Track worker struck by a road-rail vehicle at Braybrooke, 6 February 2024
Published 29 May 2024
1. Important safety messages
This accident demonstrates the importance of:
- staff controlling on-track plant maintaining a position that affords a good view of the area ahead of the machine
- staff working around on-track plant ensuring that they keep an awareness of machine movements
- maintaining and controlling exclusion zones around on-track plant.
2. Summary of the accident
During the early hours of 6 February 2024, a track worker was struck and injured by a road-rail vehicle (RRV) while working in a possession on the Midland Main Line near to Braybrooke in Northamptonshire.
The track worker was walking along the track and directing the movement of another RRV on an adjacent line when they were struck. As a result of the accident, the track worker sustained a leg injury which required hospital treatment.
3. Cause of the accident
The accident occurred because the person responsible for directing the movements of the RRV involved (the machine controller) had not seen the track worker walking along the track ahead when they instructed the machine operator to move the machine. The machine operator had a restricted view of the track ahead from their control position.
The work being undertaken was the installation of new overhead line equipment as part of the Midland Main Line electrification project. Staff were deployed in RRVs which included a pair of machines working on each of the two parallel tracks. A supervisor was overseeing the work, and another person was appointed to co-ordinate the use of the RRVs.
It was dark at the time of the accident and work was being undertaken using the lights of the machines involved and head torches worn by the staff involved. The area is a rural location and there is no nearby lighting on or adjacent to the railway.
The RRV involved in the accident was a mobile elevating work platform (MEWP). This comprises a basket attached to a boom which can be raised or lowered to enable access to the overhead line. The machine operator stands in the basket when operating the controls to move the RRV along the track or to work when it is stationary. The RRV can be configured so the basket is either leading or trailing the main body of the machine as it moves along the railway. The machine which struck the track worker is referred to as ‘RRV1’.
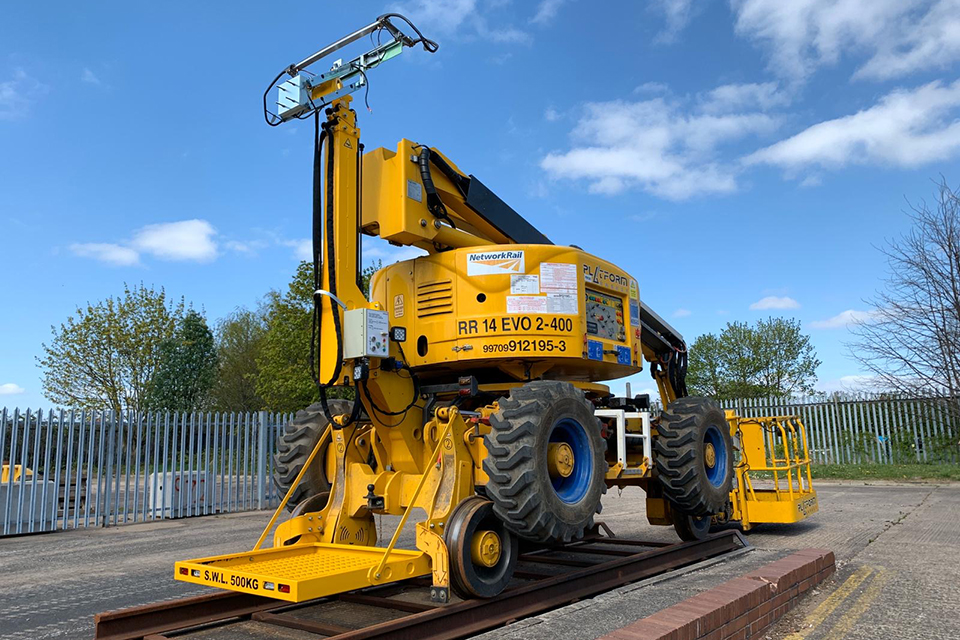
An RRV of the same type as the machine involved in the accident, with deployed carry deck nearest the photographer and operator’s basket at the opposite (‘trailing’) end. (Courtesy of SPL Powerlines UK Ltd.)
When driving the RRV with the basket in the trailing position, the machine operator, situated in the basket, has a restricted view of the track ahead. This is because the boom and body of the machine obscure their view. When a machine operator’s view ahead is restricted, it is a requirement of the Rule Book (GERT 8000 Handbook 15 ‘Duties of the machine controller (MC) and on-track plant operator’, Issue 6 September 2022) that the movement is controlled by a machine controller on the ground. It is also a specific requirement for this type of RRV that any movements made with the basket trailing be controlled by staff on the ground.
RRV1 and the three other RRVs nearby at the time of the accident each had their own dedicated machine controller and machine operator.
