Track workers struck by ballast thrown from the track bed by a passing train near Chathill, Northumberland, 16 February 2017
Published 8 May 2017
1. Important safety messages
For those involved in the design and safety assessment of equipment to be fitted to trains, this incident serves as a reminder of:
- the need to consider all foreseeable loads and hazards, and that the analysis carried out should not be unduly constrained by existing processes and checklists
- the importance of fully considering the impact of hazards on nearby people and systems
2. Summary of the incident
At around 10:10 hrs on 16 February 2017, two track workers were struck by flying ballast thrown up by a passing train travelling at 98 mph (157 km/h). One end of a flexible hose had become detached from the train and was dragging along the track. Neither track worker suffered significant injury.
The train, 1V56, was the 07:50 hrs CrossCountry Trains passenger service from Glasgow Central to Plymouth, a 4-car class 220 diesel-electric multiple unit. The train driver was unaware of the incident until debris thrown up by the dragging hose damaged equipment underneath the train causing an alarm to be triggered. The train came to a stand 3.5 miles (5.6 km) beyond the track workers. Network Rail found damage to an anti-trespass guard at Newham level crossing, 0.6 km after the train had passed the track workers at Chathill.
The track workers were part of a group of seven Network Rail staff who were inspecting the overhead wires above the tracks. They were all standing in a position of safety on the left-hand side of the line with respect to the direction of travel of the train.
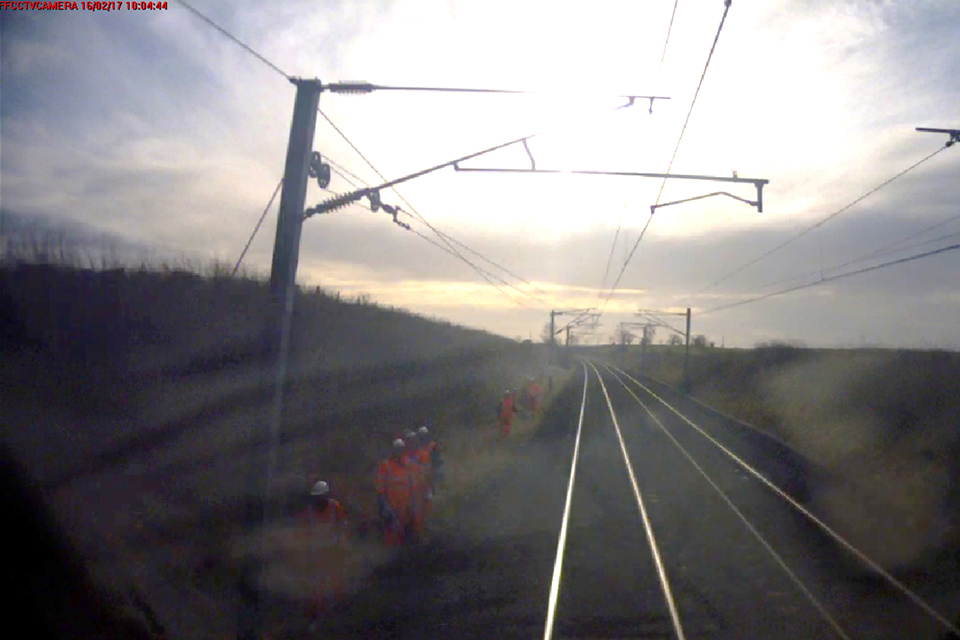
View of the group of track workers from the forward facing CCTV on the train (photo courtesy of CrossCountry Trains)
3. Cause of the incident
The hose which partially detached from the train was part of a new sanding system that had been fitted on 6 February 2017 (below), in response to recommendation 1 of the RAIB report into a buffer stop collision at Chester station on 20 November 2013 (RAIB report 26/2014). Sand hoppers had been mounted on the underframe of the two end vehicles of CrossCountry Trains class 220 and 221 units, with flexible hoses running from each hopper to brackets attached to the inner bogie to deliver sand to both rails in front of the third axle (from the driving end). Each hose was supported by a lanyard fitted under the vehicle body.
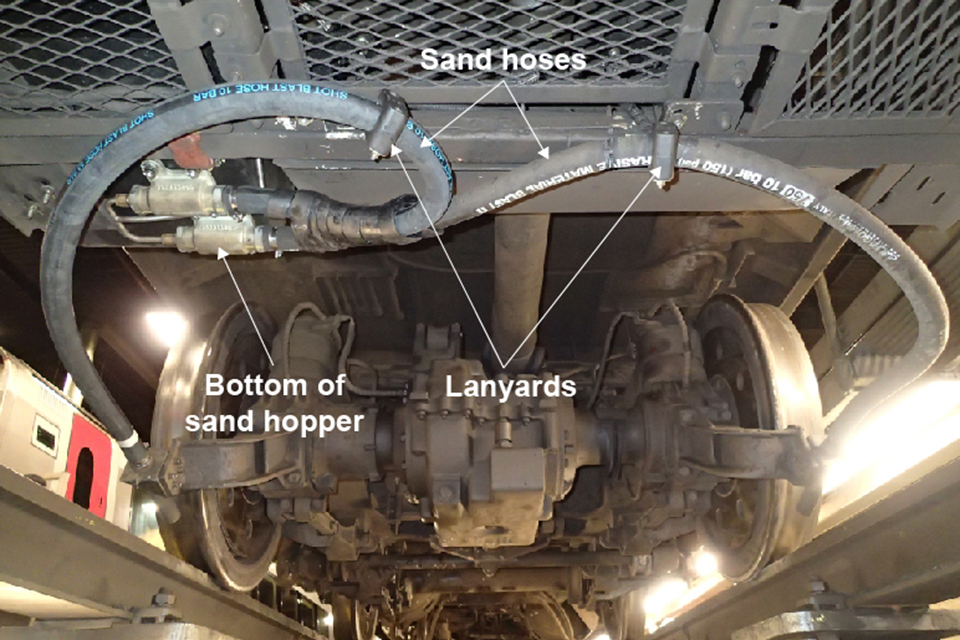
Underside of class 220 vehicle showing the location of the sanding equipment
The cause of the detachment was not determined with certainty. However, the RAIB considered evidence from this and other similar failures (see later). Those identified by drivers all appeared to have occurred on high speed sections of lines. The RAIB concludes it was most likely that the section of hose between the lanyard and the bogie mount deflected downwards and snagged on track infrastructure features; such as check rails or anti trespass guards at level crossings. The deflection is considered likely to be the result of aerodynamic loads, possibly in combination with other dynamic loads; the hose is orientated across the width of the train’s underframe (above) where there is considerable longitudinal air flow when the train is travelling at speed.
