and Network Rail company standard NR/L2/TRK/2012 both mandate that curves of 200 metres radius or less on passenger carrying lines, and track nine metres either side of such curves, should be fitted with a check rail. A check rail prevents the build-up of lateral forces on the outside rail, so the absence of one was potentially a factor in this derailment.
Standard NR/L2/TRK/2102 also states that a check rail should be considered on curves between 201 and 300 metres radius. The standard states that the assessment of these curves should include consideration of the lubrication provision, usage of the track, deterioration history of the curve, surrounding environment and the likely consequences of any derailment. The RAIB found no evidence to indicate that such assessments had been undertaken for this curve. Had such an assessment been carried out it should have identified that the curve being traversed by legacy locomotives with 3-axle bogies and older wheel profiles, the proximity to a wheel lathe, and the lack of lubrication for wrong direction moves, were all potential risk factors.
Rail cross-sectional profiles were taken by the RAIB on the day following the derailment. Sidewear measurements were taken by Network Rail on the night of the accident. These measurements both show a moderate level of sidewear, but within allowable tolerances. A visual inspection of the outside rail of the curve showed evidence of metal particles on the sleepers and rail fastenings, consistent with sidewear and evidence of a relatively high level of friction between the rail and contact with wheel flanges.
Railway duty holders, such as Network Rail and DRS, are required by The Railways and Other Guided Transport Systems (Safety) Regulations 2006 (ROGS) to have a compliant Safety Management System. Basic elements of any Safety Management System include procedures for the reporting, investigation and analysis of accidents and incidents. This is further supported by RIS-3119-TOM, the Railway Industry Standard for Accident and Incident Investigation. In most cases, the industry will undertake a joint investigation, regardless of any involvement of the RAIB.
Following the derailment, detailed inspection and measurements of the track were undertaken by Network Rail. However, no higher level industry investigation was commenced until almost two months later, by which time it is possible that other vulnerable or perishable evidence may have been compromised.
4. Previous similar occurrences
RAIB report 07/2014 describes a similar derailment at Ordsall Lane Junction, Salford, where a class 47 locomotive climbed the rail in similar circumstances. The locomotive was of a similar three-axle bogie configuration, and its wheels had just been machined to a P1 profile. The track curvature at the point of derailment was around 200 metres. The curve had no effective lubrication. Standards required the curve to have a check rail, but this was not fitted. The RAIB made three recommendations to Network Rail relating to the management of friction on small radius curves and compliance with design standards, which the safety authority (Office of Rail and Road) have stated are currently in the process of being implemented.