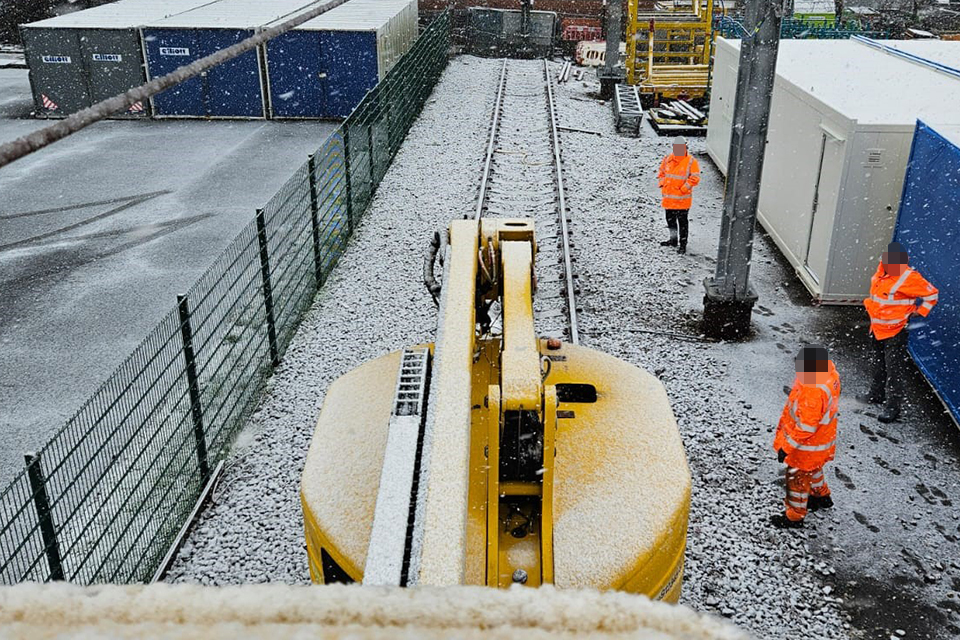
View from the raised operator’s basket showing the restricted view of the track immediately ahead of the machine. (Courtesy of SPL Powerlines UK Ltd.)
An additional feature of RRV1 is a carry deck that can be used to move tools and equipment. At the time of the accident the carry deck was at the leading end of the machine. Although not carrying any equipment at the time of the accident, it was in its horizontal position, as it is automatically lowered when the RRV’s rail axles are deployed. The top of the carry deck when in the lowered position is approximately 33 cm above rail height.
The work was planned so each line had a pair of RRVs working ‘back-to-back’ with the MEWP baskets facing each other. Two of the machines, including RRV1, were to work on the Down Main line. Another RRV (referred to as ‘RRV2’) and a fourth machine were to work together on the Up Main line. This method was planned and briefed to the staff operating and controlling the machines before work began.
To reduce the danger from on-track plant such as RRVs, Network Rail requires an exclusion zone to be set up around them. These zones are intended to prevent staff from walking into blind spots where machine operators cannot see them. Staff are not permitted to enter an exclusion zone without the permission of the machine controller for the RRV concerned, who will confirm it is safe to do so. The extent of an exclusion zone depends on the type of machine and the activity being undertaken.
The task brief for the work being carried out included a requirement to set up and maintain exclusion zones around the machines. The exclusion zones were shown graphically and extended 10 metres to the front and rear of each single MEWP. The task brief states that the exclusion zone is to be set up and managed by the machine controller.
After pre-use checks, all four machines were put onto the track shortly after midnight at an access point located to the south-east of the site of work. The four machines then travelled approximately 2.4 km (1.5 miles) north-west to the site of work. After a period of work, they were withdrawn a short distance and stood down to allow another team to survey the overhead line.
Witness accounts differ about the distance between the site of work and the position to which the machines were withdrawn to allow the survey to take place. One witness reported the distance to be around 30 metres while another suggested it was in the region of 100 metres.
The railway in this area has refuges located between the Down Main line and the boundary fence, an area referred to as the ‘Down cess’. With the machines stood down, the machine controller for RRV2 (machine controller 2) took a break, standing alone in a nearby refuge in the Down cess. The machine controller for RRV1 (machine controller 1) remained on the track and in the vicinity of RRV1.
Once the survey work was complete, the supervisor instructed the machine controllers and machine operators to return their respective machines to the site of work.
Witness evidence indicates that machine controller 1 walked from a position between the two tracks (the ‘six-foot’) around the rear of RRV1 to the Down cess side to check that the way ahead was clear. During this check, machine controller 1 saw that machine controller 2 was in a refuge in the Down cess. Machine controller 1 then returned to the six-foot via the rear of their machine, retracing their steps. Satisfied that the way ahead for RRV1 was clear, machine controller 1 gave the machine operator of RRV1 the instruction to move. The machine operator (machine operator 1) raised RRV1’s basket and sounded the horn, as was their standard practice when about to move their machine. They also checked the area ahead of their machine as best they could, given the restricted view from the basket. Machine operator 1 then commanded RRV1 to move forward.
