Innovative manufacturers get government skills boost
5 organisations have been chosen to test new ways to develop skills for innovation in manufacturing.
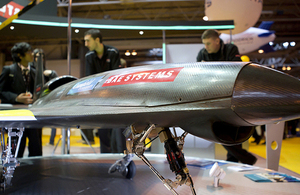
BAE Systems' exhibit at BIS Big Bang Fair 2012. Photo credit: Department of Business Innovation and Skills / flickr.com. Used under Creative Commons 2.0 (CC BY-ND 2.0).
The UK Commission for Employment and Skills (UKCES) has chosen five organisations to test new ways to develop skills for innovation in manufacturing. Each will run a trial programme expected to yield valuable learning that can be shared across the sector to improve innovation and productivity.
The successful organisations include a leading UK manufacturer, an employer representative body and UK universities. Projects are based in Belfast, Cardiff, Glasgow, Swansea and Lancaster. Each will test skills development in their workplaces as part of the UK Futures Programme, a series of learning programmes aiming to address specific workplace skills needs. Each project will receive co-investment from UKCES up to £150,000.
UKCES Commissioner and leader of the competition Paul McKelvie OBE said:
“I’m delighted to announce the successful applicants of our Skills for Innovation in Manufacturing competition. My team and I were impressed with the fresh thinking on display in these five projects, and we are excited to see what we can learn from their achievements.”
UK manufacturing is identified as highly productive and a key sector for exports, and this competition seeks to explore new ways of developing skills and practices needed to maximise the value of innovation.
McKelvie added:
“Innovation is vital for our national prosperity. It has a critical role in productivity and job creation, and nowhere is this true more than the manufacturing sector. It’s vital that that we learn how manufacturing firms can optimise their workplaces and processes to take best advantage of their high-skilled, highly productive workers.
“We will watch and learn carefully over the coming months, and we look forward to sharing the learning from these five projects to the manufacturing sector as a whole.”
The UK Futures Programme is a series of learning programmes that target specific emerging or persistent workforce development problems. This round invited employer-led proposals from businesses and other organisations in the manufacturing sector to run initiatives until summer 2016 that focus on skills to manage the innovation process and exploit innovative products or services for commercial value.
About the five projects
BAE Systems Maritime Naval Ships
BAE Systems Maritime Naval Ships is piloting a new way of incentivising innovation and enhancing discretionary effort through the introduction of schedule-based working (SBW) into a complex manufacturing facility in Glasgow. SBW, which was developed in conjunction with the Trade Unions, empowers people to work more efficiently and innovatively by rewarding teams for their level of output, rather than for their attendance. This project builds on previous small-scale pilots and seeks to understand the impact of introducing these innovative working arrangements into a complex manufacturing environment as well as how to encourage greater engagement and productivity from employees. IPA Involve are partnering with BAE Systems to develop this initiative.
Swansea University
Building on its successful leadership programme for SMEs, LEAD Wales - which closed in June 2015 - Swansea University is developing a programme which focuses on increasing the innovation management skills and knowledge of leaders and senior managers, to help them develop the innovation culture of their organisations. Supported by Industry Wales and the EEF, the project will help manufacturing firms in Wales understand the challenges of encouraging and exploiting innovation for commercial ends. It will also provide a model to help them develop their commercialisation skills and knowledge and practices around the incentivisation of innovation. A key way this will be achieved is via experiential learning – participants will learn through first-hand experience.
Cardiff Metropolitan University
This project led by the International Centre for Design and Research (PDR) and Cardiff School of Management (CSM), based at Cardiff Metropolitan University, is supporting the creation of a new innovation-focused supply chain.
The four-tier, healthcare supply chain: Prism Medical UK, EBS Automation, RTLS, and ABM University Health Board’s Rehabilitation Engineering Unit, will work together to pilot a ‘Unified Innovation Model’ approach to new product development - where the insights of designers, manufacturers and end users are brought together and shared throughout the entire process of developing the novel products targeted at the high-value UK medical device marketplace. This should ensure the co-creation of relevant novel products and develop organisational learning cultures that mutually support innovation.
BAE Systems (Operations) Ltd
BAE Systems (Operations) Ltd, in conjunction with Lancaster University, is building on the university’s flagship leadership and management programme, LEAD, to focus on developing the innovation capacity of SME owner-managers, in the Advanced Engineering and Manufacturing sector, in the North West of England. The initiative will develop strategic thinking, innovation capacity and leadership and management skills through masterclasses, workshops, innovation challenges, action learning groups, as well as supporting access to regional and national innovation infrastructure, such as the Advanced Engineering & Manufacturing Technology Exploitation Centre (AEM-TEC) at Samlesbury/Warton, Lancashire. The project should improve SMEs’ capacity for innovation as well as explore how to encourage SMEs to gain a better understanding of, and ability to exploit, market opportunities.
Northern Ireland Polymers Association (NIPA)
The Northern Ireland Polymers Association (NIPA), in conjunction with CITB Northern Ireland, is collaborating to develop innovation skills between the polymers and construction industries in Northern Ireland. Both industries have complementary skillsets and have identified learning from each other’s strengths and weaknesses, something which has not been attempted before. 24 employers, of all sizes, from both industries, will be brought together to define innovation issues and the interventions required in ‘petri-dish’ working groups. These will ‘drip feed’ information between each other to develop solutions before all participants test and share their findings. The project will provide insight into how two compatible, yet distinct sectors, can collaborate and whether the resulting innovation process could be deployed to other sectors.