CrossCountry Trains specified the requirements for the sanding system modification to Bombardier Transportation UK Ltd, who was responsible for the maintenance of the units. Bombardier contracted AB Hoses Ltd to design and manufacture the sanding system modification. AB Hoses designed the system during 2016 and submitted its design to Bombardier who managed the approvals process with support from others. Approval was given in September 2016. Small scale fitment of the modification started in October 2016, which ramped up to about 5 units per week from mid-January 2017. At the time of the incident, just over half of the fleet had been modified.
In accordance with European Union Regulation 402/2013, Bombardier applied the criteria in the common safety method for risk evaluation and assessment (CSM RA) to assess whether the modification could have a significant impact on safety. This assessment indicated that it could, and therefore Bombardier adopted the risk management process described in the CSM RA to identify the associated risks and manage them to an acceptable level.
A key element of the risk management process is the identification of hazards which might arise from the proposed change. AB Hoses conducted a Failure Modes and Effects Analysis (FMEA) of its design for the sanding system – an approach suggested in the Office of Rail and Road’s guidance on the application of the CSM RA to the GB mainline railway system. The CSM RA allows for each risk associated with the identified hazards to be demonstrated to be acceptable against one of three principles; application of codes of practice; comparison with similar systems; and explicit risk estimation.
Although the FMEA identified that both failure of the mounting arrangement and the hose itself would cause the hose to become detached or misaligned, the only effect identified was its impact on the sanding system (ie sand might not reach the rail). It did not identify the possible effects on other systems or personnel if the hose was dragged along the track. The design load cases for the system did not consider any effects of aerodynamic loads on the hose when the train was travelling at high speed.
The AB Hoses FMEA was submitted to Bombardier who reviewed it and incorporated it into its own risk management process. The Bombardier process also included hazard identification guided by a checklist. One of the off-vehicle hazards listed on the Bombardier checklist was equipment detaching from vehicles due to failure of fixings to the new underframe hardware causing a missile resulting in injury/fatality/property damage. This hazard was closed out by demonstrating compliance with the requirements of Railway Group Standard GM/RT2100 ‘Requirements for Rail Vehicle Structures’ issue 5 June 2012. However, this standard (considered a ‘code of practice’ in the CSM RA) does not explicitly require consideration of aerodynamic loads, although it does require locally generated acceleration forces and resonances acting on equipment to be accounted for. The effect of aerodynamic loads on the hose could have been considered to have been included in this. However, in this case, they were not, because the effects of the flexible characteristics of the hose in the location in which it was to be installed had not been formally recognised. The Bombardier checklist also identified, under the gauge infringement risks, the hazard of equipment partly detaching from the vehicle. However, this hazard was not considered to be applicable to this modification. The use of checklists is promoted in RSSB’s guidance on the application of the CSM RA and in CENELEC Technical report CLC/TR 50126-2 ‘Railway Applications – The specification and demonstration of Reliability, Availability, Maintainability and Safety (RAMS) – Part 2: Guide to the application of EN 50126-1 for safety’. However, the guidance is careful to highlight that ‘No checklist can be exhaustive and the analyst should bring his or her full experience to bear in searching for hazards’.
Again in accordance with the CSM RA, Bombardier appointed Aegis Engineering to undertake an independent assessment of the suitability of both the application of the risk management process and its results. Aegis Engineering reviewed Bombardier’s risk management process for the new sanding system, in terms of the robustness of the hazard identification process and the competency of the rolling stock engineers, and concluded that it ‘… is satisfied that the modification includes a risk assessment that meets the requirements of the CSM-RA Risk Management Process and that the output of the risk assessment is sufficient for the engineering change’. The independent assessment carried out by Aegis Engineering did not identify that the full consequences of hazards relating to hoses becoming detached had not been recognised in the AB Hoses FMEA, or that the effects of aerodynamic loads had not been taken into account.
4. Previous similar incidents
Since the introduction of the new sanding system at least 16 sand hoses have detached from CrossCountry Trains class 220 (14) and 221 (2) units. Half of these were identified by drivers in service and half by maintenance staff at Bombardier’s maintenance depot. Bombardier instigated fleet checks on all class 220 and 221 units fitted with the modification and has implemented a temporary solution to all these trains ahead of a permanent solution becoming available. Bombardier reported that the temporary solution has been effective in preventing further incidents.
A control cabin became detached from an engineering train at Blatchbridge Junction in Somerset on 19 March 2012 when the bolts securing it failed. The RAIB investigated this incident (RAIB report 15/2013) and identified one of the underlying causes as being that the design review process did not consider the loads on the cabin securing bolts when the machine was in its working mode.
You can print this safety digest.