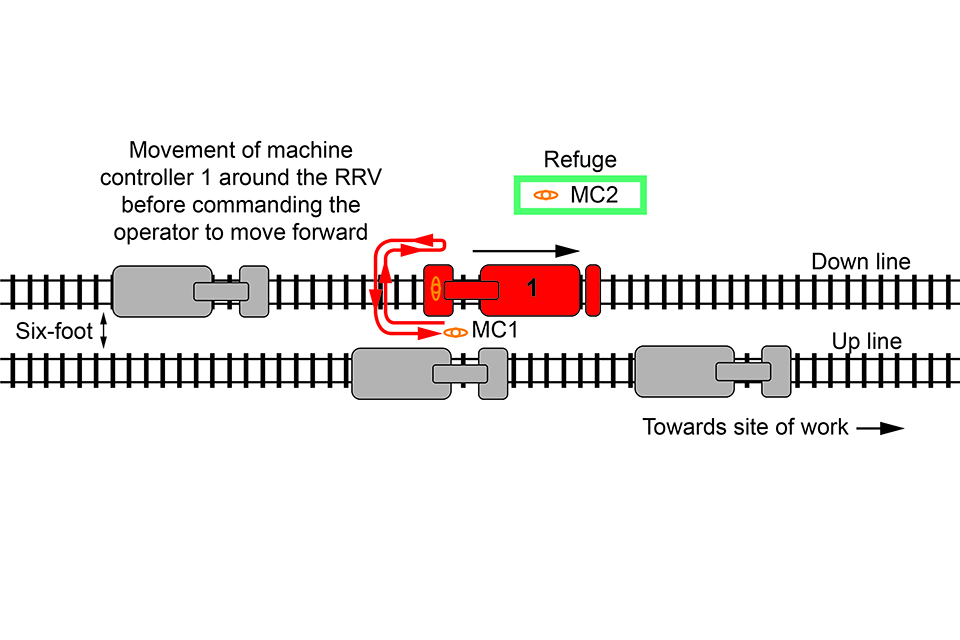
The route (red arrow) of machine controller 1 around RRV1 when checking around the RRV.
Sometime after machine controller 1 had checked the cess side of their machine, machine controller 2 left the refuge and walked towards RRV2, which was on the Up Main line. Machine controller 2 took a position in between the rails of the Down Main line (the ‘four-foot’) and started to walk ahead of RRV1, with their back to it.
Immediately before the accident, the operator of one of the RRVs on the Up Main line saw machine controller 2 walking in the four-foot of the Down Main line. They realised that RRV1 was about to strike machine controller 2, so they shouted a warning. This was heard by machine operator 1, who responded by stopping RRV1. Machine controller 2 tried to move out of the way of RRV1, towards the six-foot. However, they reported being struck on the back of one of their legs by the carry deck of RRV1 as they did so, and they fell to the ground in the six-foot. Only after RRV1 had stopped did machine operator 1 see machine controller 2 lying on the ballast and realise why a warning had been shouted.

Approximate positions of the four RRVs and the position of machine controller 1 and machine controller 2 immediately before the accident.
Machine controller 2 stated that they sustained their injury from a combination of being struck and by subsequently falling while moving out of the way of the machine. They were given assistance by colleagues and subsequently taken to a nearby hospital.
This accident occurred because machine controller 2 was walking in the area directly ahead of RRV1 and because the movement of the machine brought them within its exclusion zone and then into contact with the carry deck. The area directly ahead of RRV1 was outside the vision of machine operator 1, who had a restricted view of the line ahead, and also of machine controller 1, who was to the rear of the machine. Although machine controller 1 had checked the line ahead before authorising RRV1 to move, machine controller 2 had in the intervening period left the refuge and walked ahead of the machine.
Network Rail has a series of lifesaving rules which it requires staff and contractors to comply with. This includes the rule ‘Never enter the agreed exclusion zone, unless directed to do so by the person in charge’.
4. Previous similar occurrences
Several accidents involving RRVs where restricted visibility was a factor have previously been investigated by RAIB. Some of these accidents have resulted in serious injuries.
Events with similarities to the accident at Braybrooke include:
- RAIB undertook an investigation into an accident near Cholmondeston in Cheshire which occurred in September 2018 where a ballast distributor that was travelling in reverse collided with a small personnel carrying vehicle (RAIB report 08/2019). Two track workers in the rear of the personnel carrier were injured, with one of them suffering life-changing injuries. The collision occurred because there was very limited visibility of the line ahead when the ballast distributor was being driven in reverse, and because no one was controlling its movements from the ground.
- RAIB undertook an investigation into an accident that occurred in January 2020 near Rochford in Essex, when two MEWPs collided injuring two people (RAIB report 08/2020). In this case, the machine operator had driven away from the machine controller while using the on-board CCTV screen to view the route ahead. These actions were contrary to the applicable operating rules.
- RAIB also investigated a collision between two RRVs in May 2021 near Ramsden Bellhouse in Essex, where a stationary MEWP was hit from behind at around 7.5 mph (12 km/h) by a road-rail machine, configured as a crane (RAIB report 09/2022). The MEWP operator suffered life-changing injuries due to the collision. The operator of the crane had become dazzled by the rising sun ahead and had turned to look out of the side window to relieve their eyes. They did not apply the brakes of the crane when they did so, resulting in the collision.
A wider summary of previous RAIB learning, including more similar incidents relating to RRVs, can be found on RAIB’s website https://www.gov.uk/government/publications/summary-of-learning-6-safe-design-operation-and-maintenance-of-on-track-plant-and-trolleys.