Tech stopping the inspection blues
How do we make sure the complex equipment being fabricated by our suppliers is up to the right standards during a lockdown?
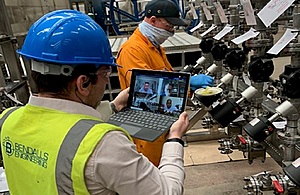
The Box Encapsulation Plant project team carrying out inspections using Microsoft Teams
It’s questions like this that may not have been the first things we thought of as a potential problem when the crisis hit, but they still need sorting.
For our Box Encapsulation Plant (BEP) project team it has meant the successful innovative use of the kind of technology that’s becoming the norm across our business for keeping in touch.
Microsoft Teams wasn’t even on our radar a couple of months ago, but the team are now using it to successfully conduct highly complex inspections on stainless steel equipment, miles away.
Deputy Project Manager for BEP Mike Critchley said:
During this ongoing lockdown period, a projects task team have been working with the Inspection and Quality Assurance Department to look at ways we could help the supply chain to continue work.
This highlighted several areas where we have had to adopt a ‘do things differently’ attitude and move away from the traditional way of attending the supplier works’ to confirm the quality of the product.
We wanted to restart inspection whilst maintaining the safety of everyone involved. We need to maintain design intent through inspections and factory acceptance tests.
One of the first examples of this is testing stainless steel equipment. Luckily, it’s a visual process – if iron is present (meaning the steel isn’t quite up to standard), it reacts with potassium ferricyanide and goes blue.
The team worked with our Joint Venture team, with Joint Venture Quality Manager Shaun Lees helping to revise the existing process and approving documentation.
BEP Quality Manager Dave Tracey added:
The ferroxyl test was witnessed remotely using Microsoft Teams while interacting with the on-site inspector. We recorded the live streams, which means we have it available for assessment and auditing.
It worked brilliantly and we think it could be used for other inspections, such as manufacturing process steps, nondestructive tests, product and packaging, and marking.
Microsoft Teams is being rolled out across the organisation to help our employees stay connected during the crisis.